A car engine block can weigh anything from 90 kilograms (kg) to over half a tonne without its associated parts, such as the power train or other directly connected components. The weight of the vehicle is one of the defining factors in its overall performance and efficiency, and reducing the weight profiles of integral components has been an ongoing challenge for advanced engineering of modern vehicles.
Limiting the use of high-density metals was one of the immediate solutions to this problem. Engine and gear box casings are now increasingly built using cast aluminium (Al) or alternative lightweight alloys as opposed to comparatively heavy cast iron (Fe). Typically, these must be coated with functional metals to achieve the desired mechanical properties. Bronze (CuSn) is ideal for spray coating lightweight engine components as it imparts exceptional wear resistance, enabling advanced engineering of lightweight, high-performance vehicles.
Advanced Engineering and Surface Preparation
To ensure optimal bonding between a coating medium and the surface of a gear box casing, shot blasting is used to modify the surface topography of the base metal and enhance good bonding is achieved. The problems of shot blasting are well-documented, however. Gradual degradation of shot blast nozzles represents an ongoing maintenance concern, particularly when using highly abrasive particles like aluminium oxide (Al2O3). These extremely fine and hard-wearing microparticles can abrade the extrusion component of the shot blaster, causing eventual component failure.
Advanced engineering of materials for wear applications has yielded a range of mechanically-stable ceramics capable of resisting the regular abrasion of highly-pressurised alumina particles. Two of the frontrunners are tungsten carbide (WC) and Syalon 050, a proprietary silicon nitride-based (Si3N4) derivative that has been optimised for superior erosion resistant behaviour.
Read More: Sialon Shot Blast Nozzles for Industrial Wear Applications
Tungsten carbide is one of the most established materials for advanced engineering of shot blast nozzles, but International Syalons has demonstrated the superiority of Syalon 050 for wear applications.
Syalon 050 vs Tungsten Carbide
Tungsten carbide is incredibly tough, displaying hardness ratings of up to 36000 MPa and a maximum fracture toughness of 3.8 MPa. This is due to its microstructural arrangement of high strength carbide grains. However, these grains are cemented together by pliable cobalt molecules which are susceptible to fine particle abrasion. Under test conditions, shot blast nozzles manufactured from tungsten carbide lasted just 20-25 hours before a replacement was required.
By comparison, Syalon 050 shot blast nozzles continued to perform after 814 hours under the same operating conditions. The component showed no signs of wear after testing was completed and are still in operation at the time of writing. On this occasion it translated to annual savings of over £6,500 per machine, with a single Syalon 050 nozzle outlasting as many as 41 tungsten carbide alternatives. The advantages of using silicon nitride shot blast nozzles are subsequently evident.
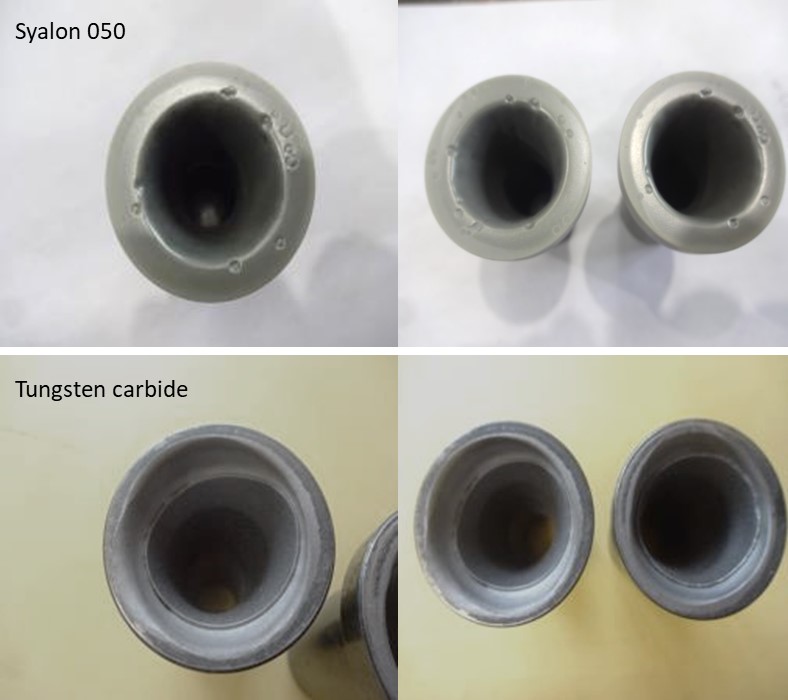
Syalon 050 nozzles showing no signs of internal bore wear after 647 hours of use.
Advanced Engineering with International Syalons
International Syalons is dedicated to advanced engineering of ceramics to help customers achieve novel solutions to ongoing industry challenges. In this instance, our customer identified their tungsten carbide shot blast nozzles as a potential cost savings area and we applied our unique experience of advanced engineering to provide replacements using Syalon 050. We are currently conducting another study to determine if our customer can reduce the cost of nozzle consumables by 60—70%.
Or, if you have any specific questions about using our advanced engineering experience for your application, simply contact us directly.
[Source: Azom]
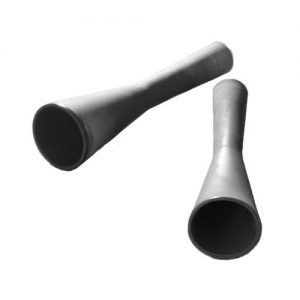