In the specialized field of surface treatment, shot blasting emerges as a key technique. At the heart of its success is the shot blast nozzle. This is a component that has a design that can significantly influence the final results of your treatment.
Let’s explore the importance of nozzle shape, size, and material in shot blasting. Alongside this, we will try to pinpoint which factor is the most critical in enhancing the process.
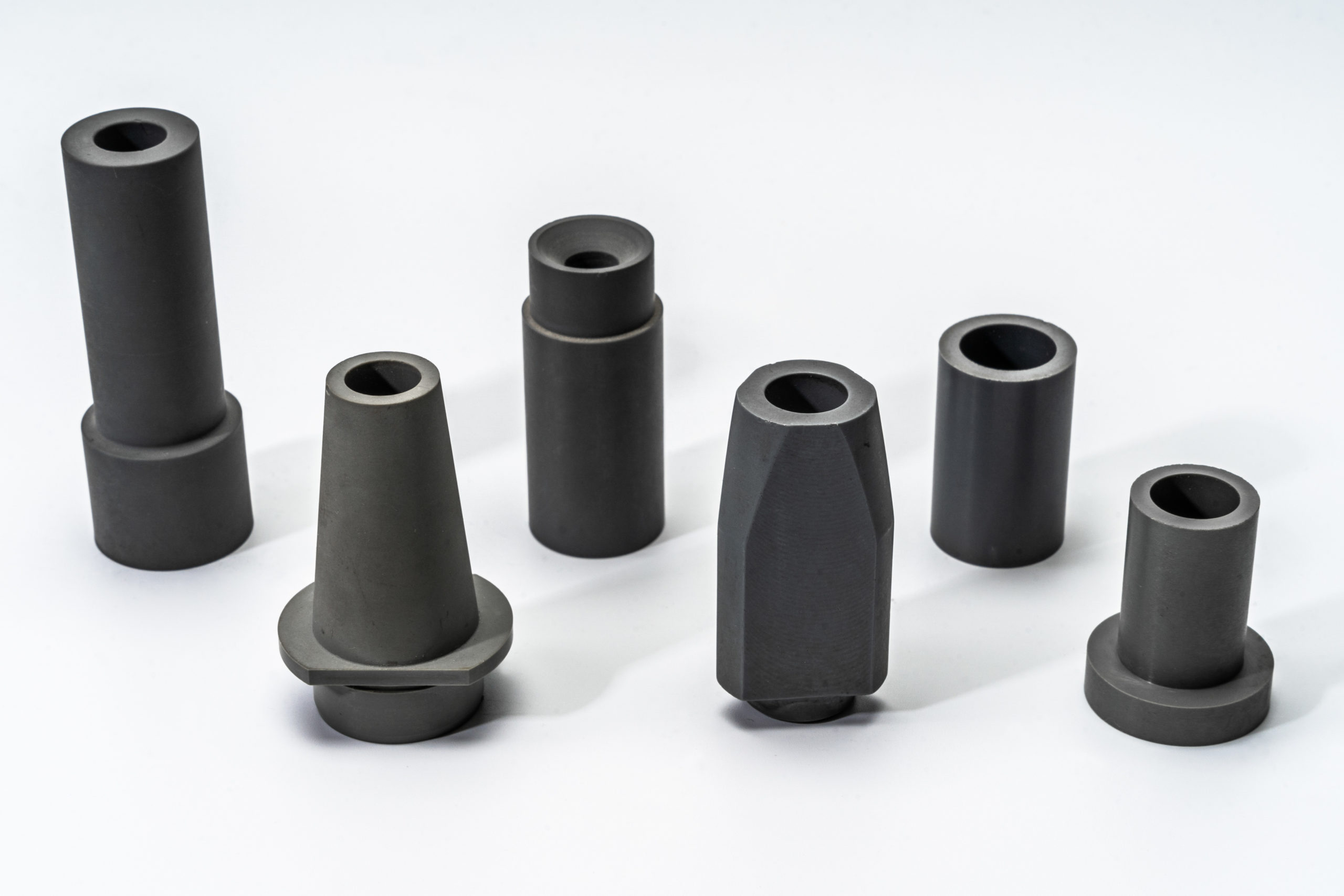
Sand Blast Nozzles
If you are considering your options for abrasive blast nozzles, you may want to use a sand blast nozzle that is combined with a blast hose. This type of nozzle works by aiming a stream of robust material, which is normally sand, at a surface. The combination of air and abrasive makes this nozzle useful in a variety of industries, including in the production of metal.
Advantages of this nozzle include its:
- Ability to clean surfaces
- Capability to remove rust
- Excellent polishing abilities.
The Influence of Nozzle Shape
The shape of the shot blast nozzle is crucial in determining the pattern and area of impact on a surface. Common shapes include straight bore, venturi, and wide-spray nozzles.
A straight bore nozzle produces a focused blast, which is perfect for precise work. Venturi nozzles, with their unique shape, increases the grit speed. They can also cover a larger area, making them great for bigger projects. Wide-spray nozzles cover the most area, but they may be less intense and even in their impact.
The right nozzle shape depends on your task. For detailed work, a straight bore nozzle is ideal, while a wide-spray nozzle could be better for larger surfaces. The material you are surface treating also matters as softer materials need a gentler grit to avoid damage.
Considering Shot Blast Nozzle Size
The size of the nozzle affects how efficient the blasting is and how much media you use. Larger nozzles mean more media and faster work, but they also use more resources and power. Smaller nozzles save on media and power but might slow down your project.
Choosing the right size is about finding a balance. In fast-paced environments, larger nozzles could be the way to go. In situations where saving media is important, smaller nozzles could be more beneficial.
Material Matters
Nozzle material is all about longevity and performance. Tungsten carbide nozzles are a good all-rounder, while boron carbide nozzles are tougher and better for heavy use. Ceramic nozzles are less durable but are a budget-friendly option for lighter tasks.
Your choice here depends on the abrasiveness of your media and how often you can afford to replace the nozzle. For intense, frequent blasting, boron carbide is a good investment. For less demanding jobs, tungsten carbide might do the trick.
However, silicon nitride shot blast nozzles are designed to outperform traditional materials like alumina and tungsten carbide. They offer advanced temperature resistances of up to 1450°C (2642°F) and can handle pressures of up to 100 psi. This makes them suitable for continuous, demanding operations.
The fracture toughness and strength of nozzle materials are crucial for their service life. Syalon 050 exceeds the capabilities of corrosion-resistant alumina products. It has a fracture toughness of 6.5 MPa and a Young’s modulus of 290 GPa. This allows Syalon 050 shot blast nozzles to withstand continuous operation for up to 1000 hours.
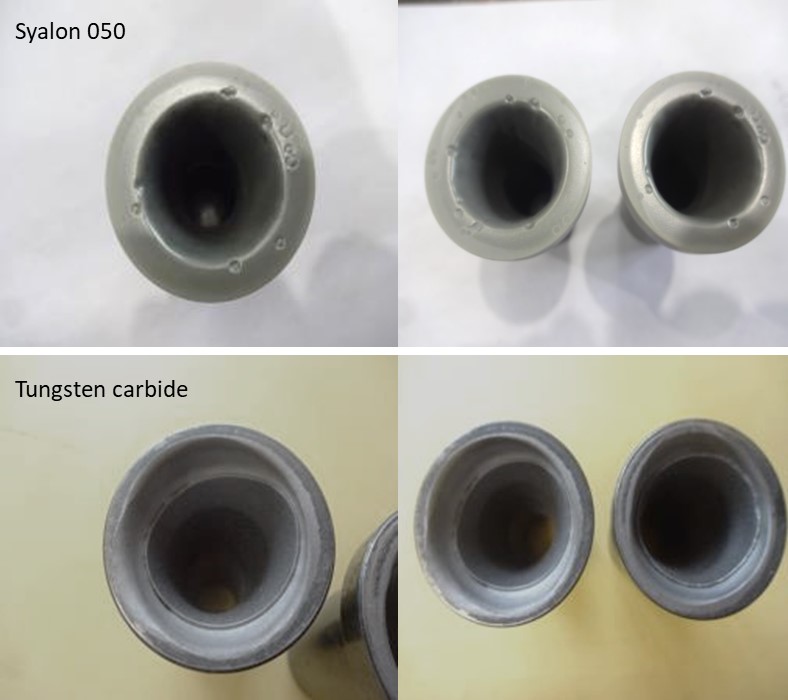
Considering The Balance Of Your Shot Blast Nozzle Setup
Choosing the most important aspect of a shot blast nozzle is not straightforward. To ensure the best outcome, you need to fully understand your blasting needs, the materials involved, and what you are trying to achieve.
For precise tasks, nozzle shape is key. When efficiency is your goal, size comes into play. Then when you encounter versus usage frequency, material is your main consideration.
The best shot blast nozzle setup is one that meets your specific blasting requirements, balancing performance, efficiency, and cost. Your decision needs to consider how shape, size, and material work together to give you the best blasting results.
Ready to revolutionize your shot blasting process with the superior performance of Syalon 050?
Ultimately, it is the outstanding properties of silicon nitride, particularly our Syalon 050, that offers unparalleled advantages in the realm of shot blast nozzles. If you are seeking a solution that combines strength, durability, and adaptability for your demanding industrial applications, consider the exceptional capabilities of our silicon nitride nozzles. At International Syalons, we are committed to providing innovative solutions tailored to your specific needs.
Contact us today to explore how our silicon nitride shot blast nozzles can enhance your operations. It can ensure efficiency and longevity in even the most challenging environments. Let’s work together to take your production to the next level through the cutting-edge technology of International Syalons.
References
- Burakowski T, Wierzchon T. Surface Engineering of Metals: Principles, Equipment, Technologies. United States: CRC Press; 1998.
- Champaigne J, Eckersey J. Shot peening – Theory and applications. Technology Transfer Series. 1991.
- Momber A. Blast Cleaning Technology. Springer. 2008. doi: 10.1007/978-3-540-73645-5_7.
- Myhra S, Riviere J. Handbook of Surface and Interface Analysis: Methods for Problem-Solving. Second ed. United Kingdom: Routledge; 2009.