Armed with innovative 3D printing technologies, engineers have designed a new generation of microturbines capable of unparalleled operating efficiency at higher speeds and elevated temperatures.
What are Microturbines Used for?
Microturbines are relatively simple gas turbines that comprise a compressor, combustor, turbine and electric generator on a single or double shaft – which rotates at 90,000-120,000 rpm. This design simplicity enables microturbines to generate between 25-500 kW. .
One of the major benefits of microturbine generators compared with conventional piston engines is that they have fewer moving parts, sometimes as little as a single component. While microturbines are generally less efficient at lower power levels, their overall power-to-weight ratio and temperature recuperation systems are attractive for applications where cogeneration of electricity and heat are required and/or space is limited.
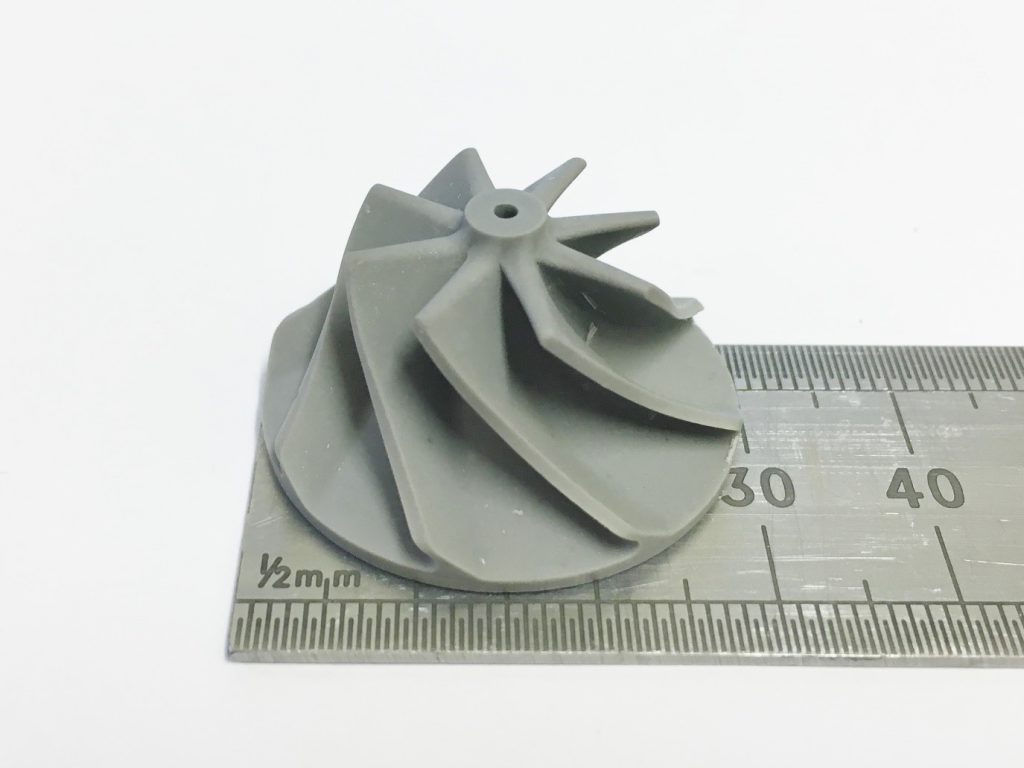
The most common modern applications for microturbines are for ultra-light unmanned aircraft and regeneration systems in hybrid vehicles. However, some of the most exciting development projects are focussed on millimetre sized turbine engines, with hopes of impellers smaller than 20 mm diameter generating up to 1500 W.
How Can Sialons Improve Microturbines?
Silicon nitride-based sialon (Si-Al-O-N) ceramics have been an attractive material for microturbine impeller manufacturing for years, thanks to their outstanding strength and exceptional temperature oxidation resistance. Due to the high strength covalent atomic bonding between silicon and nitrogen, sialon ceramics can maintain their strength and creep resistance for operation at temperatures over 1000°C.
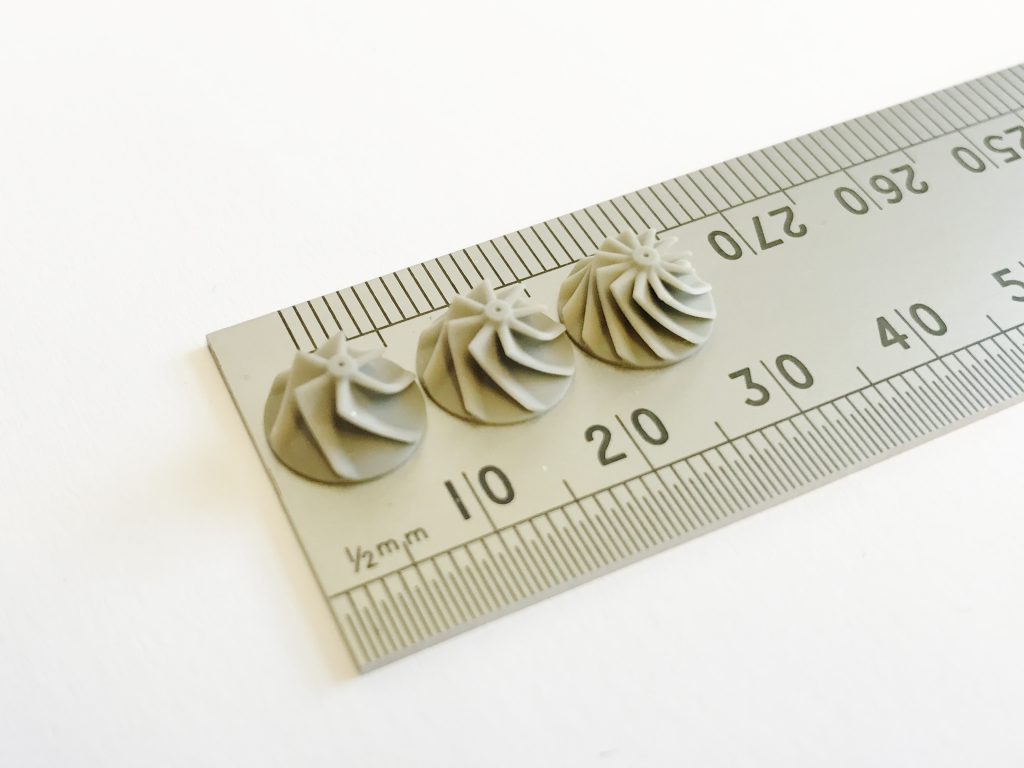
In addition to these high temperature capabilities, sialons’ lower material density of 3.25 g/cm3 compared with >8.0 g/cm3 of most Inconel alloys enables much faster rotational acceleration and deceleration. This means impellers can reach optimum speeds faster allowing them to react quicker to demand requirements without maintaining high idle speeds.
How Can 3D Printing Improve Microturbines?
The latest lithographic additive manufacturing technology (L-AMT) facilitates the production and design of complex-shaped sialon components. Previously, intricate components were impossible to produce using sialons due to the limitations of conventional machining methods. L-AMT of sialons not only enables rapid manufacturing of complicated profiles, it also, significantly reduces the cost of development. Prototyping with L-AMT allows engineers to optimise microturbine performance through multiple phases of design refinement at comparatively low costs to the expensive tooling necessary for injection moulding of sialons.
Read a Quick Intro to Additive Manufacturing Ceramic Solutions
L-AMT Syalon 101 offers the same thermomechanical properties as conventionally iso-pressed and machined ceramic. Thanks to carefully developed thermal processing, L-AMT Syalon 101 offers a hardness of 1500 HV10, 3-point bend strength of > 900 MPa, and operating temperatures up to 1200°C in corrosive and high abrasion environments.
Ceramic Solutions from International Syalons
International Syalons is the UK’s foremost supplier of ceramic solutions for industrial areas of application. We have successfully utilised lithographic additive manufacturing to generate bespoke components, such as extremely small-scale silicon nitride impellers. These ceramic solutions exhibit outstanding mechanical properties that surpass alternative 3D printing methods currently used to generate ceramic shapes.
If you would like to learn more about lithographic ceramic solutions, please do not hesitate to contact a member of our team.