Metal forming, like most of the metalworking and manufacturing chain, can be an extremely intensive process. It exploits the inherent plasticity of sheet metal to form net and near-net shapes via applied mechanical loads rather than gradual subtraction (cutting, grinding, etc.).
Though there are countless forming methods available to manufacturers today, each one typically falls under one of the following overarching categories: bending; compression; tension; combined compression and tension; or shear forming. Hard-wearing technical ceramics are ubiquitous in virtually every type of metal forming technique.
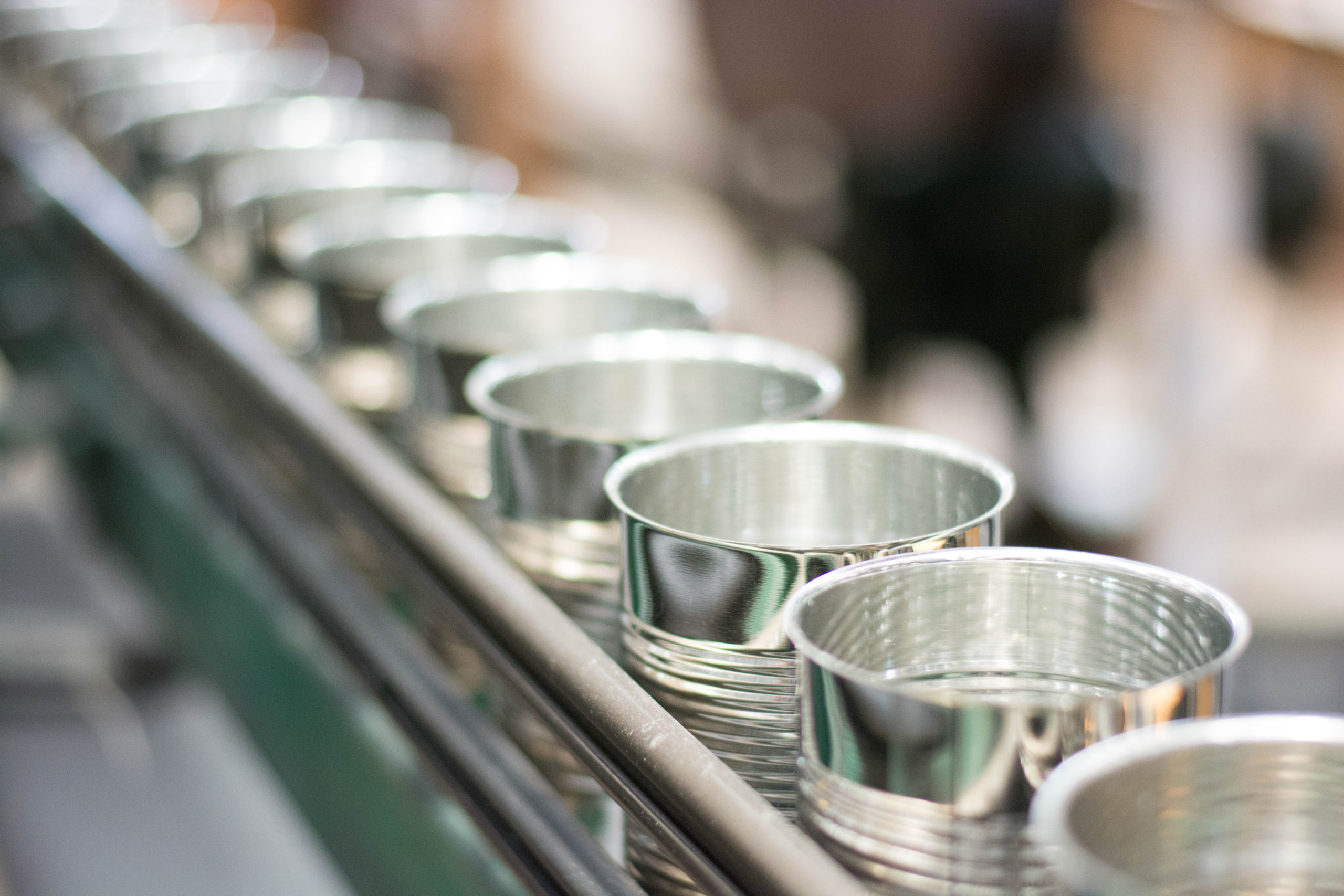
Why Use Technical Ceramics in Metal Forming?
Consider the manufacturing process for aluminum cans in the food and beverage industry. Circular blanks are cut from thinly rolled sheets and are then drawn upwards to form a hollow cylinder comprising the bottom and sides of the can. This is known as the initial draw.
A re-drawing process occurs next, where the partially formed blank is held in place by a sleeve as a pneumatic punch and a series of ironing rings apply pressure to increase the diameter and height of the cup by stretching the walls. This is done in a single motion that takes a fraction of a second.
All the forming tools used throughout this multi-step process are subjected to repeated high compressive stress and severe wearing forces during every single production cycle. This is compounded by the fact that metalworking processes are often continuous and high-throughput.
Wear-resistant technical ceramics are subsequently ideal for metal forming tools in the canning process. Two of the most common precision ceramics used in two-piece drawing and wall ironing are silicon nitride (Si3N4) and zirconia (ZrO2). These two technical ceramics are renowned for their impact-resistant properties, high strength, and toughness. They can be formatted in a range of configurations with extremely hard, smooth surfaces that mitigate friction between the tool and the workpiece throughout high-pressure forming. This translates to a higher quality finished part and longer tool integrity throughout intensive, continuous metal forming processes.
International Syalons: Technical Ceramics Suppliers
At International Syalons, we champion materials expertise and superior performance with a range of high-quality technical ceramics and precision parts. If you would like to speak with a member of the team about engineering unique canning tool parts using our Syalon range of silicon nitrides or Zircalon zirconia products, simply contact a member of the team today.
If you have found this article interesting, you may enjoy our Review of Light Metal Forming Techniques, which discusses die casting, extrusion, rolling, and more.