There are a myriad of different welding methods available today, such as metal inert or metal active gas (MIG/MAG) welding, high-frequency electric resistance welding (HF-ERW), shielded metal arc welding (SMAW), and many more. Technical ceramics can be used in tandem with practically any welding type, but they are typically restricted to high-value industrial processes due to their relatively high costs.
In this blog post, we will explore the different technical ceramics available for welding applications in more detail.
Introduction to Welding
Welding is an age-old method of fusing two or more metal workpieces together using extremely high processing temperatures, pressure, or a combination of the two. Although many welding processes can be carried out in rugged environments (scrapyards, workshops, etc.), the underlying mechanism is deceptively sophisticated.
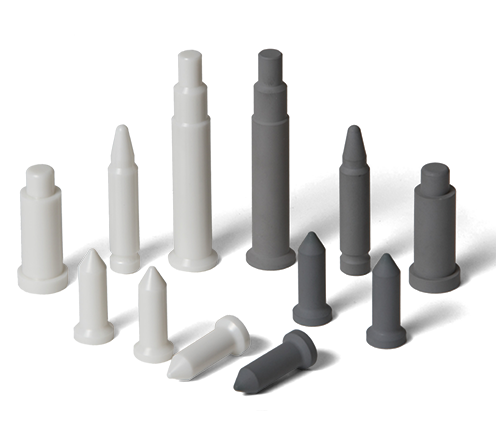
Joining occurs at the atomic level to produce bonds that can exceed the strength of the base metal with significantly reduced stress concentration effects. However, this is largely dependent on the type of joint used (butt, corner, edge, lap, or tee), the composition of the workpiece, and that of the electrode. Above all, however, the success of a welded seam or spot depends on the quality of the welding process: This is where technical ceramics come into play.
Technical Ceramics: Welding Fixtures, Pins & Rollers
Industrial welding processes have stricter demands than small-scale workshops regarding throughput, precision, and overall quality. They are also associated with more complex welding processes (i.e. tube welding).
To reach the required levels of quality assurance and control (QA/QC) mandated by industrial standards, welding operators often utilize additional fixtures and conveyors, comprised of technical ceramics, which eliminate the margin for human error. The likes of welding pins are used to hold workpieces in place while a joint is formed. We explored the basics of weld location pins in a recent article, with a focus on the different technical ceramics used to make ceramic welding pins.
Jigs and rollers can manipulate the position of components in situ for more demanding welding processes (i.e. orbital welding and HF-ERW). The challenge therein is producing components that can withstand the challenging conditions of the process itself, where temperatures may exceed 3,500°C (6,500°F) and where harsh abrasive forces are a routine factor. Retooling costs in welding applications where technical ceramics are not used are subsequently very high.
Read More: Benefits of Silicon Nitride Welding & Forming Rollers
The technical ceramics most commonly used in welding applications are silicon nitride (Si3N4), and zirconia (ZrO). Aluminum oxide, or alumina (Al2O3), may be used in welding tubes for MIG/MAG systems, but it cannot provide the toughness and outstanding thermal properties of the other two technical ceramics. In fact, silicon nitride tungsten inert gas (TIG) welding nozzles have successfully outlasted alumina-based alternatives by a factor of 10:1.
Silicon nitride and zirconia provide unmatched material hardness and are routinely used to extend the service lives of welding process machines and to enhance the end-product quality of bonded workpieces.
Technical Ceramics from International Syalons
International Syalons specializes in the formation of high-density technical ceramics to provide value-added solutions for demanding industrial processes. We supply alumina, silicon nitride, and zirconia-based products for various welding applications.
If you would like more information about how International Syalons technical ceramic products can improve your welding process, simply contact a member of the team today. We are always happy to answer any questions.