As part of the European Commission funded Horizon 2020 project ToMax, International Syalons in collaboration with European partners has demonstrated the unique capabilities of lithographic-additive manufacturing (L-AMT) of ceramic materials including Syalon 101.
How are Ceramics Printed?
Additive manufacturing, or 3D printing, has been on the rise since the early 1980s yet it is still considered an immature technology. The first iterations used photo-hardening of thermoset polymers to generate three-dimensional models via masking or fiber scanning. There are now a myriad of techniques available to generate components via deposition as opposed to conventional machining, yet 3D printing is still generally used for rapid prototyping and hobbyist applications. Important examples include binder jetting and injection molding.
Significant investment has been made in industrial spaces to help realize the commerciality of additive manufacturing at appropriate scales, particularly for technical ceramic materials.
Syalon 101 is one of our most popular grades of silicon nitride-based ceramic (Si3N4). Historically, technical ceramic materials like Syalon 101 proved impossible to manufacture at small scales and intricate geometries in a cost-effective manner, due to the limitations of conventional iso-static pressing and machining, or the expensive molds were required to shape the ceramic materials via injection moulding, with little or no guarantee of success.
L-AMT Syalon 101 has changed that; representing the exciting potential for the future of 3D printed ceramic materials.
3. Unparalleled Design Intricacy
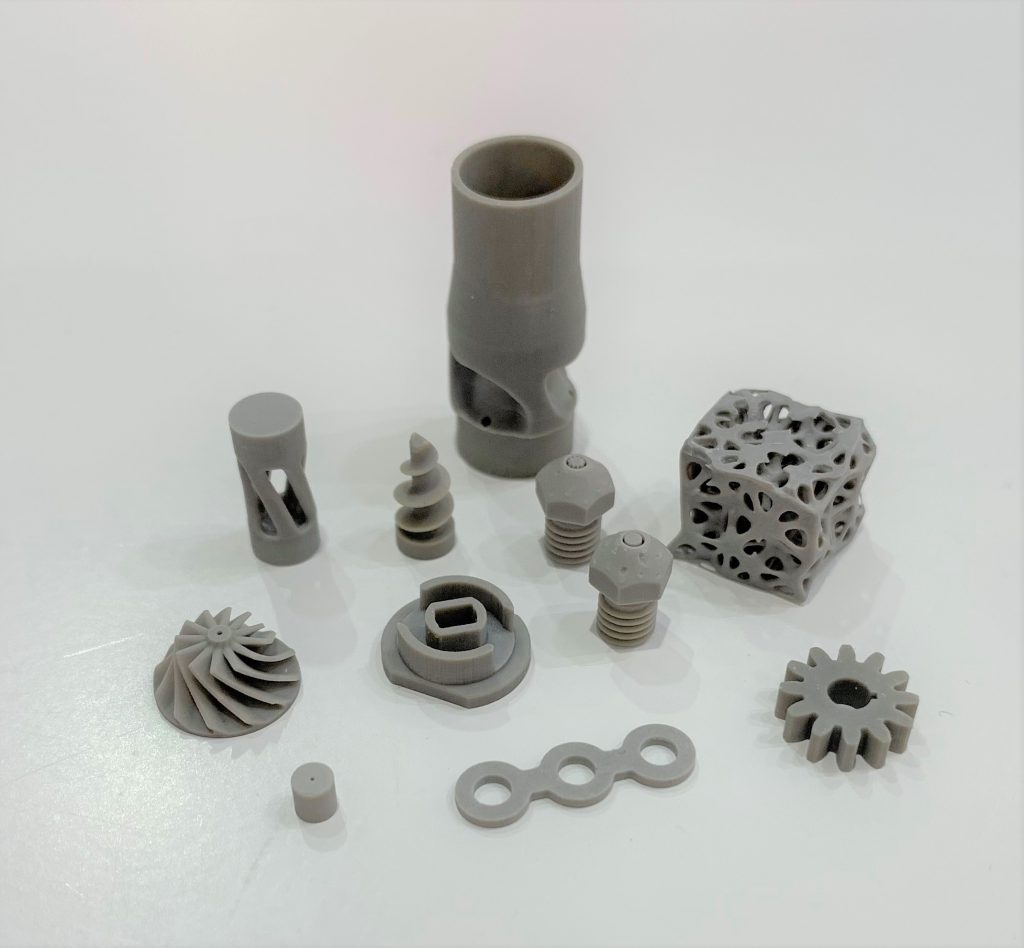
Lithographic 3D printing uses a high powered precision light source to cure the desired cross-sections of a photocurable resin containing ceramic particles layer by layer to create a complex green body in the absence of a mold. This provides unparalleled design intricacy for ceramic materials. International Syalons has successfully generated prototypical impellers on millimeter scale proportions with excellent surface finishes and dimensional tolerances.
2. Comparable Performance to Bulk Materials
This intricacy does not simply satisfy engineering curiosity; it is designed to function in real-world environments to prove the concept of L-AMT. Prototype ceramic materials can be printed with extreme precision at a fraction of the cost of high-volume commercial production runs. Conventionally, 3D printed prototype ceramics were associated with a commensurate drop in yield strength and hardness, due to sintering challenges. This drawback has now been overcome, especially for small components.
L-AMT Syalon 101 now possesses near-identical thermomechanical properties to conventionally iso-static pressed material, with a hardness of 1500 HV10 and exceptional strength properties.
1. Faster Manufacturing
This level of precision and quality is succeeded only by the speed of manufacturing. 3D printing eliminates the need for complex molds and significantly reduces finishing times for topographical variations, particularly for precision ceramic materials where small surface features could limit device performance.
Printed Ceramic Materials from International Syalons
International Syalons is a world leader in ceramic engineering, and a pioneer in 3D printing of advanced ceramic materials. We explored the background of L-AMT in a previous post: Introducing Additive Manufacturing for Silicon Nitride Ceramics and will continue to share 3D printing of ceramic’s latest developments as this proprietary technology continues to grow.
Otherwise, contact us directly for more questions about our ceramic materials.