Technical ceramics often conjure impressions of heavy-duty industry, chemical processing, or aerospace and defence applications. But the odds are likely that you have several commodities in your kitchen that have been formed using specialised ceramic components. We are referring to food and beverage cans.
Can manufacturing is an intensive batch process where rolls of sheet metal are cut into blanks, pressed into hollow cylinders, and topped with a lid which is seamed and sealed once the can has been filled. Beverages are usually canned in aluminium while food goods are canned in lacquered steel. Each of these is produced in vast quantities year on year. Aluminium can manufacturers in the US turn out around 100 billion cans per annum, while the canned food market has reached an estimated market value of $105 billion in 2020.
This turnover is inherently reliant on technical ceramic tools capable of handling the extreme demands of high-throughput, large volume metal forming processes.
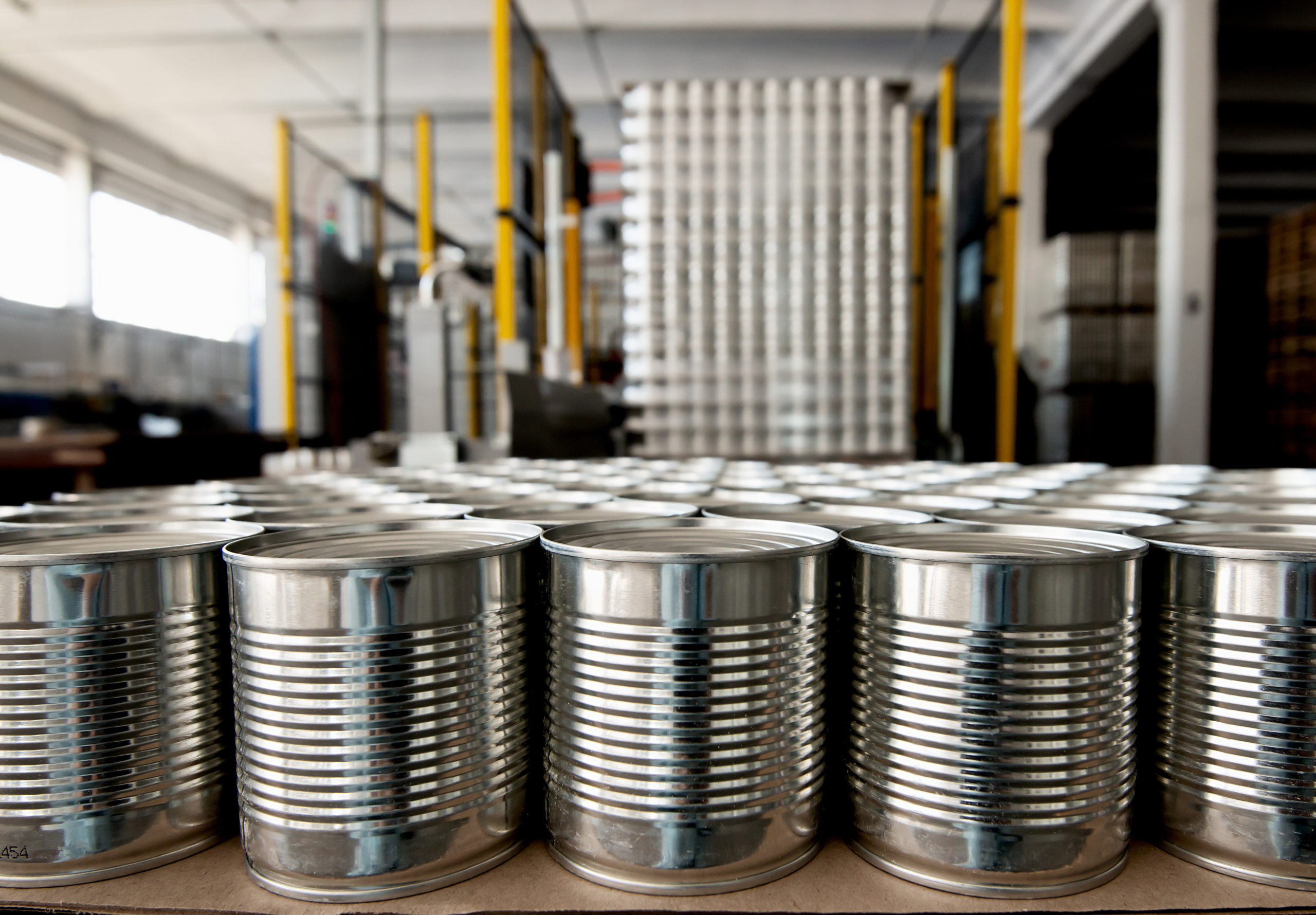
Challenges in Can Tooling
Though there are several methods available for producing both aluminium and steel cans, the most effective is the two-piece technique pioneered by CoorsTek in 1959. Sometimes referred to as the draw and wall iron method, the two-piece forming technique involves an automated cupping machine which cuts multiple cylindrical blanks from a roll of sheet metal.
These cups – or blanks – are transferred to a redrawing unit where they are held in place by a sleeve while a pneumatic press draws and irons the walls of the can so that its height increases as the wall thickness decreases. Hence the alternative name.
Wear-resistance is the first concern for metal forming tools in high-throughput canneries. Tool steel has historically been deployed in cupper tooling, body-maker punches, ironing rings, and various other critical components on intensive cannery lines. But their poor long-term durability poses a risk of rapid degradation and subsequent mandatory downtime for maintenance. Even a fairly low throughput can-filling line can operate at rates of up to 15,000 cans per hour, so any loss of productivity can represent a significant impact on end-production.
Tungsten carbide is the first technical ceramic that is preferred over steels in can forming. It can withstand continuous abrasion from sheet metal much better than steel, but – again – its long-term durability leaves something to be desired. Though tungsten carbide is exceptionally hard, specialised grades are usually required to ensure compatibility with necessary lubrication and to eliminate potentially hazardous cobalt leaching.
Silicon nitride technical ceramics are often preferable to tungsten carbide due to its comparable anti-abrasive qualities and superior corrosion-resistance. Cuppers and punches manufactured from silicon nitride derivatives benefit from a tight-knit intergranular microstructure with bonds that resist attack from most common caustic agents and acids, ensuring long-standing durability in cannery lines.
Zirconia, or zirconium dioxide, is perhaps the godfather of technical ceramics for can manufacturing. Chemically inert, extremely hard and with an unparalleled fracture toughness, zirconia technical ceramics represent an ideal material for hard-wearing components on high-throughput metal forming lines. They have the additional benefit of low coefficients of friction which is ideal for internal lacquer coated surfaces such as tin-coated food cans. Another inherent benefit of zirconia versus the likes of tungsten carbide is its reduced density. Zirconia tools weigh approximately three times less than their tungsten carbide alternatives, which translates to significant energy savings and greater processing efficiency.
Tungsten carbide (WC) | Zirconia (ZrO2) | |
Density (g/cm3) | 15.25-15.85 | 5.60-6.15 |
Flexural strength (MPa) | 480-820 | 900-1700 |
Fracture toughness (MPa.m1/2) | 2-3.8 | 7-15 |
Hardness (GPa) | 17-36 | 11.5-14 |
Max temp use (°C) | 1050 | 1500 |
Technical Ceramics from International Syalons
International Syalons is one of the UK’s leading suppliers of technical ceramics for industrial applications. If you would like more information about using our cutting-edge silicon nitrides or zirconia grades for can forming processes, simply contact a member of the team today.
If you have found this article interesting, you may enjoy our Review of Light Metal Forming Techniques, which discusses die casting, extrusion, rolling, and more.