Heat is an essential aspect of numerous industrial processes: turbines and generators often operate most effectively at higher temperatures; many key chemical process industry (CPI) reactions occur at extreme temperatures; extruded, pressed, and welded metal parts are routinely formed when heated to the point of plasticity. These are just a few examples where temperatures exceeding many hundreds of degrees are routinely generated and sustained. Naturally, all these applications require high-temperature resistant materials that can withstand the enormous thermal shock and long-term stresses associated with these extreme environments. So, how exactly do they work?
What are High-Temperature Resistant Materials?
Many materials can be used in high-temperature applications, but the most suitable will depend on the industry, application, and processes the material must withstand. Technical ceramics are widely used in the harshest environments because of their outstanding high-temperature resistant properties. The two key aspects we will focus on in this section are heat resistance and thermal wear, as both properties are crucial for withstanding challenging, high-temperature applications.
The heat resistance properties in technical ceramics are due to the raw materials used in manufacturing them and the atomic bonding formed during the densification process. The two components contributing to heat resistance are melting point and thermal shock resistance.
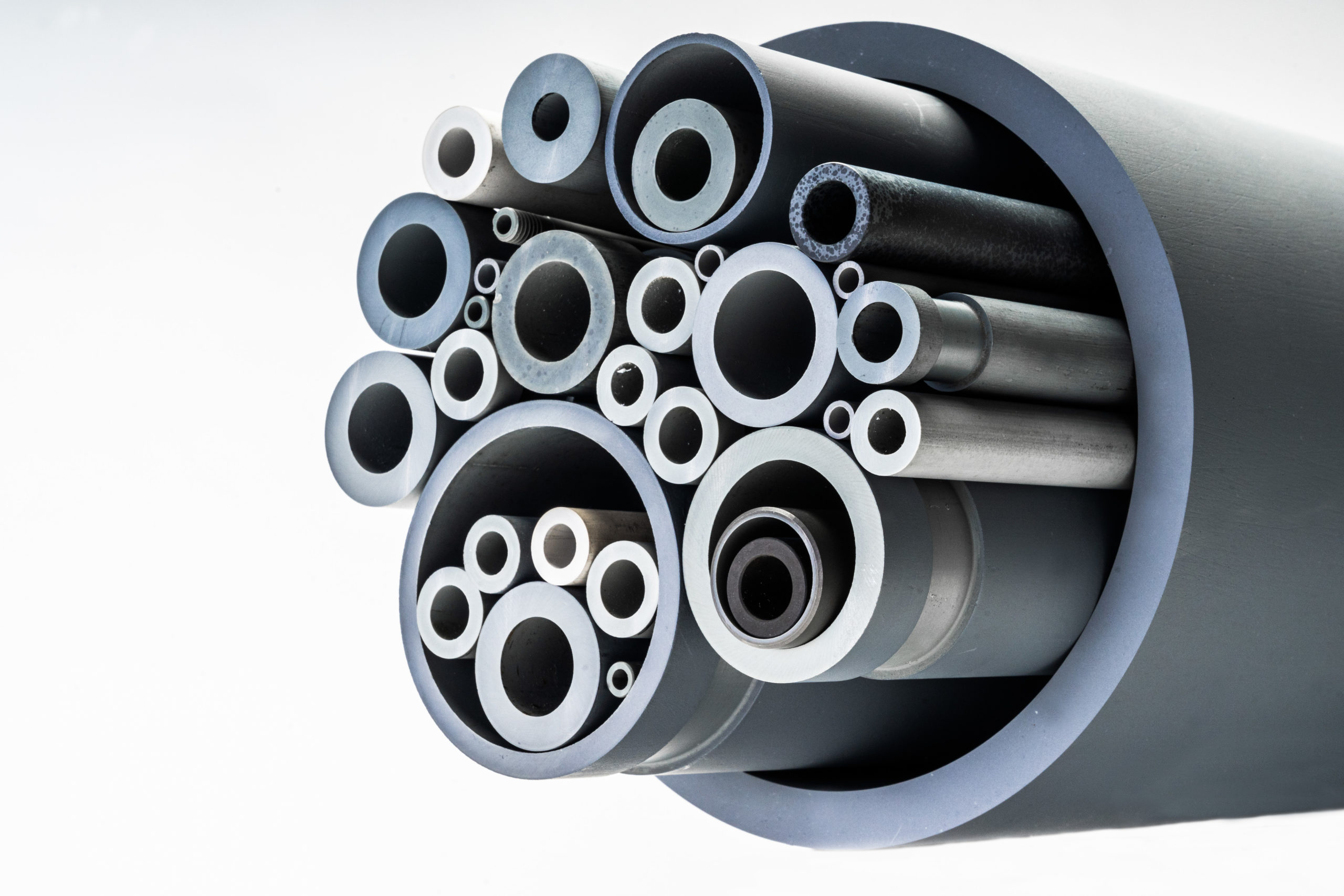
Silicon nitride thermocouple protection tubes. Image Credit: International Syalons (Newcastle) Ltd.
Melting Point
Advanced ceramics have extremely high melting points, and there is even a separate class of materials categorised as ultra-high temperature ceramics (UHTCs) with melting temperatures over 3000oC. Non-UHTCs have a range of melting points, for example, 1200oC in porcelain and 2400oC in vitreous carbon. The high melting points of ceramics contribute to their levels of heat resistance.
Thermal Shock Resistance
The thermal shock resistance of a ceramic is an essential factor in any high-temperature applications and impacts the heat resistance properties. It refers to how well a material resists internal stresses caused by rapid changes in temperature, including both heat and cold. During high-temperature applications and the cooling process, a material will be placed under pressure, which will strain and stress it. Without significant thermal shock resistance, this can lead to cracks and failure. When a ceramic material cracks under thermal pressure, this is known as thermal wear or thermal fatigue. However, these changes are often minimal due to their high thermal shock resistance.
What Makes Technical Ceramics so Thermally Resistant?
Ceramic materials have an outstanding selection of properties which include high hardness, low density, excellent mechanical strength, and, as we’ve already mentioned, high temperature and thermal resistance. These properties are exceptional due to the strong covalent and ionic bonds paired with the internal structure of the ceramic. The covalent and ionic bonds in ceramic materials contribute to their electrical, mechanical, optical, and thermal properties, which often surpass many other materials. It is important to note that the properties of ceramic materials are also based on their internal microstructure, which determines whether a ceramic is categorised as polycrystalline or monocrystalline.
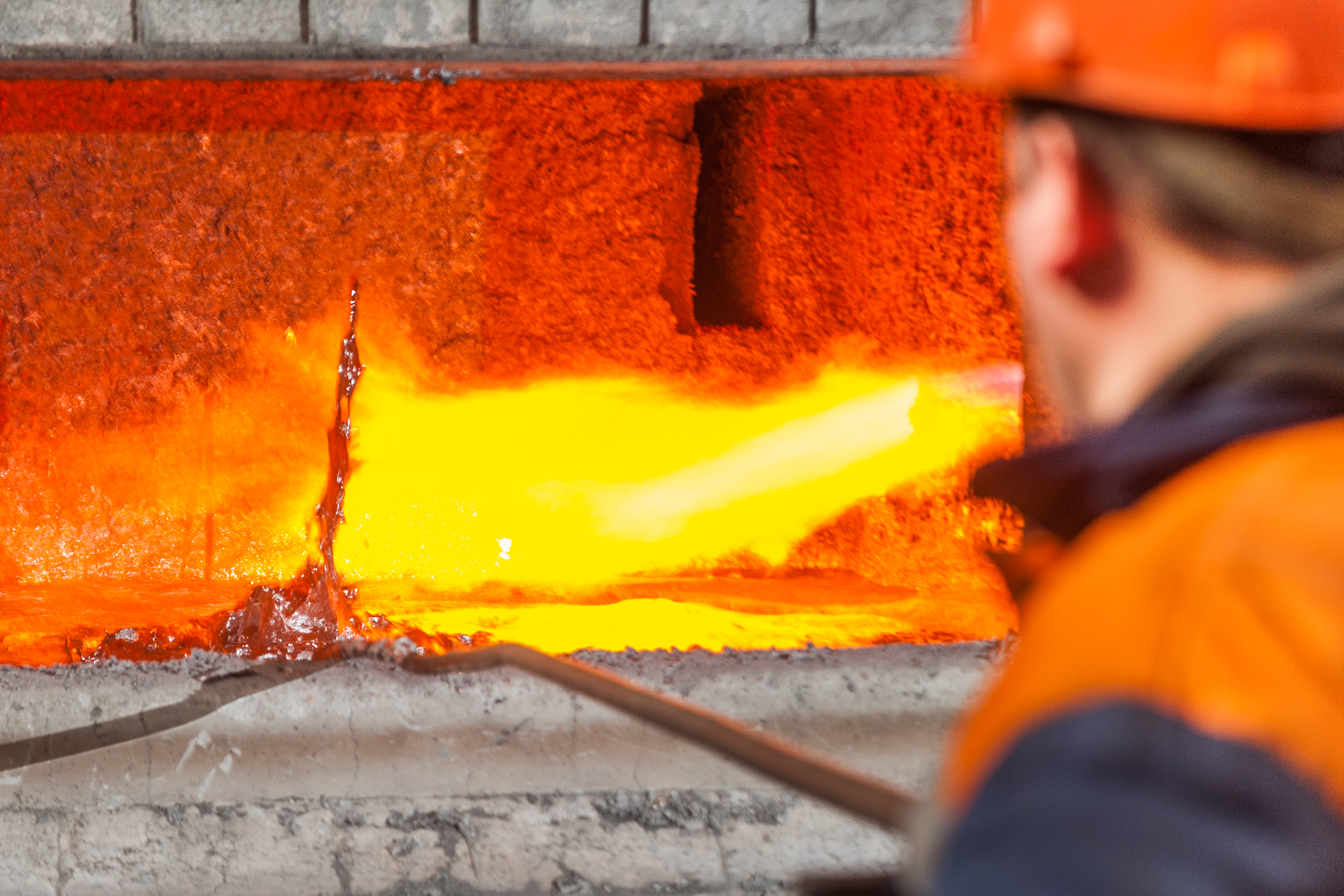
Aluminium Foundry – Image Credit: Shutterstock
International Syalons: High-temperature Resistant Ceramics
International Syalons are industry leaders in manufacturing high-quality, high-temperature-resistant ceramics for industrial applications. Our products are used in extremely harsh environments, in industries such as oil and gas, metal forming, and chemical processing.
Do you need advanced ceramic products for your applications? Contact a member of the International Syalons team today, and we’ll be happy to help.