Prototyping is inherently concerned with meticulous material selection. It concerns the rigorous, multi-step process of generating the right tool for a job. This can be complex even for relatively forgiving conditions. But there is very little margin for error in wear applications. Poor material selection can have severe deleterious effects on operations with abrasive environments. It’s essential to choose materials that can withstand the dynamic stresses of the intended application. However, there is no one-size-fits-all solution in the world of prototyping.
Ceramic solutions are increasingly the go-to material for extreme wear applications. Alumina, silicon carbide, and zirconia are among the most common ceramics deployed for severe abrasive conditions. Yet it’s important to note that the characteristic hardness and toughness of these materials will vary on a case-by-case basis. Relatively simple, sintered shapes will perform differently from intricately machined parts of the same material. Therein lies the importance of the prototyping process.
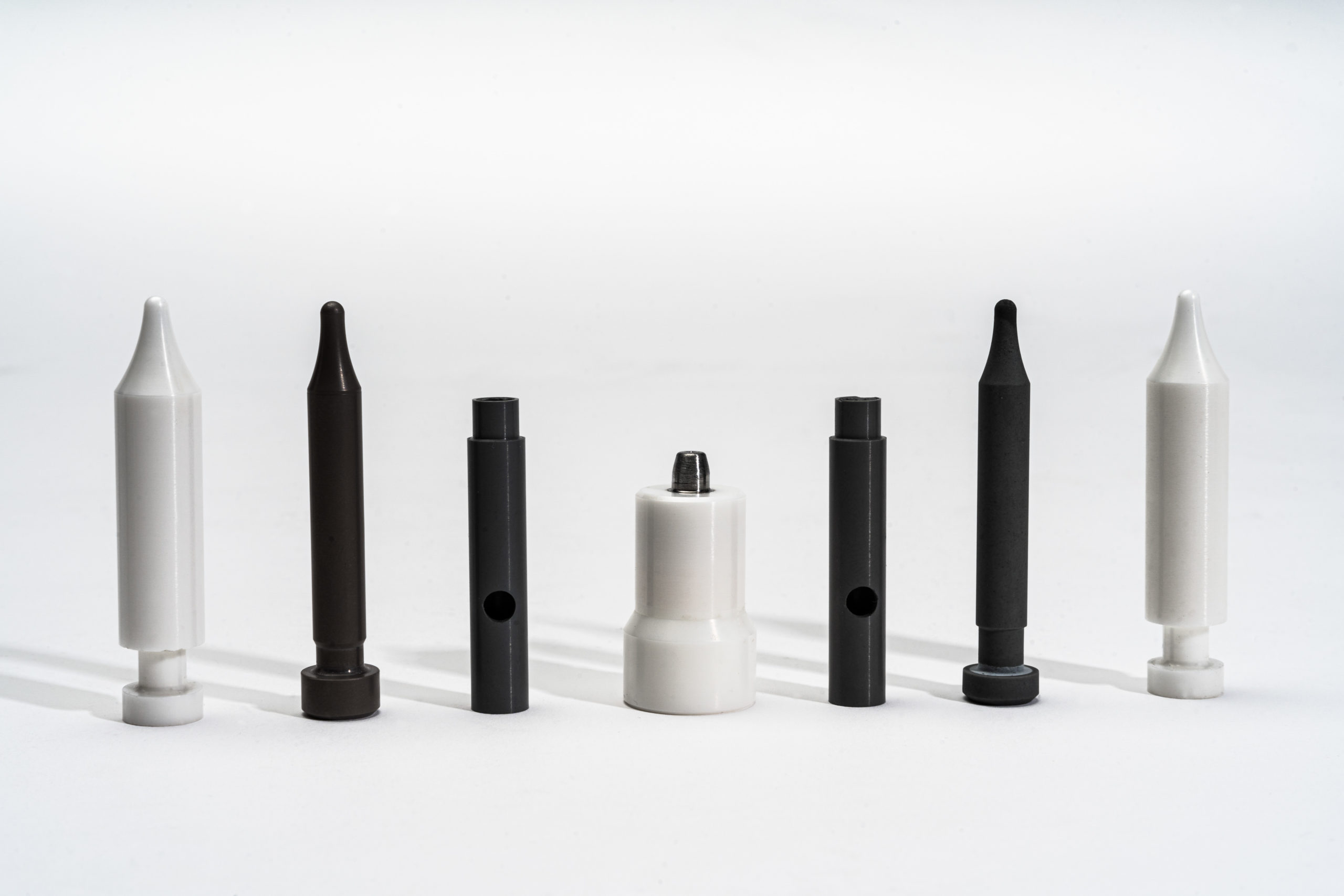
The Purpose of Prototyping and Testing Ceramic Solutions
Prototyping a ceramic solution is crucial for determining if it possesses the necessary characteristics to perform effectively in its intended environment. For instance, while zirconia is renowned for its exceptional hardness, it must still undergo testing to evaluate its structural integrity under temperature fluctuations, which it may encounter during use. Beyond assessing material properties, prototyping also verifies the efficacy and reliability of the manufacturing processes for producing the ceramic components.
The Prototyping Process
Choosing A Material
Materials used in abrasive environments must possess sufficient strength to resist wear. These conditions typically involve grinding or friction, leading to material deterioration. Selecting the optimal material depends on its inherent qualities. Carefully evaluate the attributes of your ceramic options. Below are the key characteristics of silicon carbide, alumina, and zirconia ceramic solutions:
- Silicon carbide: A major benefit of using silicon carbide is its hardness. The hardness of silicon carbide is defined as between 9.2-9.5 on the Mohs scale. Silicon carbide can also remain robust against wear and endure heat that does not rise above 1600°C.
- Alumina: This ceramic is extremely strong and can maintain this attribute until the temperature goes over 900°C. Furthermore, it can withstand corrosion and its Mohs hardness has been categorized as 9.
- Zirconia: Not only is zirconia extremely tough but it is also very strong and can resist wear.
Designing the Prototype
Once a ceramic solution has been selected, it is time to form the design of the prototype. To do this, computer-aided design software is needed. This software helps establish geometries which lower the concentrations of stress. Designs can be finalized through finite element analysis (FEA). Utilizing FEA can create a simulation that shows how the ceramic solution prototype could be affected by stress and wear. With its help, the design can be altered to improve the prototype.
Creating the Prototype
The next step of the prototyping process is to create the prototype itself. A number of techniques can be used to generate the prototype, including slip casting, injection molding, and pressing. However, for prototypes that contain geometries that are more complicated, it is wiser to use 3D printing instead. That way the fit of the prototype can be assured. If necessary, a coating can be applied to the ceramic solution to better its ability to withstand wear. To ensure the prototype’s surface finish is at a good standard, and its dimensions are exact, abrasive finishing can be applied through the use of polishing or grinding.
Testing The Prototype
With the prototype successfully created, it must be tested to see how it reacts to abrasive conditions. The results of these tests will help with making improvements to the prototype. Examples of these tests include:
- Abrasion tests: These assess how well it can withstand any wear and scratches. With the taber abrasion test, the ceramic is placed on a platform that rotates and connects to an abrasive wheel. There is also the dry sand/rubber wheel test. In this test, sand is introduced to the ceramic, which is shaped as a blocked coupon, while it is in contact with a rubber wheel.
- Micro-abrasion tests: Another set of tests for wear, they move back and forth and try recreating the abrasion found within an abrasive environment.
- Impact tests: They examine how the ceramic solution could be affected by particle collision at different angles and velocities.
Which Ceramic Solution Will You Use In Abrasive Conditions?
Your choice of ceramic solution must be based on the type of environment it will be used in. If it is going to be used in abrasive conditions, the material must be able to resist wear effectively. We, International Syalons, have ceramic solutions available that possess this property. Take a look at the materials we have to offer, such as zirconia, alumina, and silicon carbide. Each of these ceramic solutions has the ability to remain strong against wear. Whether you wish to use them in chemical engineering and processing or a different application altogether, their attributes will ensure they are the right choice of material for you. Speak with our experts now for more information on the ceramic solutions we can provide.