Silicon nitride ceramics (Si3N4) occupy a storied niche in the history of engineering materials, rising from relative obscurity in the early days of the industrial era to become one of the most important technical-grade ceramics available today. Since their renaissance in the early 1970s, silicon nitride ceramics have successfully replaced numerous legacy materials as the advanced ceramic of choice for various high-performance components. These include:
- Weld Rolls and Extrusion Dies: With high hardness (<19.81 GPa) and toughness properties, silicon nitride ceramics display outstanding durability and mechanical stability in response to continuous wearing forces.
- Weld Location Pins and Fixtures: All the above properties and the improved machinability of select silicon nitride grades combine to make the alloy applicable for use in weld location assemblies for various joinery techniques.
- Molten Metal Handling Equipment: Silicon nitrides boast outstanding stability in response to thermal shock (<Δ900°C) and in the presence of abrasive and corrosive elements, suiting it to integration into crucibles, furnaces, and molten metal extrusion dies.
- Cutting Tools: These inherent wear-resistant properties combine with exceptional fracture toughness (<7.7 MPa m½) characteristics to meet the demands of high-throughput industrial cutting tools.
However, simply replacing components that were originally metal or an alternative refractory with silicon nitride ceramics is often not the ideal solution – even though silicon nitride ceramics largely outperform metals and refractories on numerous fronts. Successfully adopting replacement ceramics requires careful consideration of several important factors.
Read More: Benefits of Silicon Nitride Welding & Forming Rollers
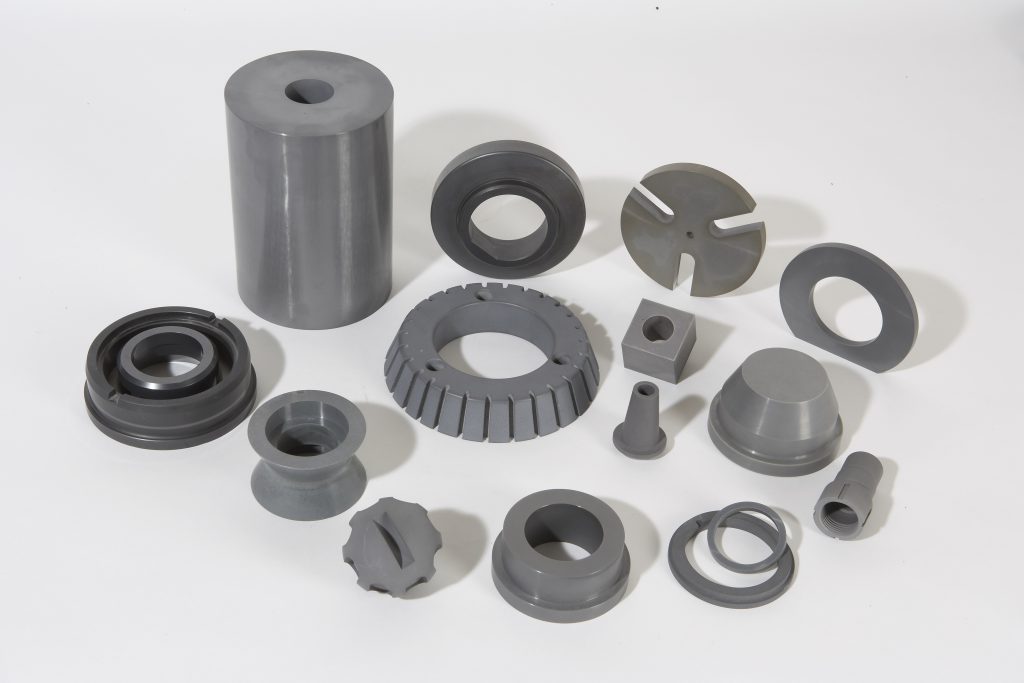
6 Design Tips for Silicon Nitride Ceramics
- Tolerance dimensions as loosely as possible: Where silicon nitride ceramics can be toleranced within 1-3%, net and near-net shapes can typically be manufactured as-sintered. This mitigates the need for costly post-processing and machining.
- Reduce component thickness: Silicon nitride ceramics are inherently strong, but the strength of parts is limited by the scale of its biggest flaw. Thicker components are more likely to display larger faults which can propagate and cause fracture. Owing to the improved strength, thin silicon nitride ceramic plates can usually outperform conventional materials with much thicker geometries.
- Avoid features that cause stress concentrations: Abrupt changes in the cross-sectional area or minute contact points can cause stress concentrations in silicon nitride ceramics. Consider relieving sharp edges and corners with chamfers, radii, and undercuts while large contact areas should be used to spread loading forces. Also, aim for uniform thicknesses across a full part.
- Utilise simple component forms: Silicon nitride ceramics can shrink by as much as 30% during the sintering process, making intricate geometries difficult to fabricate. Keep the component form simple to retain the tightest possible tolerances.
- Avoid unnecessary machining: Diamond grinding can impart extremely high stress concentration in silicon nitride ceramics. Producing components as-sintered or optimising the grinding parameters can reduce the risk of premature failure due to mechanically-induced stress.
- Consider modular designs: Silicon nitride ceramics support high modularity and can be incorporated into a composite design using a technique like shrink-fitting or joining with adhesive bonding agents.
Silicon Nitride Ceramics from International Syalons
International Syalons hopes this post has given you some useful insights into the complexities and benefits of designing with silicon nitride ceramics. It can provide value-added solutions to experts in a range of professions and demanding industrial sectors.
If you would like to learn more about the markets silicon nitrides have already been successfully implemented into, read our previous blog post Using Si3N4 in the Chemical and Process Industry
Otherwise, contact us directly if you have any design queries.