Advanced ceramic manufacturing is a complex multi-step process centring on the consolidation and sintering of raw mineralogical feedstocks. Regardless of the type of ceramic (oxide or non-oxide), or the complexity, shape, size, and structure of the finished part, it is this densification stage of production that unlocks the outstanding thermomechanical properties of technical ceramic materials. It is also, by far, the most energy-intensive link in the advanced ceramics manufacturing chain.
We have discussed the ecological footprint of technical ceramics in recent articles, from their negligible pollutive behaviour to their extended life cycles—a key driver of sustainability. However, ceramic manufacturing is more difficult to reconcile from an environmental perspective given the power-hungry nature of sintering processes.
Here we will look at some of the key ceramic manufacturing processes to see whether they could be considered environmentally friendly.
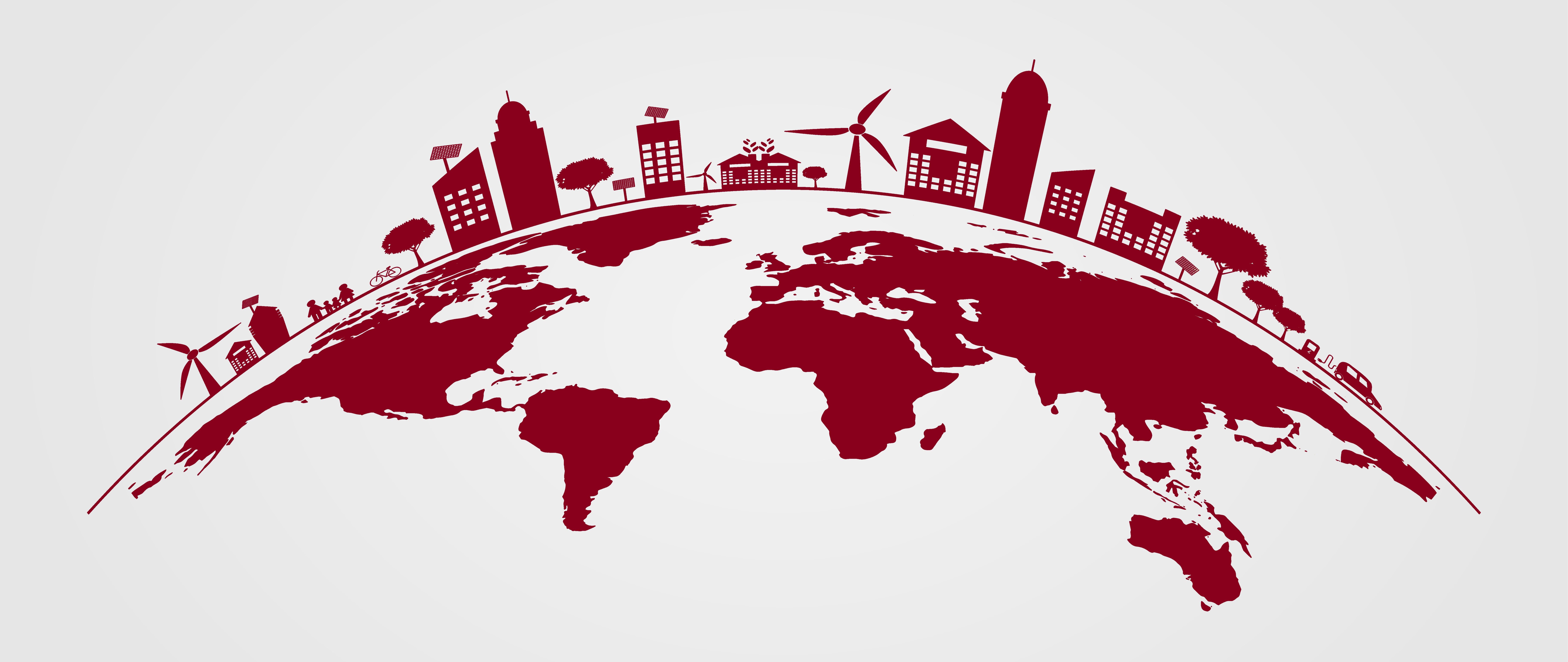
Ceramics Forming Processes
The green forming stage of ceramics manufacturing occurs when raw powders are consolidated into a ‘green body’ usually via applied pressure. Common techniques include uniaxial pressing, where feedstocks are compacted into a rigid shape using a tool steel die; isostatic pressing, where spray-dried powder in a polyurethane/rubber bag is subjected to isostatic pressure; extrusion, where a plasticised paste like mixture is forced through an orifice; and slip casting, using an aqueous slip and a porous mold.
The sheer diversity of forming processes makes it difficult to assess an overall ecological footprint. Applied pressures in uniaxial or isostatic pressing for instance can range from 20—700 MPa, with high compaction pressures typically translating to higher green compact strength. Mechanical green forming methods such as these normally rely on electrically derived pneumatic or hydraulic pressures, which are moderately energy intensive processes, but are ever improving in efficiency. An example where pressure is chosen to be applied is in high-volume commercial potteries where, to reduce casting time and increase throughput, slip is forced into porous molds, accelerating the naturally occurring capillary action relied upon for slip casting and reducing casting times by a factor of 10. In this case, conventional slip casting would be commercially unviable. Thus, greater density and faster compaction usually comes with a trade-off in terms of energy consumption.
However, most ceramic forming processes—with the notable exception of hot isostatic pressing (HIP)—are not thermal in nature, so the forming stage is comparatively ecological.
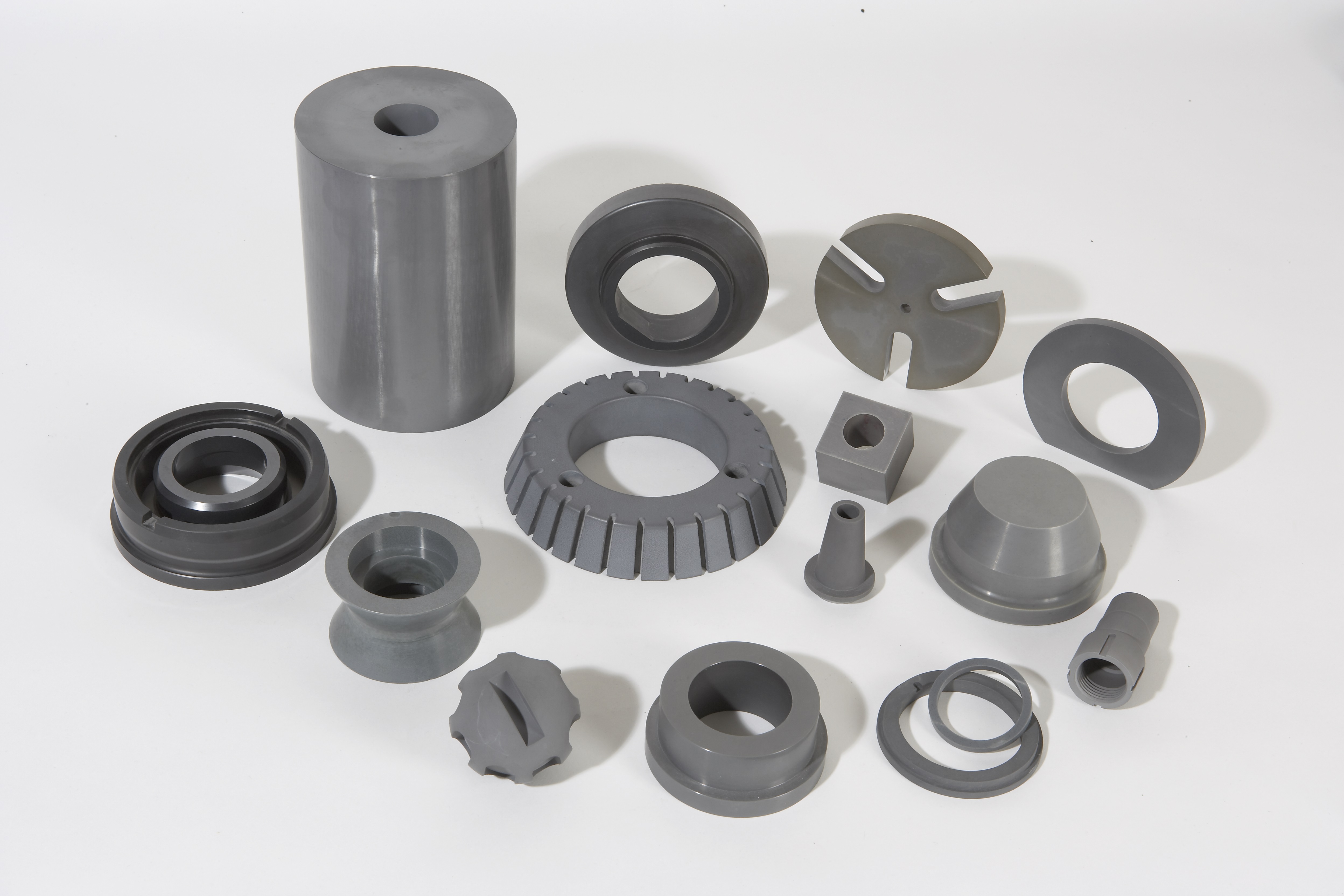
Ceramics Sintering Processes
After consolidation, the green body is fired at extremely high temperatures via either solid-state or liquid-phase sintering. While traditional potteries and ceramic construction material manufactures rely heavily on gas powered furnaces, technical ceramic sintering very rarely occurs in open flames due to the ceramic’s sensitivity to atmospheric conditions and need for precise temperature control. Instead, the extremely high temperatures required to achieve densification are generated using electrical resistance of metallic or composite heating elements (depending on the required atmosphere). This is where the question of sustainability in ceramic manufacturing truly becomes an open question as such furnaces themselves are not burning fossil fuels but are instead directly converting electricity into heat; therefore how ecological the manufacturing process is depends almost entirely on the furnace efficiency and the electricity source.
Using renewable energy sources like hydroelectricity, wind, and solar means the high electricity consumption of sintering processes has a low environmental impact compared to alternative manufacturing processes. Therefore, there is an opportunity for technical ceramics manufacturing to embrace the ongoing revolution in green technologies, and by doing so dramatically reduce the environmental costs associated with continuous material production.
Read More: Are Technical Ceramics a Sustainable Solution? An Insight into Properties
If you are interested in how to deploy technical ceramics in your next engineering products, why not contact a member of the International Syalons team today?