International Syalons are pleased to announce the availability of Zircalon 30 a new grade of zirconia-based advanced ceramic with greatly improved fracture toughness, which is ideal for induction welding applications.
Zirconia, also known as zirconium dioxide (ZrO2), is a high-strength advanced ceramic with outstanding impact- and wear-resistant properties. It is usually present in one of three distinct crystal microstructures that are dependent upon forming temperatures and the presence of dopants and stabilizers such as cerium (Ce) or yttrium oxide (Y2O3); each of which is believed to impart different mechanical characteristics.Typically, yttrium-doped zirconia ceramics reach higher compressive strength values (>2000MPa) while cerium imparts greater fracture toughness[1]. Zircalon 30 is a new grade of zirconia that has demonstrated outstanding levels of performance for fracture-resistant control pins in weld assemblies.
Introducing Zircalon 30 – A New Zirconia Ceramic
Zircalon 30 is a co-stabilised zirconia and aluminum oxide (Al2O3) matrix based composite ceramic, which is reinforced by self-grown alumina-based platelets. This microstructure achieves the same mechanical benefits of zirconia ceramics stabilized with yttrium additives albeit with vastly improved fracture toughness in the region of 14 – 15MPa m½. Zircalon 30 also boasts an increase in impact resistance of up to 50% compared to yttrium-stabilized zirconia (YSZ).
Zircalon 30 is a new grade of zirconia which has been developed for industries and applications requiring exceptional wear resistant characteristics for electrically-insulating materials. It is predominantly used in metal forming and welding applications, chiefly as non-conductive weld location and control pins.
Owing to the outstanding strain-resistant properties and good biocompatibility of YSZ, this advanced ceramic has seen significant growth within the dental and orthopedic sector. Currently, zirconia-based cores for fixed partial dentures on anterior and posterior teeth are challenging titanium as the primary material of choice for oral implantology[2]. Its commercial viability as a suitable material for hip head prostheses is still under clinical evaluation, with further studies exploring the biological and mechanical capacities of novel zirconia implants[3].
Issues with Established Weld Pin Materials
Control pins for welding assemblies are used to secure sheet metal and additional components, such as nuts, in place throughout the welding process. This operation is typically carried out by feeding the location pin through a preformed aperture in the sheet. The nut is then centered around the pin by the force of gravity and the welding assembly fuses the nut to the sheet by introducing a voltage differential between the upper and lower domains of the welding unit – after which, the non-conductive control pin can be easily retracted.

Steel control pins are problematic as the material’s electrical conductivity can cause arcing between the product, the workpiece, and the pin itself. This can cause a build-up of slag material on the pin which may inhibit the retraction process. They are also susceptible to metal contamination and weld corrosion, known as pitting, which results as a visible porosity that gradually renders the component inoperable. Corroded control pins must be replaced, resulting in loss of production and avoidable maintenance costs[4].
Technical ceramics have become the prevalent material for fabricating weld location pins, with demonstrable improvements in terms of ongoing operating performance. A major European automotive manufacturer determined the lifespan of their steel location pins at approximately 70,000 operations before irreversible failure. By comparison, control pins manufactured using Syalon 101, an innovative silicon nitride (Si3N4) derivative, performed over 7 million operation cycles without exhibiting noticeable wear or reduced functionality[5]. Subsequently, Syalon 101 weld control pins are among the primary components used in metal forming applications.
The Emergence of Zirconia Weld Pins
The emergence of zirconia ceramics in engineering spaces such as metal forming is attributed to the complex and demanding mechanical conditions of high-throughput processing. Occasionally weld location pins fabricated from zirconia products are preferable to silicon nitride in facilities where high impacting forces are a factor in the long-term performance of the weld assembly.
Zircalon 30 is poised to improve upon the established benefits of existing zirconia-based control pins, with comprehensively enhanced mechanical performance characteristics. Already, Zircalon 30 control pins are outperforming products manufactured from Zircalon 10 – which previously set the benchmark for strength and toughness properties of zirconia. It also exceeds the thermal transfer coefficient of 2.5 W/(mK) established by Zircalon 20 – a magnesia-stabilized zirconia (MgSZ) engineered for improved thermal performance.
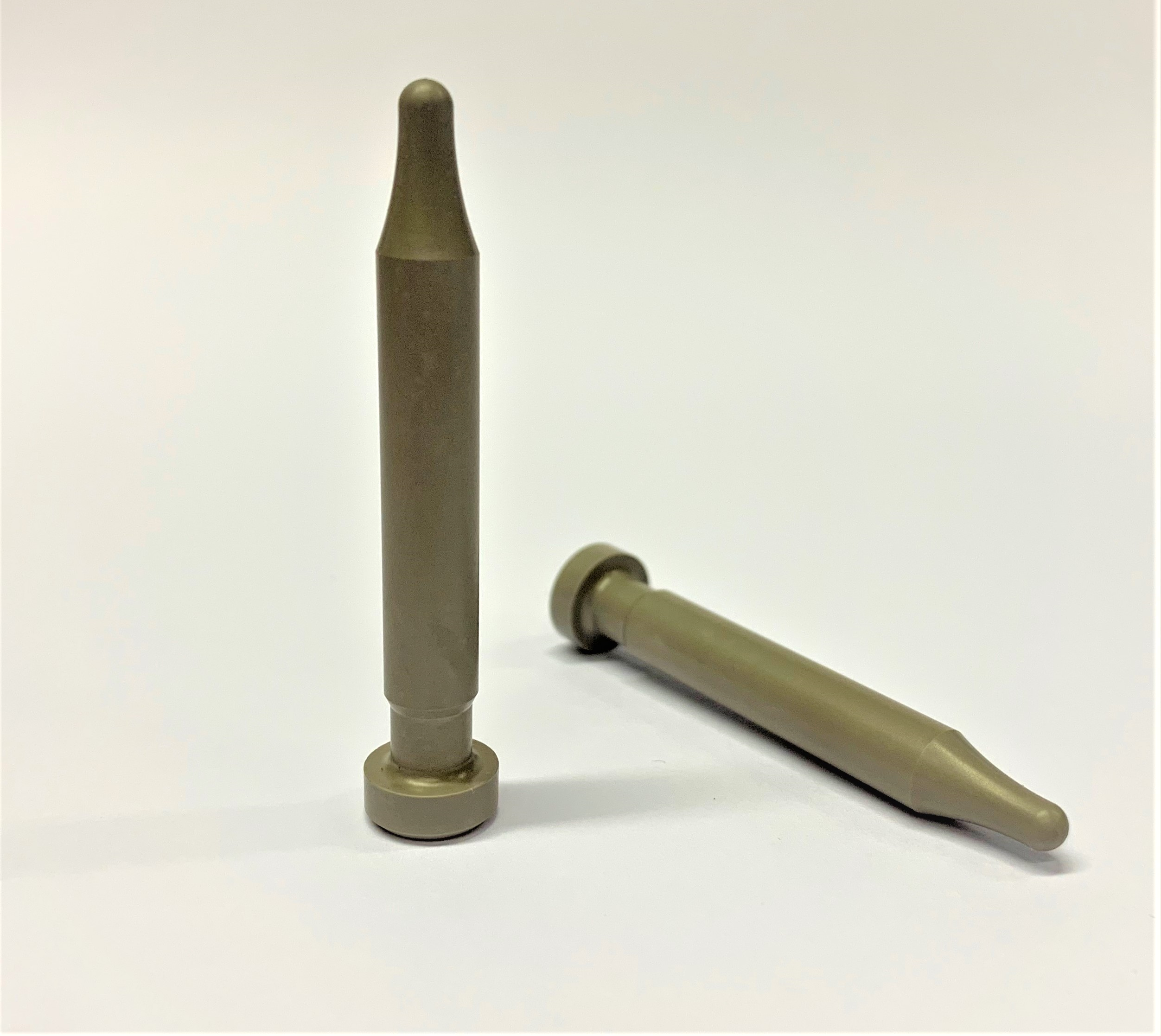
The operating conditions in a weld assembly are extreme, comprising peak flame impingement temperatures of 3,500°C (6,500°F), elevated ambient temperatures, and potentially hazardous agents such as ionized gases and particles. Control pins engineered from Zircalon 30 can reliably perform high-throughput welding operations with substantially increased resistance to fracture caused by unavoidable impacts while lining up the sheet metal aperture, placing the nut on the pin, or retracting the component from the end-product. Zircalon 30 is also anticipated to advance the performance of additional fixtures and jigs in other types of welding assembly.
The table below lists typical mechanical, thermal and electrical property data for Zircalon 30.
Physical property data for Zircalon 30
Property | Value | Units |
---|---|---|
Composition | ZrO2-Al2O3 | – |
Density | >5.62 | g/cc |
Porosity | 0 | % |
3 point Modulus of Rupture 20°C (Specimen 3 × 3 × 50mm, span 19.05mm) | 1000 | MPa |
Weibull Modulus | 14 | – |
Compressive Strength | >2000 | MPa |
Young’s Modulus of Elasticity | – | GPa |
Poisson’s Ratio | 0.295 | – |
Hardness (HRA) | 89 | – |
Hardness (Vickers HV50) | 12.13 | GPa |
Fracture Toughness K1C | 14-15 | MPa m½ |
Thermal Expansion Coefficient (0-1200°C) | 10.1 x 10-6 | K-1 |
Thermal Conductivity | 3.5 | W/m/K |
Thermal Shock Resistance | – | ΔT°C quenched in cold water |
Maximum Use Temperature | 1000 | °C |
RT Electrical Resistivity | 1013 | ohm cm |
Typical physical property data obtained under test conditions. All properties have been measured by independent testing authorities. The values given only apply to the test bodies on which they were determined, and therefore can only be recommended values. See our disclaimer.
Download the Zircalon 30 Property Data Sheet PDF (0.09 Mb).
Sources:
[1] http://huysindustries.com/wp-content/uploads/huysarticle08-Non-Conductive_Welding_Pins_Based_on_Zirconia_Ceramics.pdf
[2] https://www.ncbi.nlm.nih.gov/pubmed/28000266
[3] https://www.sciencedirect.com/science/article/pii/S0300571207001418
[4] https://patents.google.com/patent/US5248869A/en
[5] https://www.azom.com/article.aspx?ArticleID=11578