The chemical and process industry is concerned with converting raw materials into semi-finished or finished products via thermochemical reactions. This covers an extensive range of industrial and commercial processes, including petroleum metering and petrochemical production of organic and inorganic polymers. Chemical and process industries are typified by chemical reactions of highly corrosive or erosive media at ambient or elevated temperatures.
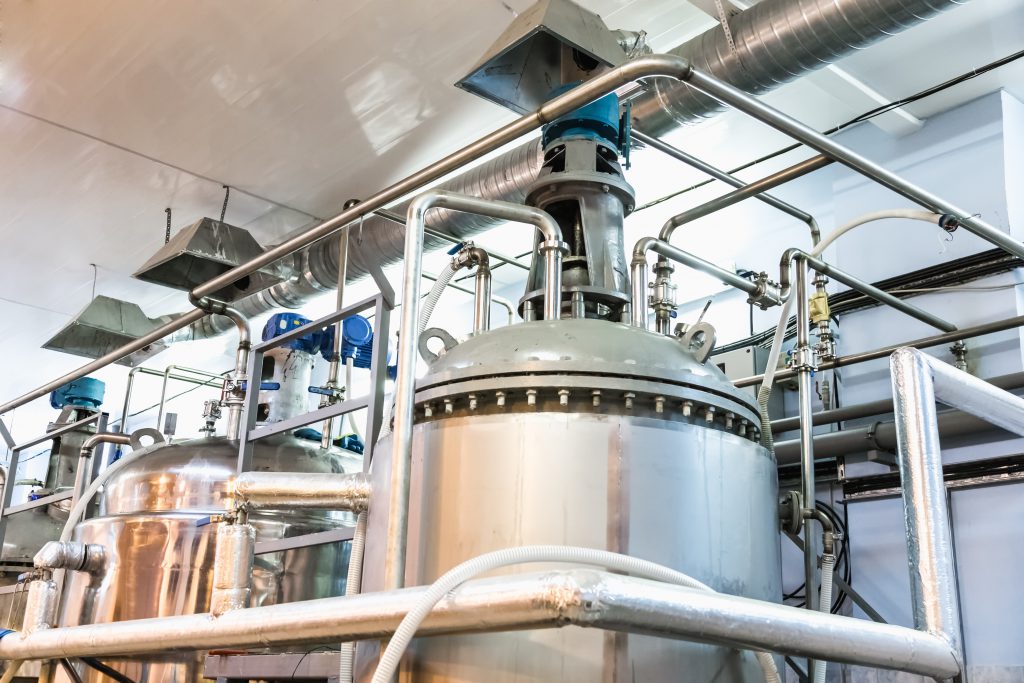
Silicon nitride (Si3N4) has played a significant functional role in enhancing the capacities of components in the chemical and process industry. Seals and tubes manufactured from advanced Si3N4 represent outstanding resistance to chemical corrosion due to their unique physiochemical characteristics.
This blog post will explore some key Si3N4 applications in the chemical and process industry in further detail.
The Advantages of Si3N4 for CPIs
Si3N4 is an advanced ceramic material engineered to be isostructural with one of the three phases of silicon nitride. The novel arrangement of silicon (Si) and nitrogen (N) atoms supplemented with aluminum (Al), oxygen (O), as used in sialon (Si-Al-O-N) ceramics which can be thought of as an ‘alloy’ of silicon nitride, has provided novel avenues for manufacturing hard-wearing, chemically inert components for the most demanding chemical and processing conditions.
Read More: What are Sialon Ceramics?
Beta- (β-) and mixed alpha-beta- (α:β-) Si3N4 are routinely used to fabricate seals and tubes for the chemical and process industry due to their enhanced chemical integrity in the presence of acidic or alkaline solutions, and excellent physical resistances to particle abrasion for handling slurries of high solid contents.
Si3N4 Chemical Seals
Mechanical seals in chemical and processing industries are commonly used to prevent leaks from pumping and compressing equipment. These moving parts use severe agitation to generate or maintain optimal reaction conditions within the processing environment. Yet this method introduces an additional erosive element to the system in the form of friction. Inferior seals may gradually degrade due to the combined properties of exterior mechanical erosion and interior corrosion from heated chemicals.
Syalon 101 is a β-Si3N4 that is routinely used to manufacture hard seals for moving components in chemical and processing environments. It boasts outstanding wear-resistant characteristics due to a low coefficient of friction, extremely high hardness, and exceptional strength values. These properties are coupled with inherently high chemical integrity, representing negligent reactivity with a range of common acids and alkalis at boiling temperatures and high concentrations.
Si3N4 Chemical Tubes
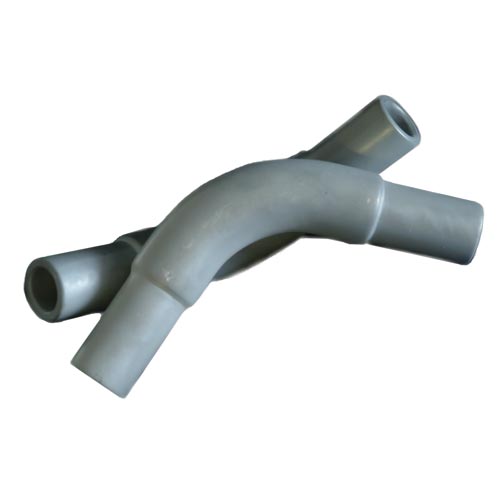
Transporting highly corrosive chemicals through a processing facility can be extremely complex, requiring high-stability pipework that can maintain its chemical resistivity over extended periods of operation. This can be challenging for conventional materials such as Inconel, one of the primary nickel-chromium metal alloys used for manufacturing chemical pipes.
Syalon 101 tubes display significantly improved physiochemical integrity over time, with sustained resistance to chemical attack by solutions or slurries of highly acidic or alkali concentrations. The chemical properties of Syalon 101 are surpassed only by Syalon 050, a unique mixed-phase Si3N4 that was engineered for superior wear properties and corrosion resistance.
Si3N4 from International Syalons
International Syalons is one of the world’s leading manufacturers and suppliers of ceramic solutions for the most demanding chemical and process industry requirements. Our Si3N4 product range for handling highly corrosive and erosive media includes seals, tubes, hydro cyclones, and impellers.
If you would like any more information about our Si3N4 materials, simply contact us.