High-voltage plasma arcs are indispensable in water treatment, industrial cleaning, waste processing, and more. These industries rely on arc plasma technology to generate intense energy bursts that drive essential chemical and physical processes. However, one significant challenge associated with plasma arcs is the generation of powerful shock waves, which can severely damage electrical insulators at the cathode and anode.
When insulators fail, they can cause equipment downtime, expensive repairs, and reduced operational efficiency. Preventing these failures is essential for maintaining high-performance plasma systems. This article explores how shock waves contribute to insulator failure and how material selection and system design improvements can mitigate the risks.
The Science Behind Plasma Arcs and Shock Waves
How a Plasma Arc Forms in Water
A high-voltage pulse applied to water generates an ionized plasma channel, forming a highly conductive pathway for electrical discharge. This plasma arc expands rapidly, leading to a sudden increase in pressure. The expansion creates a shock wave, which propagates through the water at speeds of approximately 1.5 km/s.
As the shock wave interacts with the surrounding environment, it reflects off boundaries and generates secondary pressure waves. These waves can amplify stresses within the system, particularly in confined spaces such as reactors or cathode assemblies, putting enormous strain on electrical insulators.
The Role of Shock Waves in Material Failure
- Extreme pressure pulses (~260 MPa) exert enormous forces on surrounding components, including electrical insulators.
- Reflected waves within confined systems amplify mechanical stress, causing fatigue in brittle materials.
- Repeated stress cycles contribute to the formation of microcracks, which progressively grow, leading to catastrophic failure.
- Alumina (Al₂O₃) insulators, though commonly used for their high-temperature resistance, are inherently brittle and susceptible to damage under extreme shock wave exposure.
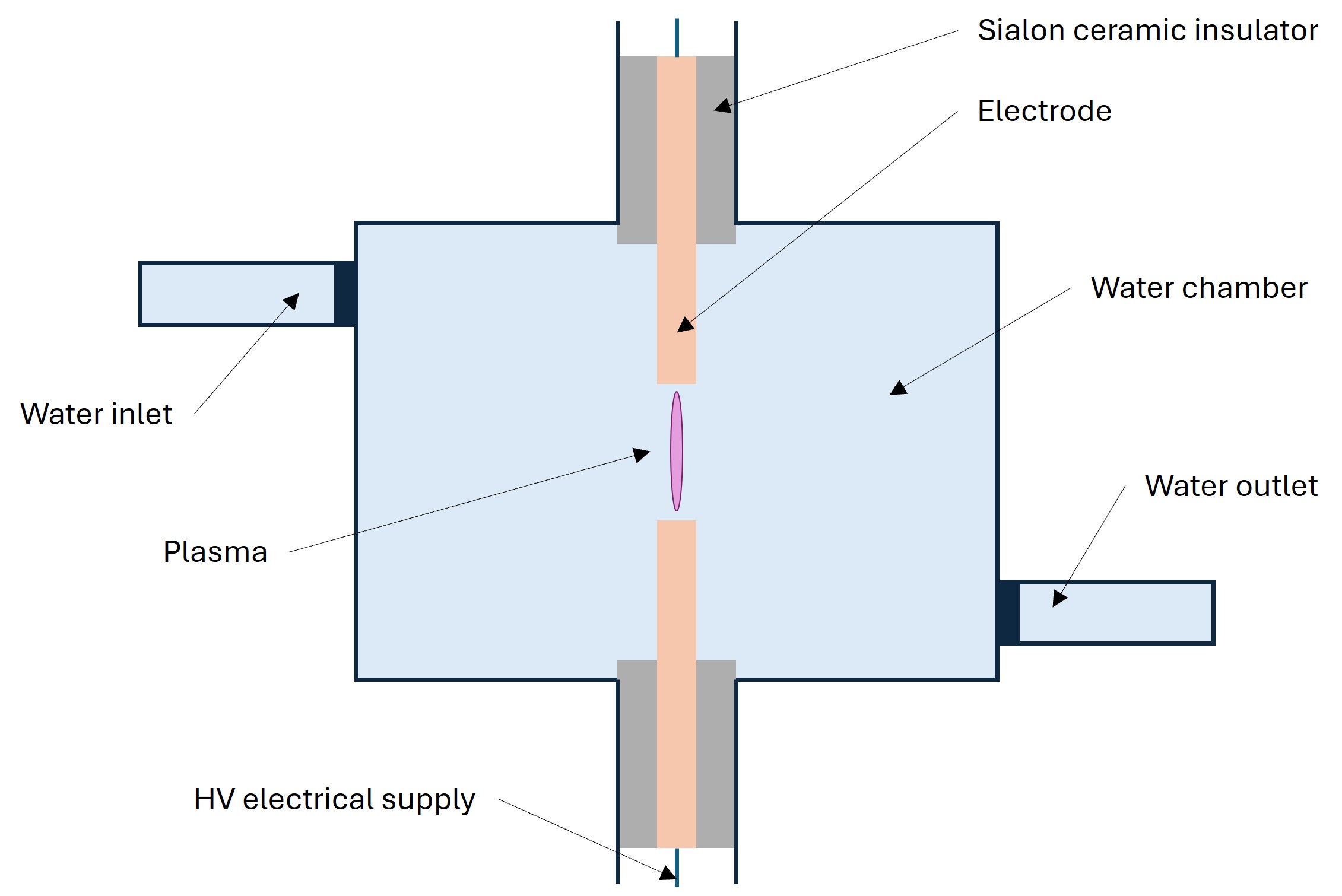
A typical arc plasma water treatment process schematic. Image Credit: International Syalons (Newcastle) Ltd
Case Study: Why Alumina Insulators Failed in a Plasma System
The Problem: Brittle Failure Under Repeated Shock Waves
One of our clients experienced unexpected failures in their plasma system due to the degradation of alumina insulators installed at the cathode and anode. During operation, shock waves induced rapid microcracking, which worsened over time due to secondary wave reflections. Eventually, these microcracks led to structural failure, necessitating frequent replacements and causing expensive operational downtime.
The Solution: Switching to Silicon Nitride (Sialon) Insulators
To address this issue, we recommended replacing alumina insulators with sialon (silicon nitride-based) insulators, which offer superior mechanical properties:
- Higher fracture toughness (6-7 MPa⋅m½) vs. alumina (3-4 MPa⋅m½) → More resistance to crack propagation.
- Better energy absorption → Can withstand repeated high-pressure pulses without degradation.
- Maintains electrical insulation → No compromise on system performance.
The result? Longer-lasting insulators, reduced maintenance costs, and increased system reliability.
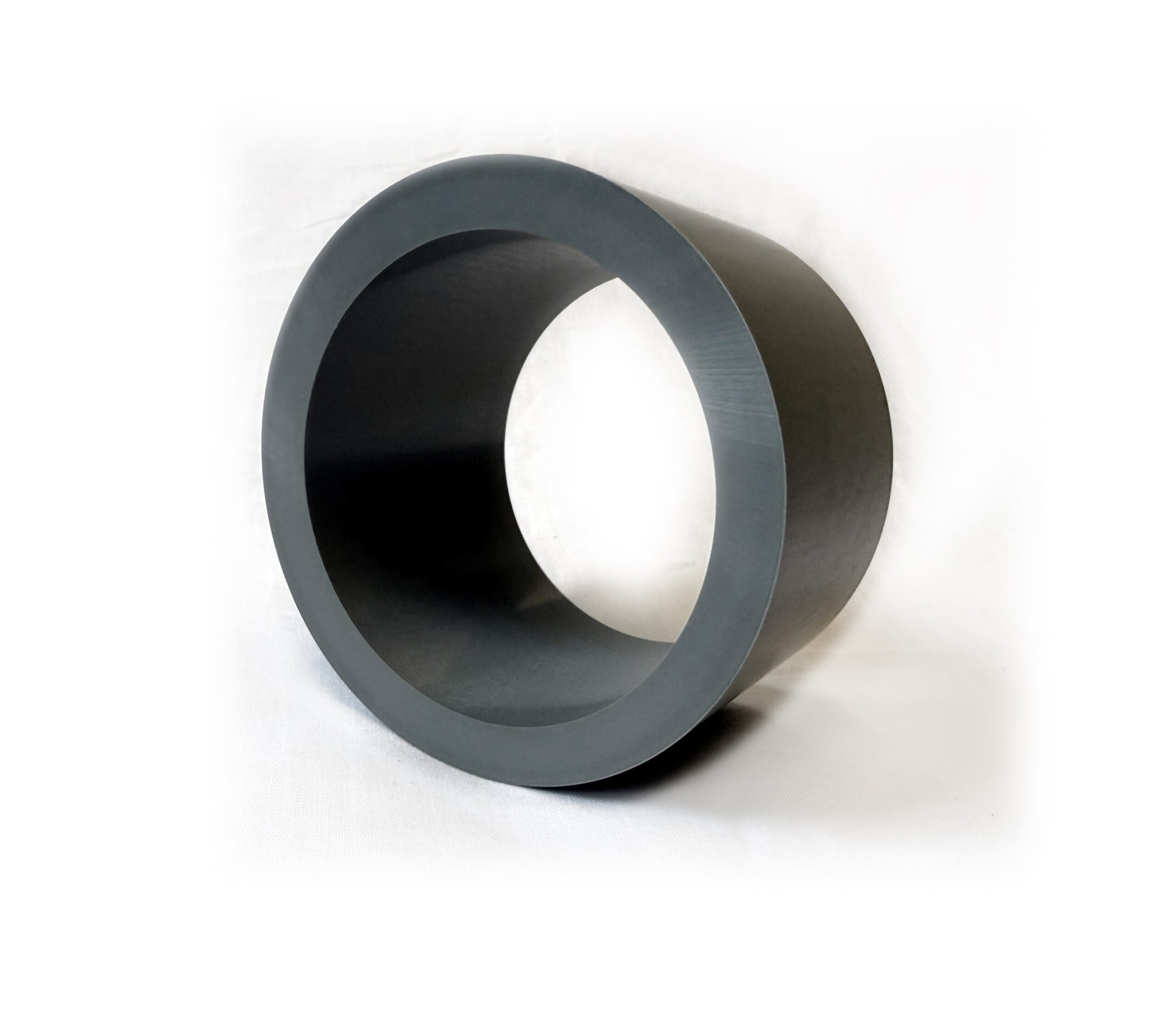
A high strength Sialon electrical insulator used in arc plasma water treatment. Image Credit: International Syalons (Newcastle) Ltd.
How to Prevent Insulator Failure in High-Voltage Plasma Systems
1. Choose the Right Insulator Material
- Alumina: Suitable for low-impact environments but prone to brittle failure under repeated shock waves.
- Silicon Nitride (Sialon): Ideal for high-shock environments due to its superior fracture toughness and durability.
2. Optimize System Design to Reduce Shock Wave Impact
- Modify boundary conditions: Implement damping structures or coatings to absorb wave energy.
- Adjust electrode positioning: Minimize direct wave impact on insulators.
- Use Computational Fluid Dynamics (CFD) simulations (e.g., OpenFOAM) to model and optimize pressure wave distribution within the system.
3. Monitor for Early Signs of Failure
- Install high-speed sensors to track pressure wave behaviour in real-time.
- Conduct regular inspections to detect microcracks before they lead to failure.
- Implement predictive maintenance strategies based on shock wave impact data.
Smarter Materials & Design for Longer-Lasting Insulators
High-voltage plasma systems inherently generate shock waves, but insulator failure is preventable with the right approach. Our experience demonstrated that switching from alumina to sialon insulators significantly improved durability and reduced maintenance demands. Additionally, design modifications and predictive monitoring can further extend insulator’s lifespan and enhance system reliability.
By understanding how shock waves interact with materials and applying advanced material science solutions, we can build more robust and efficient plasma systems that operate reliably in high-impact environments.
For more insights on advanced ceramic solutions for high-voltage applications, contact us today.