Technical ceramics have become a mainstay among advanced engineering materials, replacing heavy duty metallic alloys and even refractories in many challenging applications and industries. This stems from their good all-round thermomechanical properties, but can also be attributed to incremental improvements in designing with ceramics and ceramic manufacturing. So, what impact does this shift towards specialist, high-performance material solutions have on corporate and social responsibilities, and sustainability initiatives?
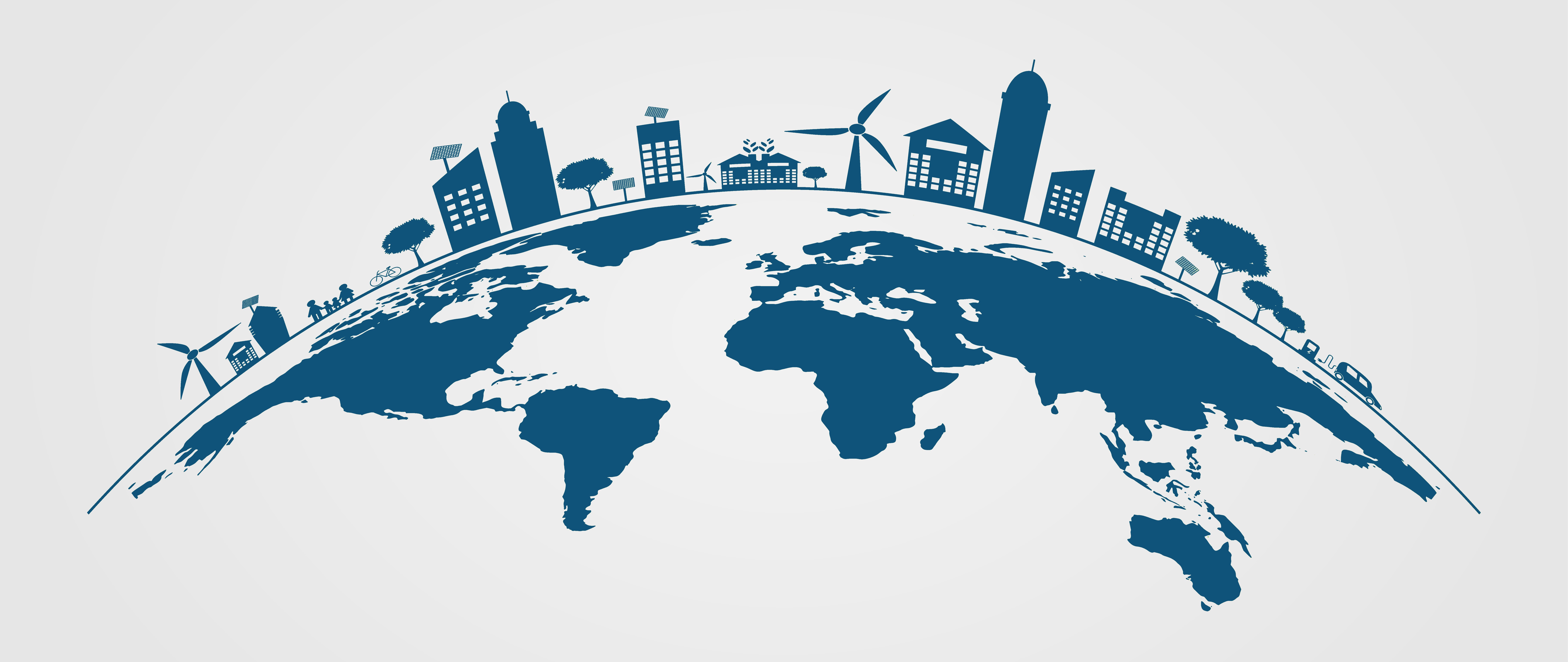
Image Credit: Shutterstock
Cost Vs. Performance Vs. Sustainability
Project and supply chain managers always look to select the right material for the contract, not just the job. That includes weighing up the initial versus the long-term cost of materials, plus the availability of different solutions. This must all be balanced by client-defined performance expectations. In the past, cost versus performance was the main dichotomy in engineering applications, but project managers are increasingly tasked with meeting sustainability requirements.
We discussed what makes a sustainable material in our recent article looking into the pollutive effects of technical ceramics. Briefly: a sustainable solution is usually defined as one with a negligible ecological footprint. Advanced engineering materials are rarely truly sustainable given the power-hungry processes that go into their production. However, technical ceramics are considered more eco-friendly in applications where counterparts made from conventional materials are subject to wearing or failure.
Read More: How Eco-Friendly are Ceramic Materials? An Insight into Pollution
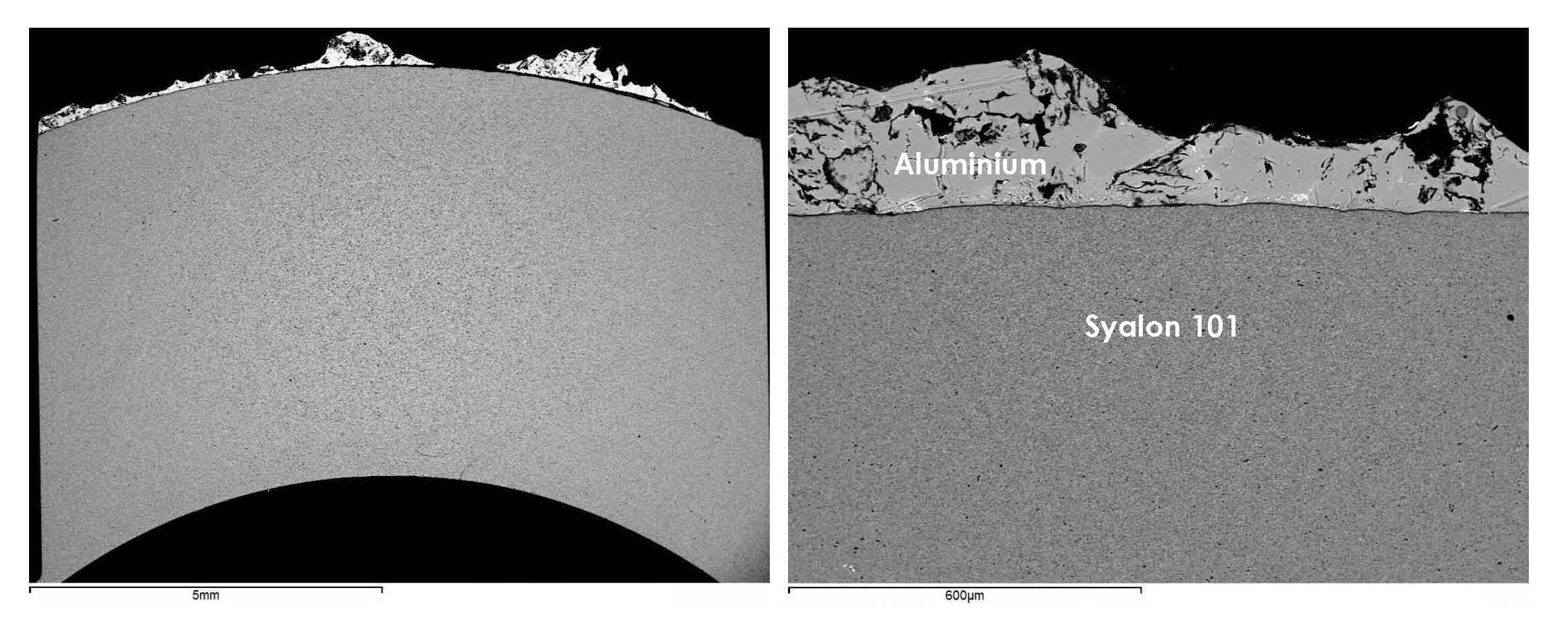
Image Credit: International Syalons (Newcastle) Ltd.
Production & Performance: Key Drivers of Sustainability
Without cost-effective production methods, it can be difficult, if not impossible for engineers to justify the production expense of relatively new materials versus industry standard solutions (i.e. HSLA steel) regardless of performance comparisons. Yet gradual enhancements in binding, forming, and sintering processes have made the likes of alumina (Al2O3), silicon nitride (Si3N4), and zirconia (ZrO) more attainable from a budgetary perspective.
The long-term performance of specialist technical ceramic solutions has encouraged similar attraction from a wide cross-section of industrial areas. Technical ceramic components can withstand higher temperatures and loading forces with a dramatic increase in the amount of successful run cycles compared with conventional materials. This translates to significantly improved efficiency, which is a key indicator of sustainability.
Sustainable High Duty Solutions
When discussing the feasibility of sustainable materials in harsh environments, lifetime is a critical factor. The frequency of maintenance and part replacement directly leads to wastage, mandating both disposal and further production. Conventional materials are increasingly recyclable, meaning there is a reduced reliance on landfills which pollute sediments and water sources, yet the need to routinely generate replacement parts inevitably generates emissions which contribute to the greenhouse effect. Anything that can interrupt this cycle of consumable goods is a welcome change.
Interested in using technical ceramics for your next project? There are various design parameters that you should bear in mind, including the different properties of oxide and non-oxide ceramics, plus the distinct differences within ceramic grades that are determined by their composition, purity, and so on.
However, with generally favourable mechanical properties (hardness, strength, toughness, elastic modulus, etc.) combined with outstanding thermal characteristics (CTE, thermal conductivity, thermal shock resistance, etc.), technical ceramics provide specialist heavy duty solutions for specific demanding application areas. Contact a member of the International Syalons team today to learn about meeting your budget, performance, and sustainability requirements with technical ceramics.