Wire braiding, a specialised process used in industries from aerospace to telecommunications, has undergone significant advancements in recent years—particularly through the integration of technical ceramics. Materials like sialons and silicon nitride are advantageous for the wire braiding industry owing to their high performance under extreme conditions. Here, we’ll explore how ceramic innovations support efficiency, longevity, and performance improvements in wire braiding applications.
Traditional Ceramic Applications in Wire Braiding
Precision handling is essential in the wire braiding process. Ceramic materials, with their high hardness, wear resistance, and chemical stability, offer ideal solutions for managing this demanding process. Some of the traditional uses of ceramics in wire braiding include:
- Wire Guides and Eyelets: Ceramic wire guides and eyelets reduce friction, facilitating smooth passage and reducing wear on wires. This results in higher-quality braids and extends component life. Ceramics with a low friction coefficient excel in this role by resisting abrasion and maintaining their properties even at high speeds.
- Tensioning Components: Tension is crucial for achieving uniform braids. Ceramic tension wheels and pulleys maintain consistent tension without succumbing to wear and tear, as they are engineered to withstand high temperatures and prolonged stress without deformation.
These traditional applications have long supported reliable wire braiding operations. However, new advancements in ceramics are pushing the performance of these components even further.
Recent Ceramic Innovations Transforming Wire Braiding
Modern advancements in technical ceramics have led to novel applications that enhance the efficiency and longevity of wire braiding components. These innovations address several industry demands, including higher-speed operations, customization, and improved wear resistance.
1. Enhanced Thermal Stability and Reduced Brittleness
Recent breakthroughs have resulted in ceramics that better tolerate rapid temperature changes and exhibit improved toughness. Traditional ceramics could be brittle, a drawback that limited their use in high-speed applications where rapid stress changes could lead to fracturing. However, newer ceramic materials, including modified sialons and silicon nitride, resist cracking, even at high temperatures. This enhanced durability is essential for modern wire braiding machinery, which operates at ever-increasing speeds to meet production demands.
2. Additive Manufacturing of Custom Ceramic Components
The rise of 3D printing is set to revolutionise ceramic manufacturing. Today, prototype ceramic parts can be 3D-printed with complex geometries, offering precise, custom designs tailored to specific machine requirements. This customizability could be extremely beneficial for wire braiding components, where precise shapes and features are essential for guiding and tensioning wires. Rapid prototyping also reduces lead times, making it feasible to iterate designs and optimize performance faster than ever before.
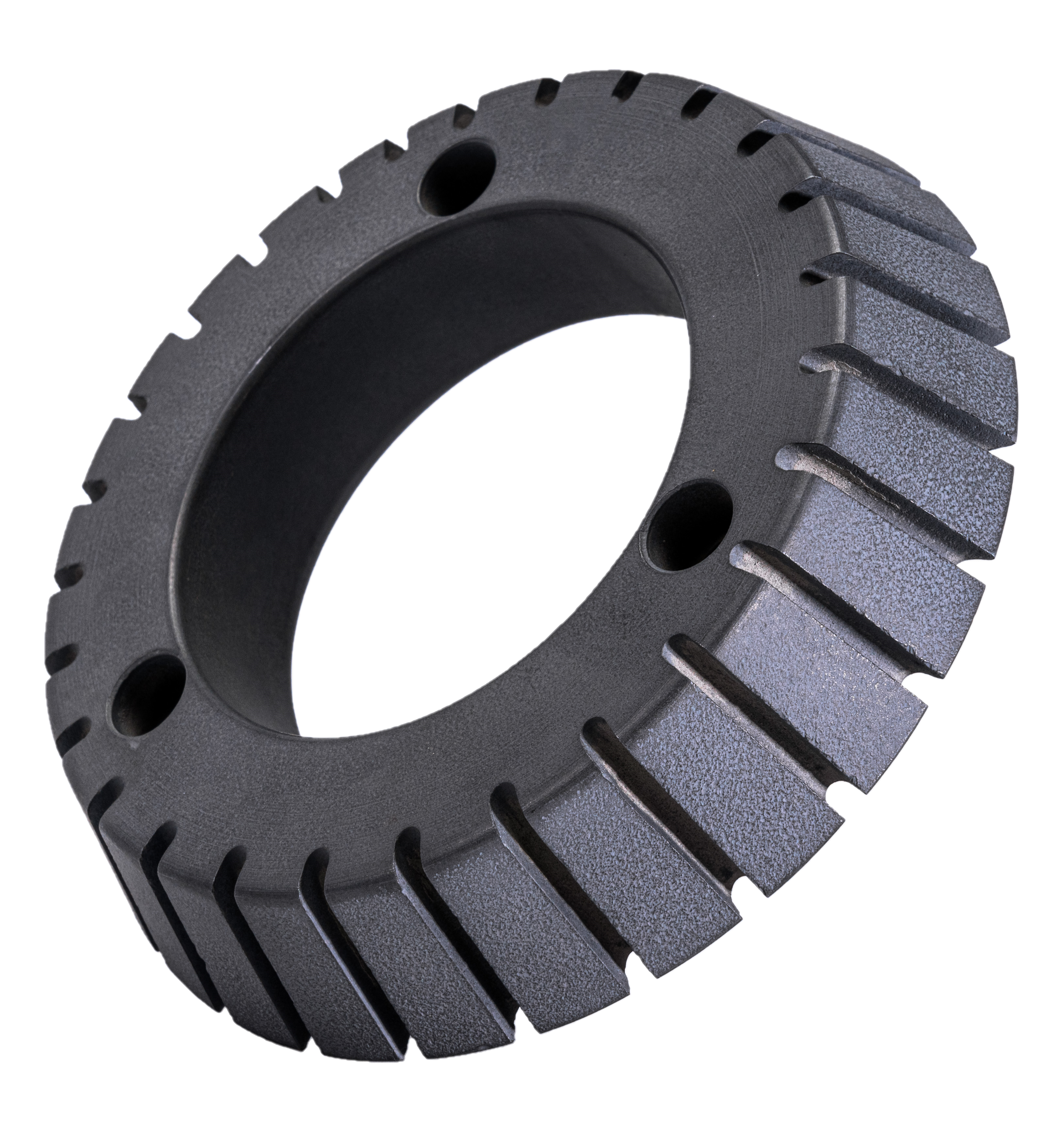
Wear resistance sialon tooling. Image Credit: International Syalons (Newcastle) Ltd.
Why Choose Sialons and Silicon Nitride for Wire Braiding?
Among the various types of technical ceramics available, sialons and silicon nitride stand out as materials of choice in wire braiding due to their unique properties:
- High Hardness and Wear Resistance: Both sialons and silicon nitride exhibit exceptional hardness, making them suitable for components that endure continuous contact with wires. This resistance to wear and abrasion allows them to maintain performance and structure even with frequent use.
- Low Friction Coefficient: These ceramics facilitate smooth wire movement, enhancing production efficiency and minimizing abrasion. This low friction coefficient is a key reason they are chosen over other materials in wire braiding components.
- Thermal Stability: Sialons and silicon nitride can endure high temperatures without degradation, allowing them to support high-speed braiding processes that generate significant heat. This stability ensures that components remain functional under the intense demands of modern wire braiding operations.
The Future of Ceramics in Wire Braiding
As the wire braiding industry continues to demand materials that can withstand higher speeds, increased tension, and complex braiding patterns, ceramics are expected to remain at the forefront. Innovations in ceramic materials and manufacturing techniques, such as additive manufacturing and advanced surface engineering, will further strengthen the role of ceramics in this industry.
In the near future, we anticipate the development of even tougher ceramic materials with enhanced resistance to thermal shock and brittleness, further enabling high-speed operations. Additionally, advances in coating technology are likely to result in surfaces with near-zero friction, drastically improving component lifespans and minimizing wire abrasion.
Final Thoughts
The integration of sialons, silicon nitride, and other advanced ceramics in wire braiding marks a transformative shift, helping meet the high-performance demands of modern industry. With customization options and longevity-enhancing innovations, technical ceramics enable wire braiding machines to operate more efficiently and with less maintenance. As research into these materials progresses, ceramics will undoubtedly continue to push the boundaries of what is possible in wire braiding applications.
For more insights into how International Syalons’ advanced ceramic solutions can enhance your wire braiding operations, connect with our experts and explore how our tailored ceramic components can support your production goals.