Innovation is often the answer to process inefficiency. Manufacturers routinely look to develop new systems that address specific pain points in industrial manufacturing. Welding rollers, for example, unlocked greater levels of throughput and product quality in longitudinal seam welding and high-frequency electric resistance welding (HF-ERW). These relatively simple components allowed for accurate positioning and conveying of cylindrical workpieces throughout key processes. This enabled manufacturers to break new ground in operational efficiency. But conventional pipe rollers are not without issue.
The choice of welding rollers, especially when considering the material-specific requirements and their capabilities in different welding scenarios, directly influences the production process’s efficiency and output quality. Transitioning from traditional steel to advanced ceramic rollers, known for their superior durability and performance, is a critical consideration for systems integrators aiming to optimize manufacturing workflows and address key pain points such as equipment longevity and maintenance frequency.
What’s the Problem with Steel Weld Rollers?
Steel weld rollers have a shorter service life compared to their ceramic counterparts, such as those made from silicon nitride. This shorter lifespan results in more frequent replacements due to significant wear, directly impacting the consistency and quality of the welding process. Consequently, this need for frequent maintenance and replacement disrupts production schedules, extending lead times and reducing overall efficiency. In contrast, silicon nitride ceramic rollers offer up to 40 times longer service life, significantly reducing downtime and maintenance costs.
Additionally, the regular maintenance required for steel rollers adds operational costs and interrupts the manufacturing flow. This interruption is a key factor in extending lead times, as it contributes to delays in processing, production, and delivery. Implementing ceramic welding rollers can mitigate these issues by reducing maintenance frequency, thereby enhancing operational efficiency and productivity.
Regarding product quality, steel rollers may not perform optimally with non-ferrous materials like stainless steel, brass, and aluminium tubes, potentially leading to weld failures and subpar surface finishes. This deficiency can result in product rework or quality issues, prolonging lead times. Ceramic rollers improve product quality and reduce the likelihood of such setbacks.
The high temperatures involved in welding with steel rollers necessitate significant cooling times, yet another factor that can extend lead times. Ceramic rollers, capable of operating at higher temperatures, reduce these cooling requirements, streamlining the welding process and saving energy.
Furthermore, steel rollers are less energy-efficient compared to ceramic rollers. Practical tests have shown that using ceramic weld rolls can reduce high-frequency weld power by up to 30%, contributing to energy savings and shortened lead times through more efficient operations.
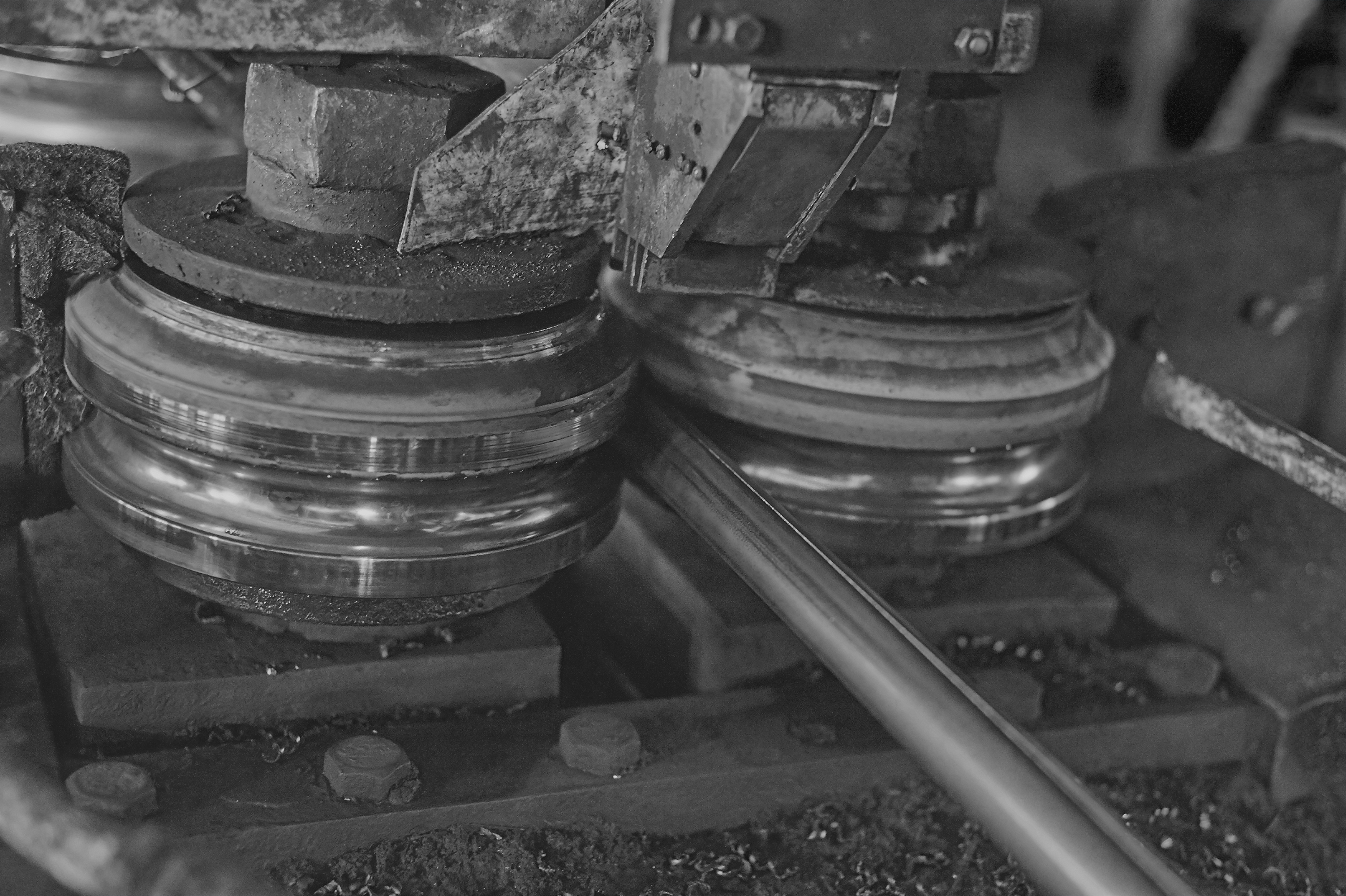
Tube forming process – Image Credit: Shutterstock
Realising Greater Lead Times with Ceramic Welding Rollers
With their limitations in service life, maintenance requirements, cooling needs, and energy efficiency, steel rollers can inadvertently extend lead times. Conversely, ceramic welding rollers, especially those made from silicon nitride, offer numerous benefits that can help overcome these challenges, ultimately leading to enhanced operational performance and customer satisfaction in the competitive industrial welding sector.
Operational Efficiency
The inherent properties of ceramic materials, such as their non-micro-welding nature and stability at high temperatures, yield significant operational benefits. These rollers exhibit minimal thermal expansion, maintaining their integrity even in high-temperature environments. This stability ensures continuous, uninterrupted operation, thereby streamlining the welding process.
Impact on Maintenance and Productivity
A critical aspect where ceramic welding rollers trump steel rollers is in the frequency of maintenance and replacement. Extended durability diminishes the need for frequent roller replacements, leading to fewer operational interruptions. Consequently, this enhances overall productivity and reduces lead times in the production process.
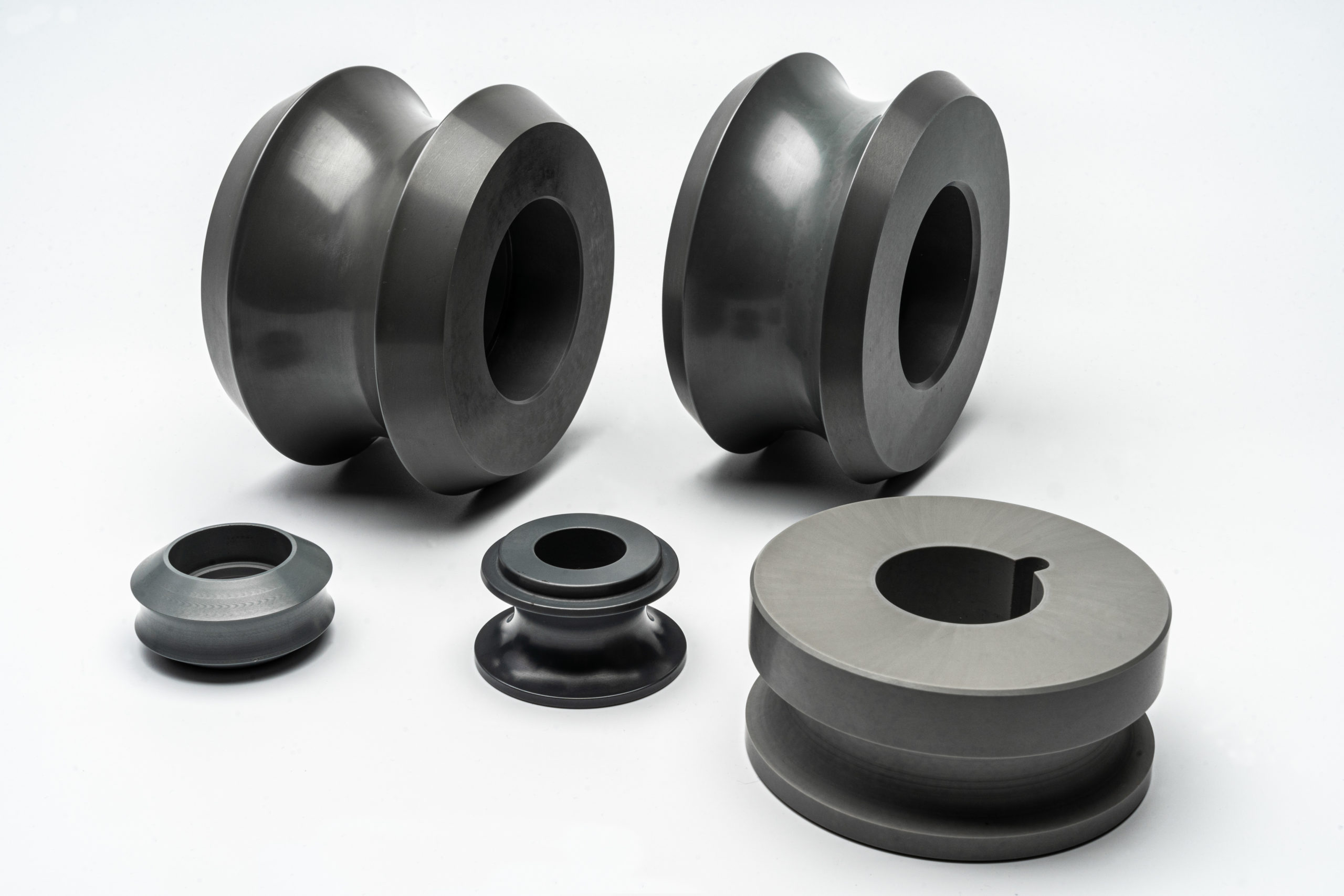
Silicon nitride based ceramic weld rollers for tube forming. Image Credit: International Syalons (Newcastle) Ltd.
Looking for Ceramic Welding Rollers?
International Syalons’ ceramic weld rolls stand out for their exceptional durability, offering up to 12 times more life than tool steel rolls. They solve common material pick-up problems, especially in high-frequency welded tubes, ensuring substantially improved surface finishes and reduced risks of rolling weld spatter or particles into tube surfaces. This particularly benefits non-ferrous materials like stainless steel, brass, and aluminium.
Moreover, these ceramic rolls significantly reduce high-frequency weld power by as much as 30%, enhancing energy efficiency and reducing unwanted ‘field’ heating of surrounding components. Their use is particularly advantageous for manufacturers of small diameter tubing, as they can reduce weld vee length, leading to a more aesthetically pleasing product with a reduced heat-affected zone.
Understanding that successfully integrating these advanced technical ceramics into your systems is vital, we invite you to collaborate closely for optimal results. For an initial consultation and to explore how these innovative ceramic weld rolls can enhance your operational performance, contact our technical sales team at +44(0)191 2951010 or via email at enquiries@syalons.com. You can also submit a request for a quote to tailor these solutions to your specific needs.