Ceramics have transformed wire and cable manufacturing, making it possible to produce stronger, more heat-resistant, and longer-lasting components. But innovation comes with obstacles. Brittleness, high production costs, and thermal expansion mismatches can limit their use in wire and cable applications. Rather than barriers, these challenges are driving advancements in ceramic formulations, processing techniques, and hybrid materials, ensuring ceramics continue to push the industry forward.
Why Ceramics Are Critical to Wire and Cable Manufacturing
Few materials offer the mechanical strength, heat resistance, and electrical insulation of ceramics. These properties make them essential in wire and cable applications, where components must endure constant friction, extreme temperatures, and electrical loads without degrading. Ceramics are particularly valued for their:
- Wear Resistance – Zirconia and alumina withstand prolonged metal contact, extending the lifespan of wire drawing dies and cable guides.
- Electrical Insulation – Alumina prevents electrical discharge, ensuring safe, high-voltage transmission.
- High-Temperature Stability – Silicon carbide and Sialon remain structurally sound under extreme heat, protecting wiring in furnaces, aerospace, and power grids.
- Corrosion and Low-Friction Properties – Unlike metals and polymers, ceramics resist harsh environments and do not require lubrication. This makes them ideal for high-speed cable manufacturing.
Although ceramics excel in these areas, their integration into wire and cable systems presents engineering challenges that require innovative solutions.
Challenges in Ceramic Applications and the Engineering Solutions Addressing Them
There are many significant advantages that come with using ceramics in wire and cable manufacturing. However their widespread use is limited by several material and processing challenges. Overcoming these obstacles is essential to fully unlocking their potential.
1. Managing Brittleness and Impact Sensitivity
One of the most well-known limitations of ceramics is their lack of flexibility. Unlike metals, which deform under stress, ceramics tend to crack or shatter when subjected to impact or sudden force. This makes them vulnerable in wire and cable manufacturing, especially in high-speed wire drawing and cable production equipment, where rapid mechanical forces are common.
Engineering Solutions for Greater Durability:
- Toughened Ceramic Formulations – Advanced materials like yttria-stabilised zirconia (YSZ) and silicon nitride (Si₃N₄) offer greater fracture resistance than traditional alumina.
- Hybrid Metal-Ceramic Components – Combining ceramics with metal backings allows them to absorb impact without sacrificing wear resistance.
- Optimised Stress Distribution – Engineers are refining component geometries to minimise weak points and improve structural integrity.
Enhancing fracture toughness and designing components to distribute stress more effectively is making ceramics more reliable in high-impact applications.
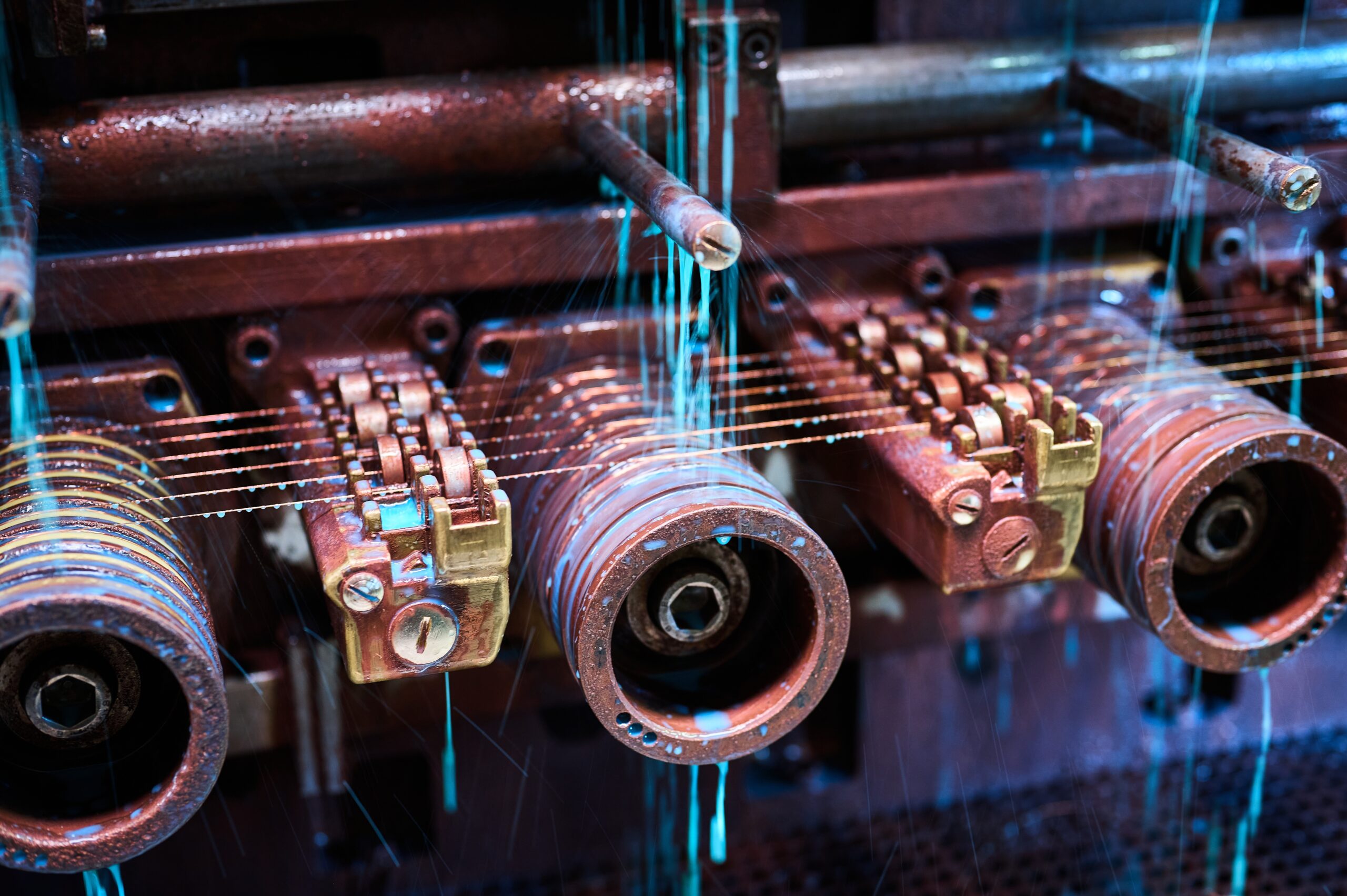
Copper wire drawing. Image Credit: Shutterstock
2. Reducing Manufacturing Costs Without Compromising Performance
The production of high-performance ceramics is expensive due to specialised raw materials, high-temperature sintering, and precision machining requirements. These costs have historically made ceramics less accessible for widespread use in the wire and cable industry.
Innovations Driving Cost Reduction:
- Near-Net-Shape Manufacturing – Ceramic injection molding and 3D printing reduce material waste and minimise costly post-processing.
- Automation in Ceramic Processing – AI-driven ceramic sintering and finishing techniques improve efficiency, lower labor costs, and enhance consistency.
Advances in manufacturing are making ceramic components more economically viable for large-scale industrial applications.
3. Preventing Thermal Shock and Cracking in Extreme Environments
Ceramics perform well in wire and cable applications that require high-temperature resistance, but rapid temperature changes can cause them to crack due to thermal expansion and contraction. This is particularly problematic in wire and cable manufacturing, where components such as wire processing equipment, high-temperature insulation, and power transmission systems must endure fluctuating conditions.
Strategies to Improve Thermal Stability:
- Thermal Shock-Resistant Ceramics – Silicon nitride and Sialon ceramics exhibit superior resistance to cracking under extreme temperature changes.
- Controlled Thermal Processing – Implementing gradual heating and cooling protocols during manufacturing minimises the risk of sudden thermal expansion or contraction.
As ceramic formulations continue to improve, they’re becoming more adaptable for high-speed, high-temperature industrial applications.
4. Extending Wear Life in High-Friction Applications
Even with exceptional hardness, ceramics can gradually degrade when exposed to prolonged friction. In wire and cable manufacturing, applications such as wire drawing dies and cable guides experience lengthy metal-on-ceramic contact, which can lead to surface erosion and reduced efficiency.
Breakthroughs in Wear Resistance:
- Advanced Surface Coatings – Diamond-like carbon (DLC) coatings strengthen ceramic surfaces against long-term wear.
- Self-Lubricating Ceramics – Some formulations now incorporate lubricating phases, reducing friction and extending component lifespan.
- Improved Component Design – Rotating and self-aligning ceramic guides ensure even wear distribution, preventing localised damage.
These improvements ensure that ceramic components maintain their performance in high-friction applications, reducing maintenance costs and downtime.
5. Addressing Thermal Expansion Mismatch in Hybrid Components
Many wire and cable applications require ceramics to be combined with metals. However differences in thermal expansion rates can produce stress at material junctions, leading to fractures over time.
Solutions for Seamless Integration:
- Expansion-Matched Ceramics – Zirconia ceramics expand at a rate similar to glass. Thus, they’re ideal for fiber optic alignment sleeves.
- Graded Bonding Interfaces – Transitional layers that gradually shift from ceramic to metal properties prevent stress buildup.
With continued advancements, ceramic-metal interfaces are becoming more durable and reliable for fiber optic and electrical insulation applications.
Unlocking Ceramic Innovation with International Syalons
Ceramics are revolutionising wire and cable manufacturing, offering unmatched durability, insulation, and heat resistance. As advancements continue, they’re becoming more adaptable and cost-effective for demanding applications. International Syalons specialises in high-performance ceramic solutions. Contact us today to discover how we can support your manufacturing needs.