Engineering ceramics occupy the cutting edge of industrial applications. They are deployed where conventional materials are prone to failure, or to refine equipment for greater throughput and profitability. Their incredibly favourable thermomechanical properties have made them a mainstay in metalworks and steel foundries for decades, where they generally offer long-lasting performance over multiple cycles—even when in direct contact with molten metals.
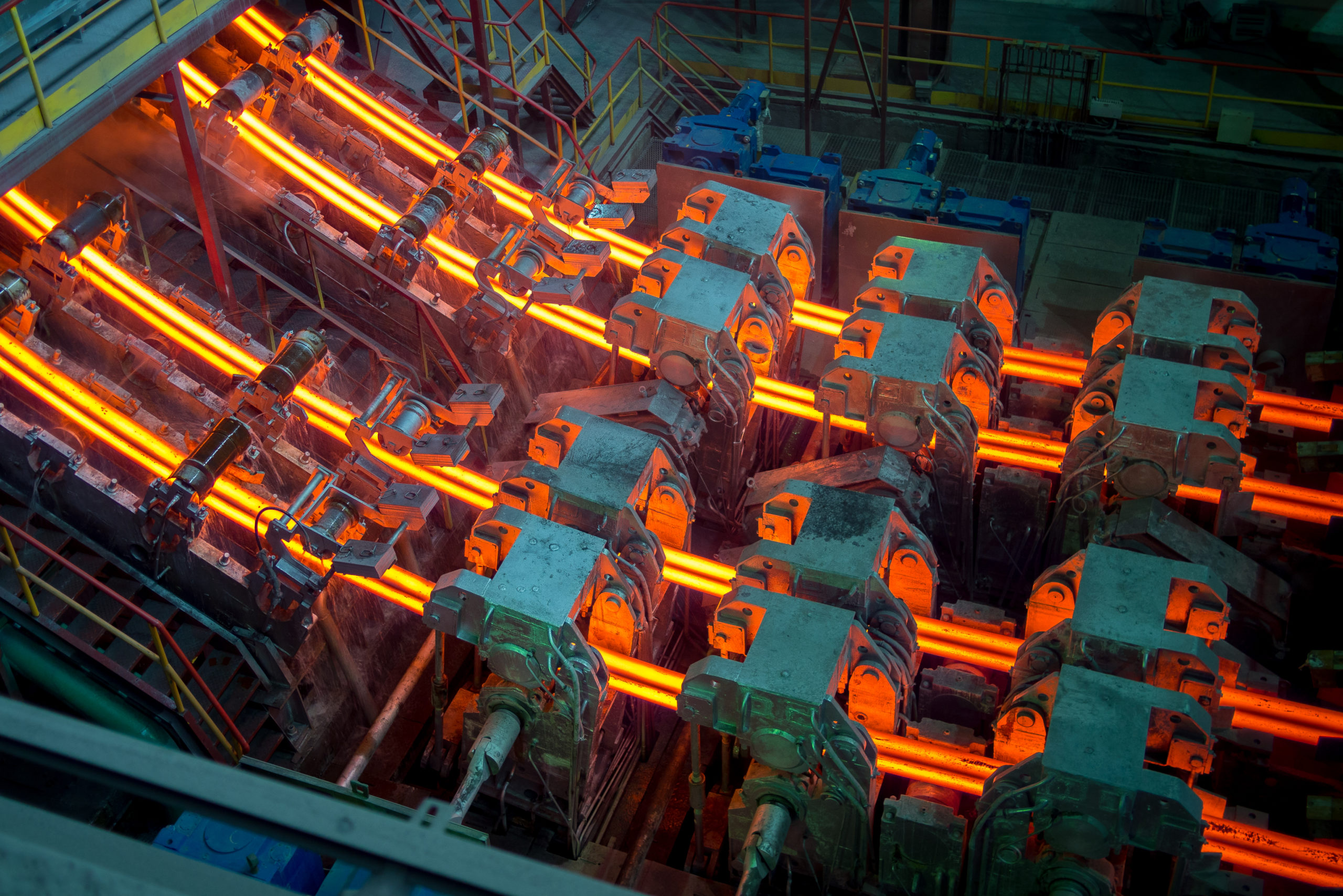
Image Credit: Shutterstock
At International Syalons, we have developed a suite of high-performance silicon nitride (Si3N4) technical grades, each designed to resolve key production pain points such as component failure induced by molten abrasion or thermal shock. Our solutions often surpass the performance of other, tried-and-trusted ceramic materials and tool steels in foundry applications. Syalon 110, for example, is a cost-effective alternative to well-established alpha-phase boron nitride (α-BN) and BN composites for break rings in horizontal continuous casting (HCC) of steel.
What is Continuous Steel Casting?
Continuous casting has been the leading method of generating semifinished billets from molten steel since the 1950s. The process involves tapping a furnace and treating the melt in a ladle (adding alloying elements, degassing, etc.) before passing it through a refractory shroud into the tundish. This melt reservoir is connected to a mold casting nozzle—usually composed of zirconium dioxide (ZrO2)—via a feed tube and a break ring installed within the copper mold. As the mold is water cooled, molten steel that extrudes through the break ring rapidly cools into a continuous profile. This poses several significant challenges.
Break rings are subject to abrasion and chemical attack from molten steel, they are also at risk of deformation or outright failure due to thermal shock—given the extreme temperature gradient between their interior and exterior faces. Additionally, wetting by liquid metal may cause detrimental interfacial reactions which may impact yield and/or steel quality.
Boron and silicon nitrides are subsequently the natural solutions for HCC break rings, given their inherent non wettability, excellent thermal shock and corrosion resistance, and high strength. However, BN break rings typically offer enhanced wear-resistance at the expense of thermal performance while silicon nitrides have been unable to satisfy ferrous metal corrosion resistance requirements for HCC applications. Syalon 110 was engineered with these specific requirements in mind.
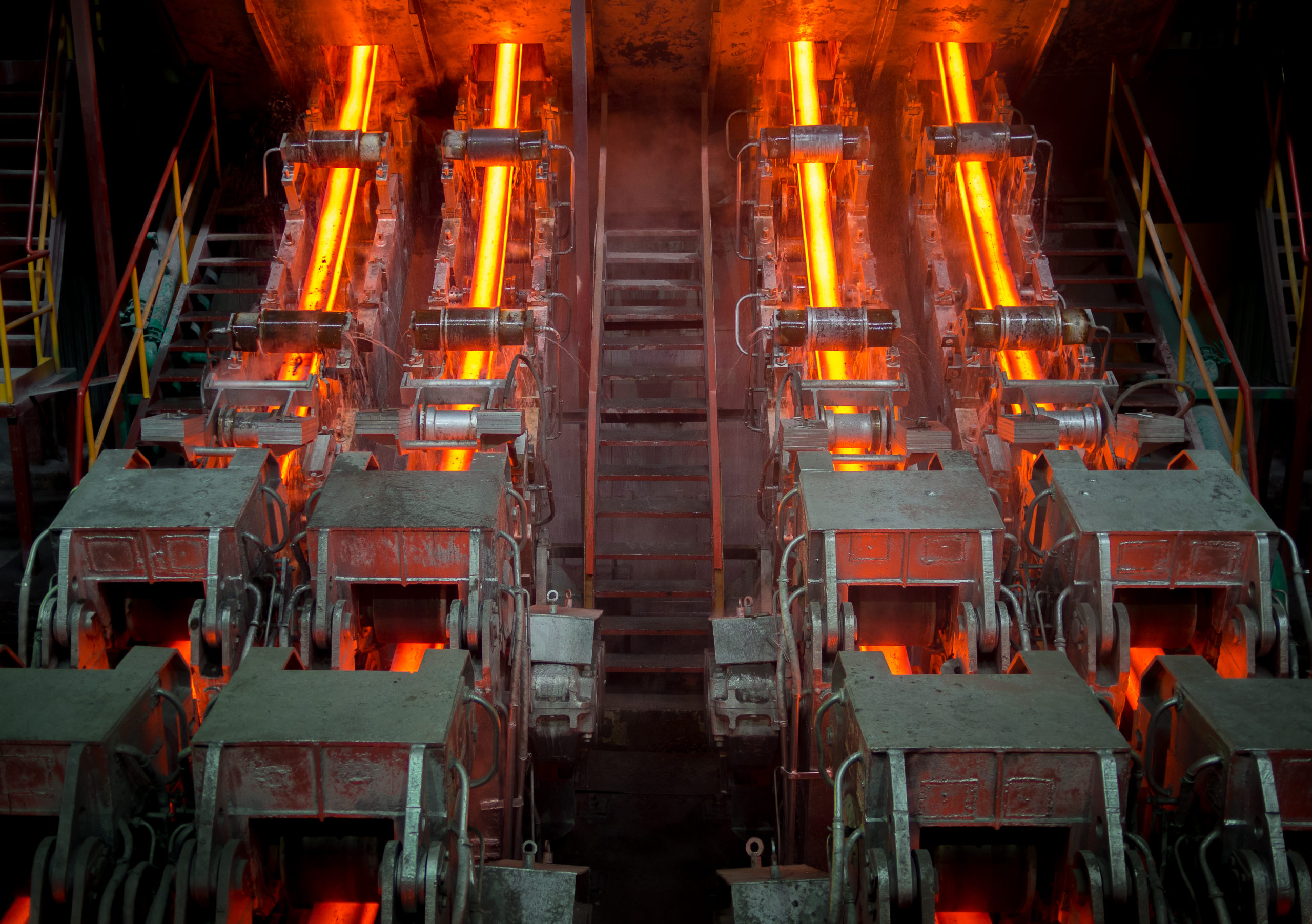
Image Credit: Shutterstock
Our Syalon Break Rings
Syalon 110 is a unique beta-phase silicon nitride-BN composite, unifying the beneficial properties of both preferred break ring materials. One of the most specialised technical ceramics in the Syalon line, Syalon 110 boasts superior corrosion resistance to molten steel—compared with standard silicon nitride—and greater thermal shock properties than BN ceramics.
Key properties of our Syalon 110 break rings include:
- Thermal shock resistance of ΔT = 800°C for cold water quenching
- Maximum use temperatures approaching 1450°C (2642°F)
- Thermal conductivity of 27.0 W/(mK)
Interested in hearing about specific use cases? Contact a member of the International Syalons team today to discuss design parameters and for more detail on our heavy-duty break rings for long-service in HCC applications.