Wire and cable drawing is a fundamental manufacturing process used to produce precisely sized metal wires for applications in telecommunications, automotive, aerospace, and construction. The process involves pulling metal through a series of dies to reduce its diameter while ensuring uniformity. However, the extreme stress, friction, and heat generated in the wire and cable drawing process place significant demands on the materials used for drawing dies, guides, and capstans.
Traditional materials like tungsten carbide, while durable, suffer from wear over time. This leads to frequent replacements and increased operational costs. Advanced ceramics, Silicon Nitride (Si₃N₄), Sialon (Si-Al-O-N), Zirconia (ZrO₂), Alumina (Al₂O₃), and Silicon Carbide (SiC), offer a superior alternative. The exceptional hardness, wear resistance, and thermal stability of these advanced ceramics make them indispensable in improving efficiency, extending tool life, and enhancing the quality of drawn wire.
The Essential Role of Advanced Ceramics in Wire and Cable Drawing
Wire and cable drawing demands materials that can withstand continuous mechanical stress, extreme temperatures, and prolonged exposure to lubricants. Advanced ceramics provide the durability, heat resistance, and precision needed to maintain consistent wire quality, extend tool life, and optimise production efficiency. Their unique combination of mechanical strength and chemical stability makes them a key material for high-performance manufacturing environments.
Wear Resistance and Tool Longevity
Wire drawing subjects dies, guides, and pulleys to relentless wear, which can degrade tool performance over time. Advanced ceramics like Silicon Carbide and Alumina excel in resisting abrasion, allowing components to maintain precision far longer than metal alternatives. This extended lifespan minimises downtime, reduces maintenance costs, and ensures consistent wire quality throughout production cycles.
Thermal Stability and High-Speed Performance
Extreme temperatures during high-speed wire drawing can lead to warping and dimensional instability in conventional materials. The advanced ceramics Sialon and Silicon Nitride maintain structural integrity under intense heat, ensuring reliable performance in demanding operations. Their ability to resist thermal shock prevents deformation, ensuring reliable performance under extreme conditions. Additionally, Zirconia’s low thermal conductivity helps regulate temperature fluctuations, reducing the risk of premature tool failure.
Reduced Friction for Enhanced Wire Quality
Excessive resistance between the wire and drawing components can result in surface imperfections and energy inefficiencies. Thanks to their low-friction surfaces, Sialon and Silicon Nitride enable a smoother wire drawing process with minimal resistance. This leads to improved wire quality, reduced wear on tools, and increased production efficiency.
Corrosion Resistance in Lubricated Drawing Environments
Exposure to lubricants and coolants can accelerate material degradation in traditional metal dies. Silicon Carbide and Zirconia offer exceptional resistance to corrosion and oxidation, ensuring consistent performance in wet drawing operations. The chemical stability of these advanced ceramics makes them well-suited for processing coated and specialty wires, reducing contamination risks and extending service life.
Precision and Uniformity in Ultra-Fine Wire Drawing
For industries requiring ultra-fine wires, such as fiber optics and medical devices, absolute precision is crucial. Zirconia dies maintain sharp edges longer than metal counterparts, ensuring consistent wire diameters and flawless surface finishes. Similarly, Alumina rollers and capstans provide stable, vibration-free wire handling, further improving process control.
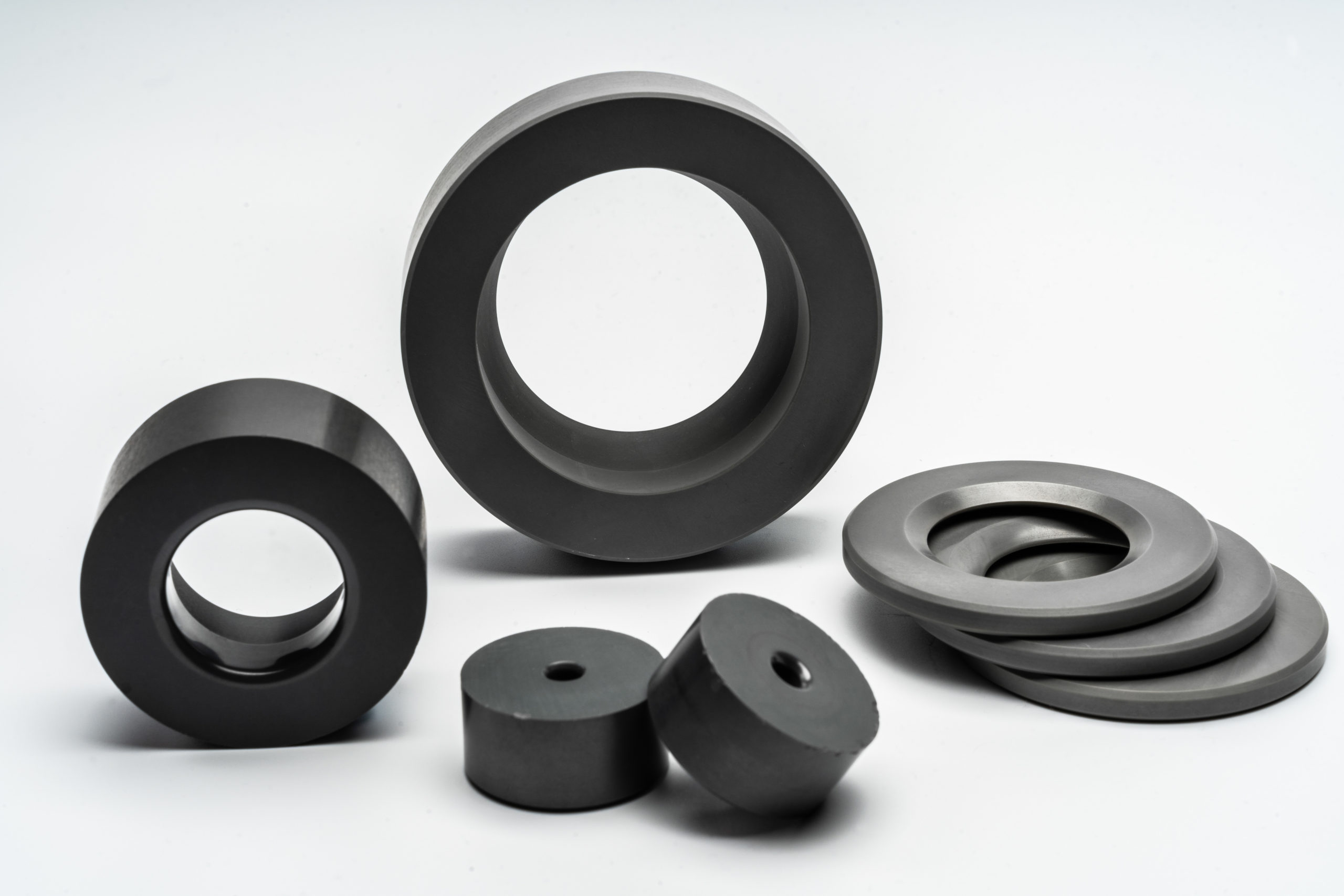
Silicon nitride extrusion dies. Image Credit: International Syalons (Newcastle) Ltd.
How Advanced Ceramics Improve Wire and Cable Drawing Performance
Achieving high precision, durability, and operational efficiency in wire and cable drawing depends on the materials used in critical components. Advanced ceramics enhance the performance of dies, guides, capstans, and coating systems, enabling higher productivity, reduced maintenance, and superior product quality. The use of these advanced ceramics has become essential for manufacturers looking to improve process reliability and production output.
Enhancing the Functionality of Drawing Dies and Guides
Dies are fundamental to shaping and reducing wire diameters, making their durability crucial for maintaining precision. Ceramic dies made from Zirconia and Silicon Carbide hold their form under extreme pressure, ensuring tight dimensional tolerances and extended tool life. Their smooth, wear-resistant surfaces also help maintain wire integrity, reducing defects and breakage.
Optimising Wire Handling with Ceramic Capstans and Rollers
Capstans and rollers control the movement and tension of wires during drawing. Alumina and Silicon Nitride capstans withstand prolonged use in high-speed operations, offering superior resistance to wear and thermal stress. These heat dissipation properties prevent overheating, which helps maintain wire consistency and process stability.
Improving Coating and Insulation Processes
Controlled, high-temperature environments are vital for applying coatings such as enamel, tin, and polymer insulation to wires. To ensure uniform application without contamination, Zirconia and Silicon Carbide crucibles provide chemical resistance and thermal stability. Their durability enhances product reliability, particularly in applications where corrosion resistance is critical.
Supporting Extrusion and Insulation Applications
During polymer extrusion and insulation, ceramic nozzles and guides ensure precise application of protective layers. Silicon Nitride and Sialon nozzles resist wear and chemical attack, maintaining uniform coatings for high-performance cables. Their precision makes them crucial for telecommunications and power transmission applications.
Advanced Ceramics from International Syalons for High-Performance Wire and Cable Drawing
At International Syalons, we specialise in advanced ceramics, designing high-performance components that enhance efficiency, durability, and precision in wire and cable drawing. Our advanced ceramics, Silicon Nitride, Sialon, Zirconia, Alumina, and Silicon Carbide, help manufacturers reduce tool wear, improve wire quality, and minimise downtime. To support these benefits, we design custom-engineered dies, capstans, guides, and extrusion nozzles that withstand the demands of modern production. Contact International Syalons today to learn how our advanced ceramics can optimise your wire and cable drawing processes.