Update: Originally posted in 2022, this blog was updated with new context on 27/03/2024.
Careful material selection is essential in sectors using heavy machinery or extreme processing temperatures. Advanced ceramic materials are instrumental in mitigating or diminishing wear in industrial environments. This blog will discuss a broad spectrum of wear mechanisms, highlighting how advanced ceramics outperform traditional ceramics in combating wear. Specific attention will be paid to the role of advanced ceramic materials in resisting abrasive wear, where hard particles remove material from the surface, and adhesive wear, characterized by strong adhesive forces between sliding surfaces. Additionally, we will address how these materials withstand corrosive wear, which involves chemical or electrochemical reactions at the surface.
Advanced Ceramics
Advanced ceramics are critical in offering wear resistance against various types of wear, including abrasive, adhesive, and corrosive wear, which frequently occur under high temperature and harsh operation conditions. These materials are selected for their superior material properties, which include high corrosion resistance and the ability to maintain a solid surface integrity even under cyclic loading or conditions that typically induce surface fatigue.
There are several advanced ceramics that are used for their strength, excellent wear resistance, corrosion resistance and thermal stability. The ceramics chosen will depend on the application,
Some materials that are frequently used for their abrasion resistance and high strength are:
- Aluminium Oxide
- Zirconia
- Silicon Nitride
- Silicon Carbide
To try and reduce the impact of wear and tear on machinery and materials, or prevent it all together, machinery parts and systems must be manufactured in a way that can withstand harsh conditions. This includes extreme temperatures, abrasion, chemical reactions and wear and tear.
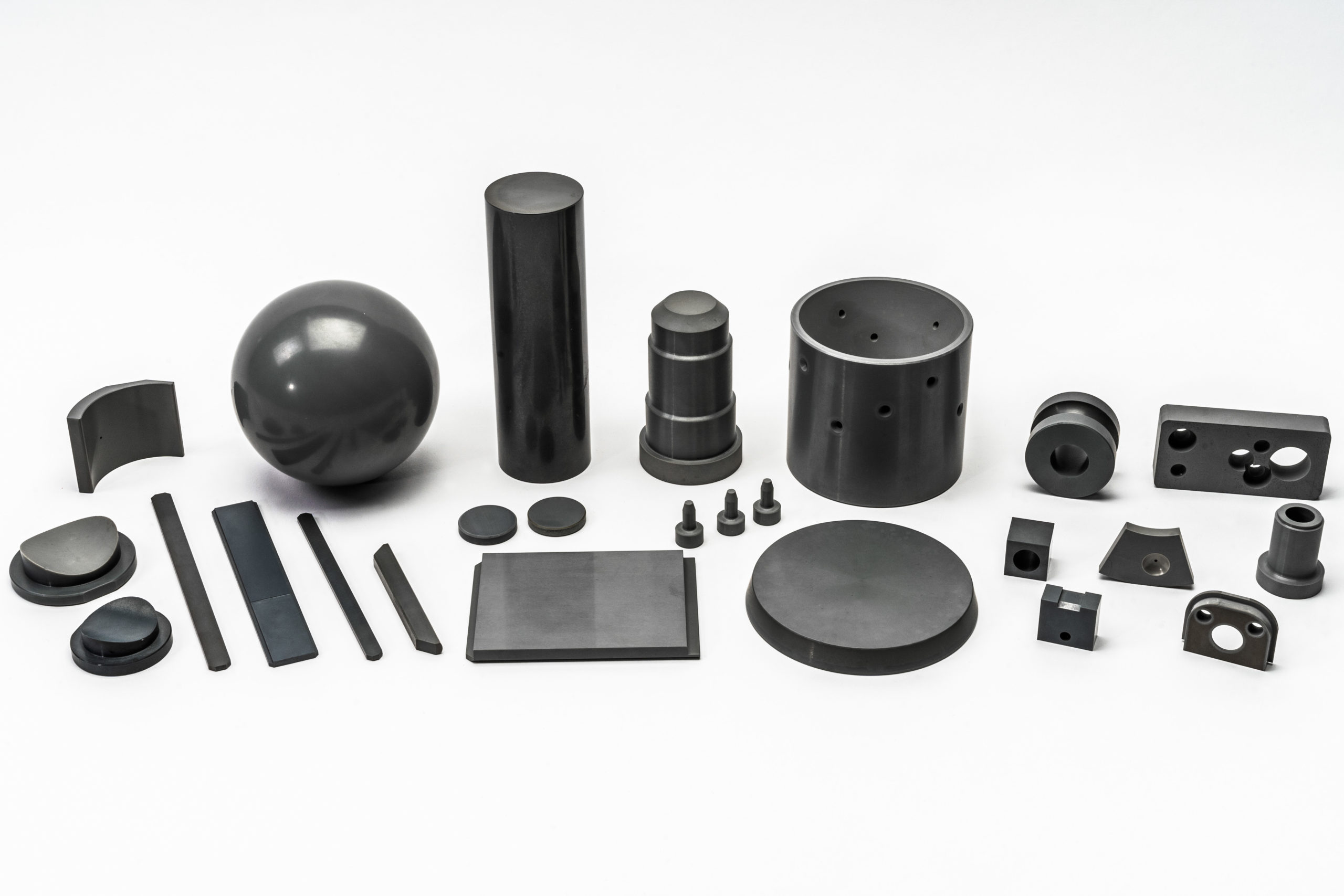
High temperature and wear resistant Syalon 101 components. Image Credit: International Syalons (Newcastle) Ltd.
Case Study 1: Mass Evaluation of Thermo-Blast Jet Nozzle Materials
There have been a number of case studies carried out concerning the wear and durability of blasting nozzles. The above-named case study was carried out by I.A. Gorlach for their PhD in Mechanical Engineering thesis for the North-West University in South Africa. Blasting nozzles are strong components that push air and abrasive media over the surface of a material. Previously, blasting nozzles were frequently manufactured using tungsten carbide (WC) due to their high strength and extreme hardness. However, the material that WC is combined with to uphold such strong properties can be worn down over time and therefore blast nozzles made of traditional materials will not withstand the pressures forever.
To replace WC, sialons are now a more appropriate choice for blast nozzles. Sialons are able to withstand long-term abrasion and high-temperature processes, as well as boasting outstanding resistance properties. These blast nozzles are produced with Syalon 050 and an alpha-beta ceramic material with extreme hardness. The material is then able to endure over 1000 hours under tough operating conditions and reduce the amount of wear and tear compared to WC nozzles.
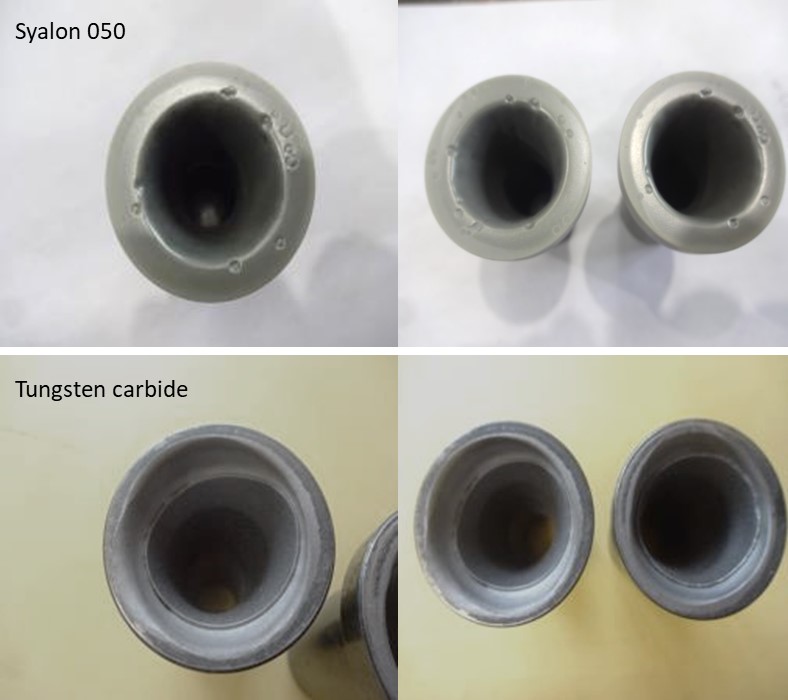
Sialon 050 vs Tungsten Carbide nozzles. Image Credit: International Syalons (Newcastle) Ltd.
Case Study 2: Wear Prediction of Ceramics
The case study Wear Prediction of Ceramics was carried out by Stephen Hsu and Ming Shen at the National Institute of Standards and Technology, Gaithersburg, USA. Their studies have highlighted the need for advanced ceramics in applications where high speeds, extreme temperatures and aggressive media are used. The ceramic materials investigated include silicon nitride, silicon carbide, aluminium oxide and zirconium oxide due to their high levels of toughness, heat resistance as well as their abrasion and corrosion resistant properties.
Their case study results show that the four ceramic materials investigated are suitable for use in advanced structural applications, more specifically where strong wear resistance is required.
International Syalons
International Syalons supplies a range of advanced ceramic materials for several process industry applications that require thermal stability and high levels of wear resistance. Some of the products we provide include high quality Syalon 101 nozzles, milling media, face plates and weld rolls, which are all common industrial wear applications.
Read More: Understanding Wear and Recognising Different Wear Modes
We have a variety of advanced technical ceramic solutions and can offer these to your requirements. If you’d like a consultation with our sales team or are looking for a quote, please get in touch with us today.