Milling media is a critical component in the materials processing industry. It plays a pivotal role in the mechanical reduction of particle size in a vast array of raw materials and products, from pharmaceuticals to ceramics and metals.
While the immediate costs associated with milling media, such as purchase price and operational efficiency, are often meticulously accounted for, the hidden costs can be subtler, yet significant over time.
This article delves into these concealed expenses. Its main focus will be on factors that could influence long-term financial and operational outcomes.
Direct Costs: The Visible Tip of the Iceberg
Direct costs of milling media, including acquisition, replacement, and energy consumption, are readily quantifiable. High-quality media, though more expensive upfront, may offer better durability and performance, potentially reducing long-term replacement costs. Conversely, cheaper alternatives might lead to frequent replacements and downtime, escalating operational costs.
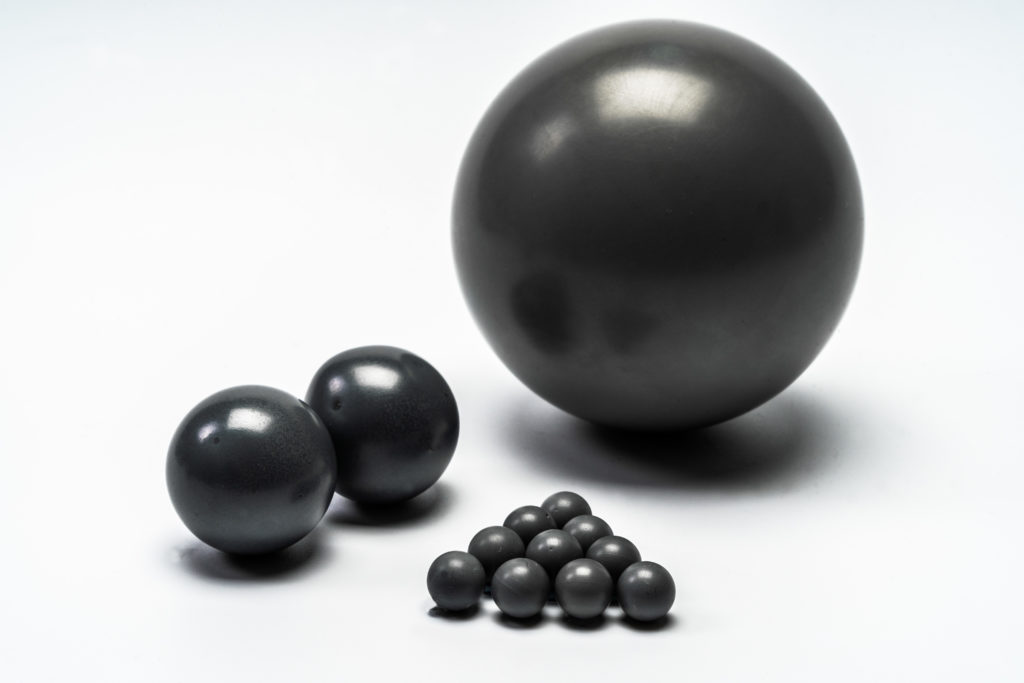
Hidden Cost 1: Media Wear and Contamination
One of the most overlooked aspects is the wear of the media itself from grinding and milling. As media degrade, they not only lose efficiency but can also contaminate the product with the debris of the material. This could be extremely detrimental in processes involving high-purity substances such as pharmaceuticals or fine ceramics. Contamination can compromise product quality and lead to costly product rejections or recalls.
Hidden Cost 2: Efficiency Degradation
The efficiency of milling media declines over time. This is a result of wear and shape alteration. If the media is not replaced, degradation could lead to longer milling times to achieve the final particle size. This not only increases energy consumption but also reduces throughput, impacting overall production efficiency.
Hidden Cost 3: Maintenance and Downtime
Frequent replacements and the maintenance of milling media necessitate operational downtime, which is often overlooked in cost analyses. The cumulative effect of these stoppages can be substantial, affecting production schedules and delivery commitments.
Hidden Cost 4: Environmental and Disposal Costs
The environmental impact and disposal costs associated with milling media are increasingly significant, especially with growing regulatory and societal pressures for sustainable manufacturing practices. The disposal of certain types of media, particularly those containing hazardous materials, can incur substantial costs and regulatory compliance challenges.
Strategies for Mitigating Hidden Costs
- Material Selection: Choosing milling media material for a specific milling application can significantly reduce wear and contamination. For instance, silicon nitride media, while more expensive, may offer superior durability and inertness compared to traditional silica or alumina media.
- Operational Parameters Optimization: Fine-tuning milling parameters, such as speed, media size, and loading, can enhance efficiency and reduce wear and energy consumption.
- Regular Monitoring and Maintenance: Implementing a routine schedule for inspecting and replacing milling media can prevent efficiency losses and unexpected downtimes. This will ensure a consistent milling process.
- Sustainability Practices: Exploring recycling options for spent media or selecting environmentally friendly materials can mitigate disposal costs and environmental impacts.
Make Sure You Know The Hidden Costs of Milling Media
The hidden costs associated with milling media, though often overlooked, can have a profound impact on the financial and operational efficiency of processing materials. A comprehensive understanding of these costs, coupled with strategic mitigation practices, is essential for optimizing long-term outcomes.
As the industry continues to evolve, with a growing emphasis on sustainability and efficiency, the scrutiny of these hidden costs will undoubtedly intensify, driving innovation and improvement in milling technologies and practices.
Many types of grinding tools exist to reduce particle size that you may want to consider. Some examples include:
- Grinding balls within ball mills and mill jars
- Tungsten carbide balls
- Silicon carbide grinding media
- Stainless steel media.
Of course, a wide range of grinding apparatus exists for particle size reduction. However, keep in mind that when choosing, you need to think about whether you actually need the tool or material. For instance, although tungsten carbide balls have the largest specific gravity, they are quite expensive. You may want a material that is more affordable to use in your processes.
Ultimately, choosing the wrong raw material or tool may end up costing more than you first thought. So keep it in mind during the selection process.
International Syalons Has Milling Media Available For Your Consideration
For industry professionals seeking to mitigate the hidden costs associated with milling media and optimize their milling processes, International Syalons offers a range of advanced ceramic milling media solutions.
Our products are designed to enhance durability, reduce contamination risks, and improve overall milling efficiency, aligning with the highest standards of quality and sustainability.
Explore our innovative milling media options and discover how International Syalons can contribute to the efficiency and sustainability of your operations. Visit International Syalon’s Milling Media page to learn more about our advanced ceramic solutions and how they can be tailored to your milling needs.
References
- Juhász A.Z, Opoczky L. Mechanical Activation of Minerals by Grinding: Pulverizing and Morphology of Particles. UK: Ellis Horwood;1990.
- Suryanarayana C. Mechanical alloying and milling. Progress in Materials Science. 2001;46(1-2): 1-184. doi: 10.1016/S0079-6425(99)00010-9.
- Tkáčová K. Mechanical Activation of Minerals. Netherlands: Elsevier; 1989.