Mankind has been using moulds to manufacture ceramics for centuries. The precise origin of slip casting is still debated, with variations of the method observed in prehistoric Peruvian cultures and the ancient empires of the Mediterranean Sea. The French rather romantically coined the phrase coulage to describe the process of slip casting, which roughly translates as casting through shrinkage. This term is also associated with mass production, which is why the discovery of the technique is often dated centuries after indigenous peoples in Peru first used slip casting to construct simple panpipes.
Read More: Introduction to Sialon Ceramics
The process remains remarkably similar today but slip casting of technical ceramics such as SiAlONs requires stringent considerations to satisfy the mass production capabilities of the technique. This blog post will explore slip casting and the difficulties that SiAlONs represent to this established technique.
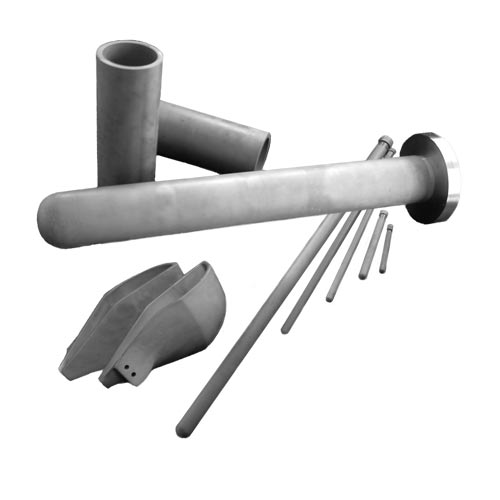
How Does Slip Casting Work?
The precise method of slip casting involves a simple porous mould that is typically made from plaster. This enclosure is used to consolidate small to medium volumes of an aqueous slip and form green bodies with near net shapes to reduce or eliminate the need for surface finishing and machining.
An aqueous slip is a slurry comprised of water, an organic dispersant, and a blend of ceramic powder materials. These components are milled together to create a heterogenous mixture with highly-uniform solid particle dispersion throughout the water. The dispersing agent ensures that the ceramic particles do not flocculate.
The slip is then poured into the plaster mould at room temperature. Water is drawn from the slurry through the capillary action of the plaster’s porous structure, which causes deposition of ceramic particles on the inside of the mould. Manufacturers monitor the gradual swelling of the cast to assess the levels of slip moisture loss and particle deposition. When the cast has grown to a required thickness, the slip is drained from a valve or opening in the mould and the ceramic component is removed from the plaster cast.
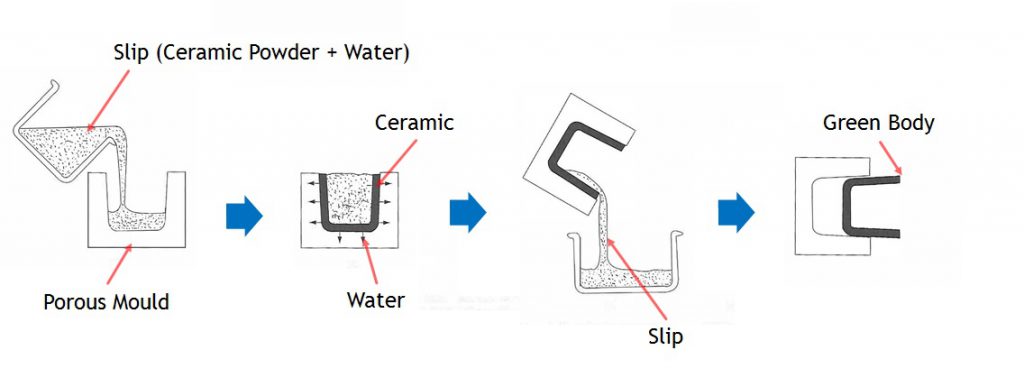
Problems with Slip Casting SiAlONs
Some of the problems with slip casting are that it is conventionally used for traditional ceramic materials, such as porcelain, and is more difficult for engineering ceramics such as SiAlONs. This is due to the surface chemistry of the different oxide and nitride based ceramic materials which are required to promote densification during a liquid phase sintering. SiAlON aqueous slips must, therefore, be accurately characterised to determine the colloidal properties of the raw material and the anti-flocculating characteristics of the dispersing agent. Also, all of the water must be removed from the green body prior to sintering, which is a very sensitive process as the green parts can be extremely fragile.
Slip Cast SiAlON Products
Despite these difficulties, slip casting has been used to manufacture advanced SiAlON shapes for demanding thermomechanical applications. At International Syalons, we have engineered SiAlON thermocouple sheaths and riser and heater tubes using slip casting techniques.
If you would like to learn more, read our article on Design Tips for Silicon Nitride Ceramics.
SiAlON Solutions with International Syalons
International Syalons has spent decades researching and developing advanced ceramic materials for an array of applications. We have provided a robust range of SiAlON ceramics that are tailored for unique manufacturing requirements, allowing for additive manufacturing, electro-discharge profiling, and slip casting of SiAlON ceramics.
If you would like any more information about our SiAlON ceramics, please do not hesitate to contact us.