INDUSTRIAL PROCESSING APPLICATIONS
Industrial processing grapples with the harshest conditions. Extreme temperatures. Abrasive materials. Corrosive chemicals. This trifecta can lead to rapid wear and degradation of equipment. Frequent maintenance is an operational headache that increases downtime and cost. Abrasion resistant materials, with their exceptional hardness and chemical stability, offer a solution. Their inherent wear resistance ensures prolonged equipment life, minimizing replacements and disruptions. International Syalons has been supplying a choice of abrasion-resistant materials for industry and manufacturing applications for years. Our technical ceramic materials occupy the pinnacle of wear resistance in challenging application areas.
Advanced ceramics, a fusion of high strength and toughness with pronounced hardness, are the epitome of wear resistant technologies (WRT). Materials such as silicon nitride, sialon, and silicon carbide are not only resistant to corrosion by a spectrum of acids and alkalis but also thrive at high temperatures. This versatility allows them to be integrated into a myriad of wear-resistance applications across industries, including specialty chemicals and basic chemicals. Syalon 101, for instance, boasts an impressive cross-sectional array of physical properties, making it ideal for sliding wear applications or as dewatering foils in paper manufacture. Syalon 050, with its superior hardness, finds its niche in applications like sandblast liners. Meanwhile, Sycarb is the go-to choice for mechanical seals, given its wear resistance.
Zircalon 10, a variant of yttria partially stabilised zirconia, may not rival the wear resistance of Syalon or Sycarb but compensates with unmatched toughness. This makes it a preferred choice in applications experiencing impact, such as weld location pins used in resistance welding of captive nuts to sheet metal.
Industries we serve include specialty chemicals, industrial gases, and more, emphasizing our commitment to delivering high-quality raw materials and solutions for chemical processing industry challenges.
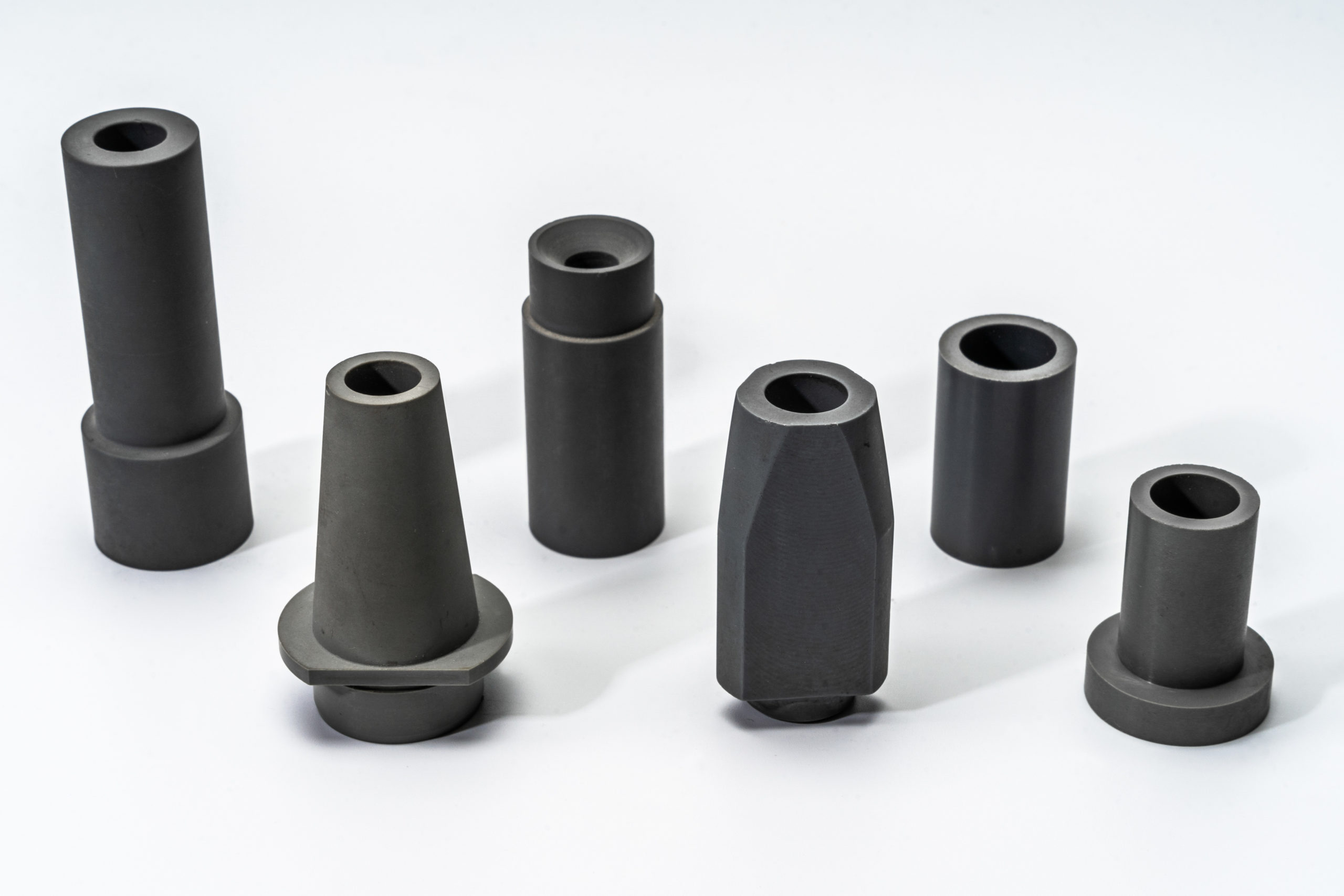
Sialon nozzles, lances and deflectors are often used as a high strength, wear resistant alternatives to tungsten carbide, offering significant consumable and maintenance cost savings through extended tool life.
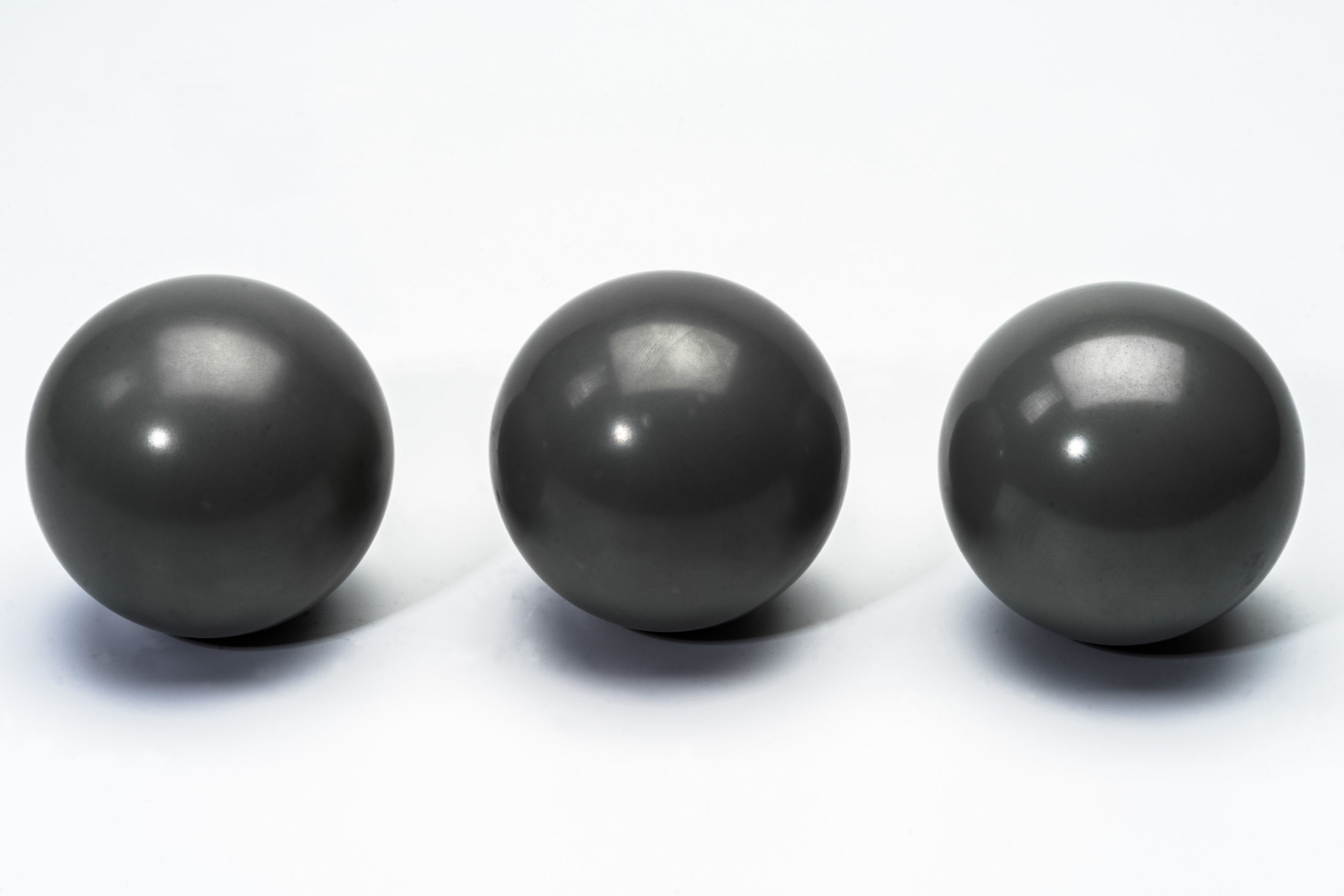
The benefits of high temperature and abrasion resistant Syalon 101 balls for high pressure valves or milling media for powder and slurry preparation include improved control and reduced contamination.
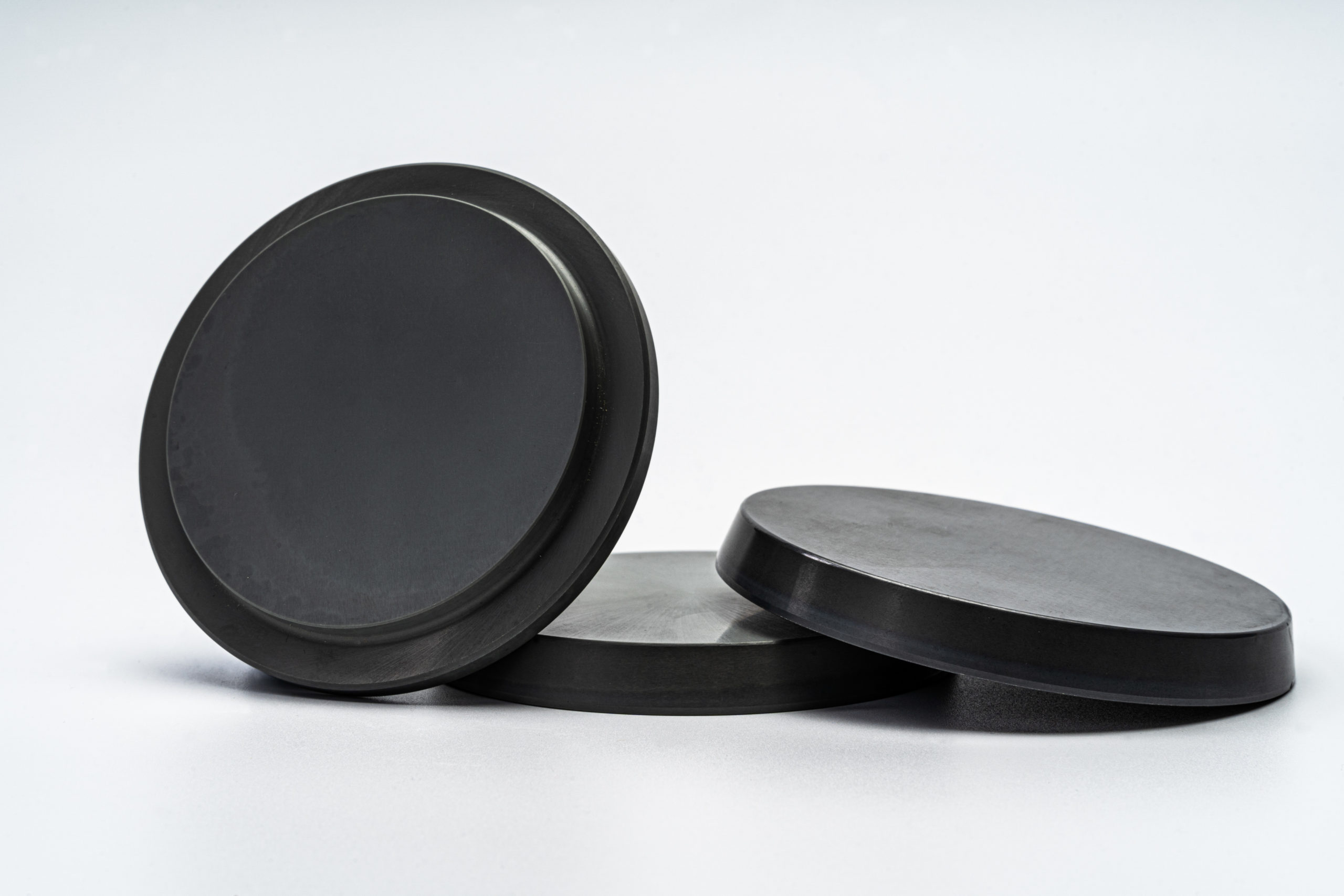
Silicon nitride and sialon stand out as abrasion resistant choices, especially in challenging environments, making them perfect for protective plates in sensor applications.
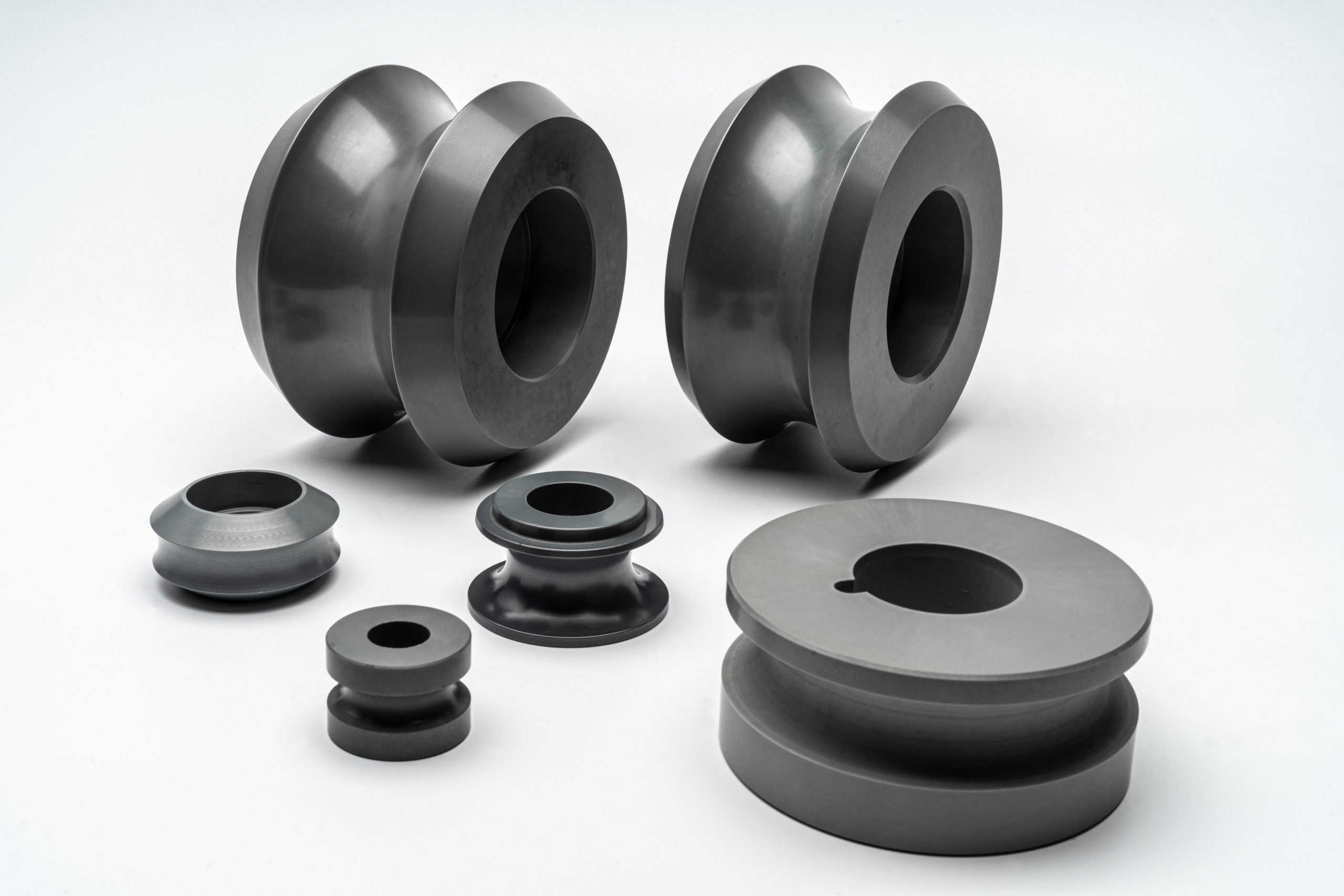
Sialon ceramic welding rollers enhance the surface finish of non-ferrous metal welded tubes, promising faster processing and a longer lifespan than traditional tool steel rolls.
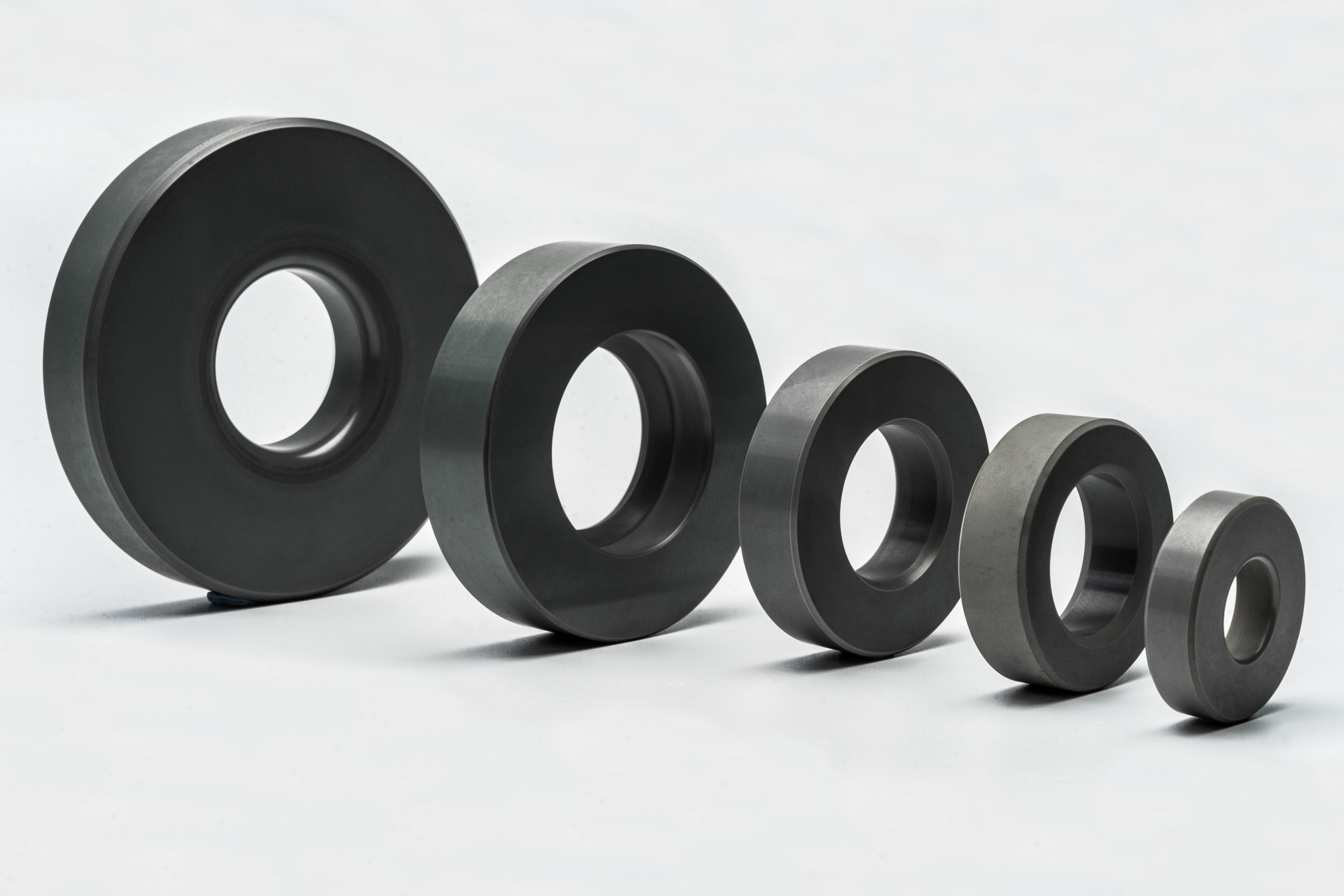
Silicon nitride and sialon dies are pivotal in the extrusion of metals like copper and brass, known for their wear properties and thermal stability.
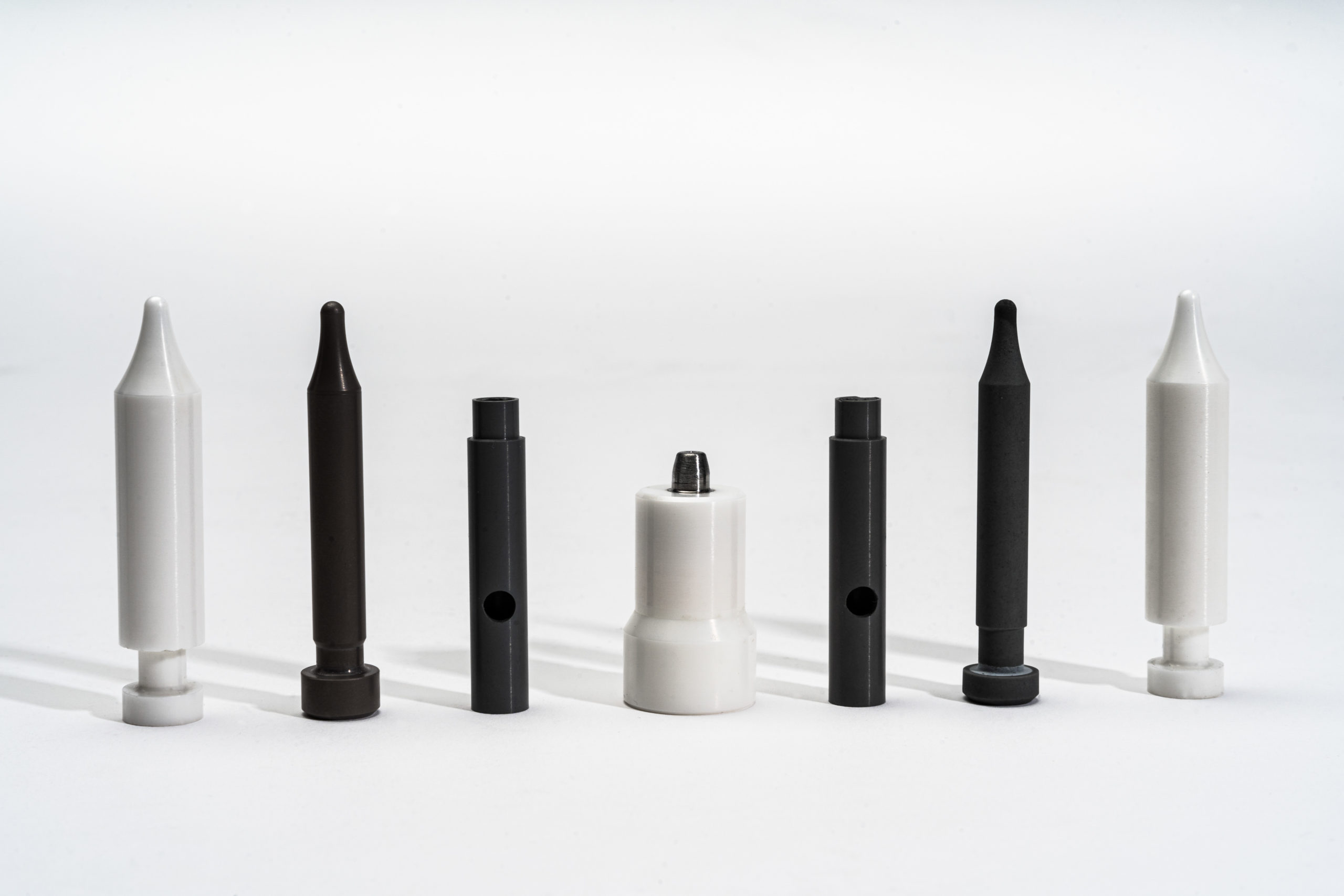
Widely adopted in the automotive sector, silicon nitride and zirconia weld pin solutions offer precision and wear resistance for high-volume robotic welding.
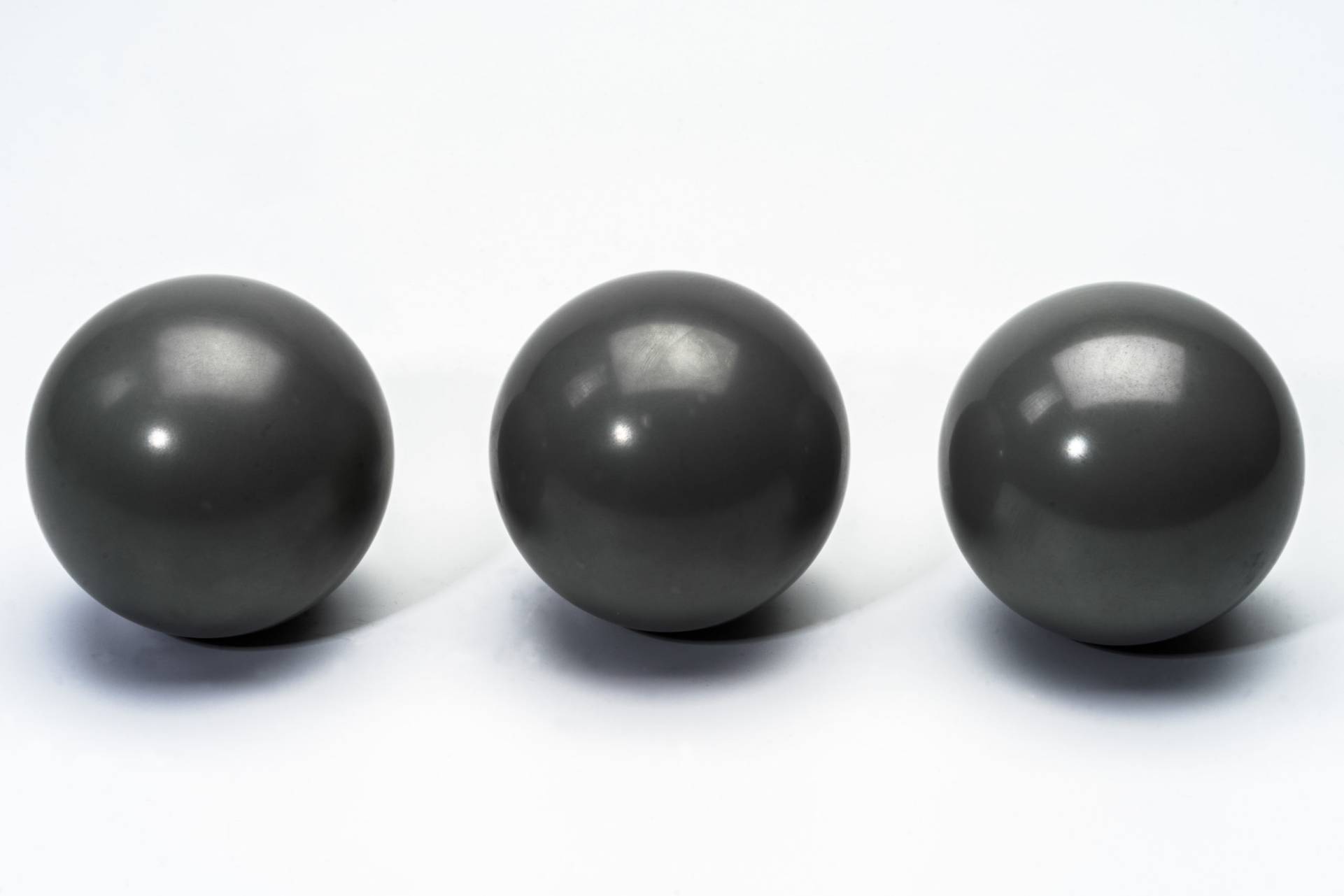
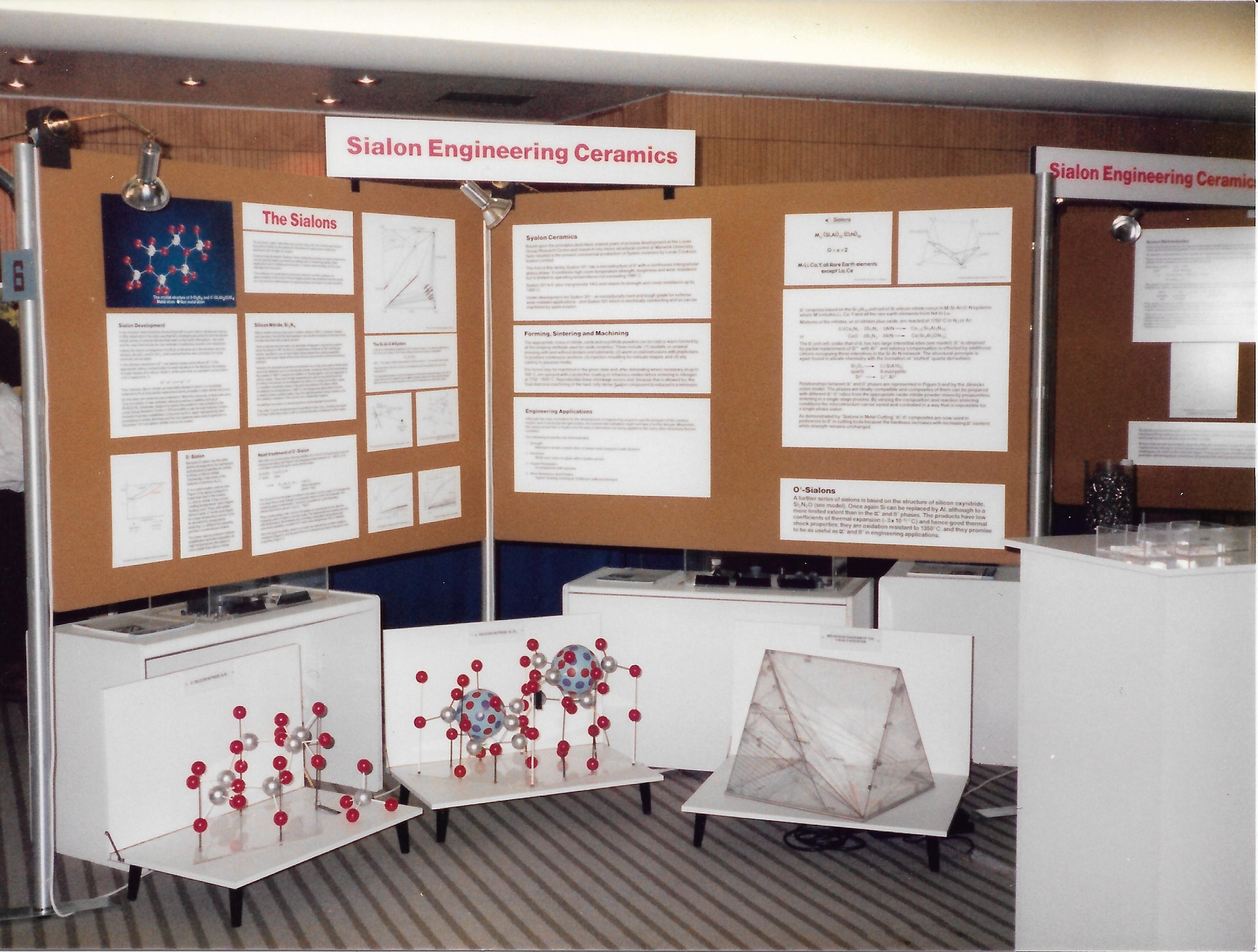
Explore the discovery of sialon ceramics
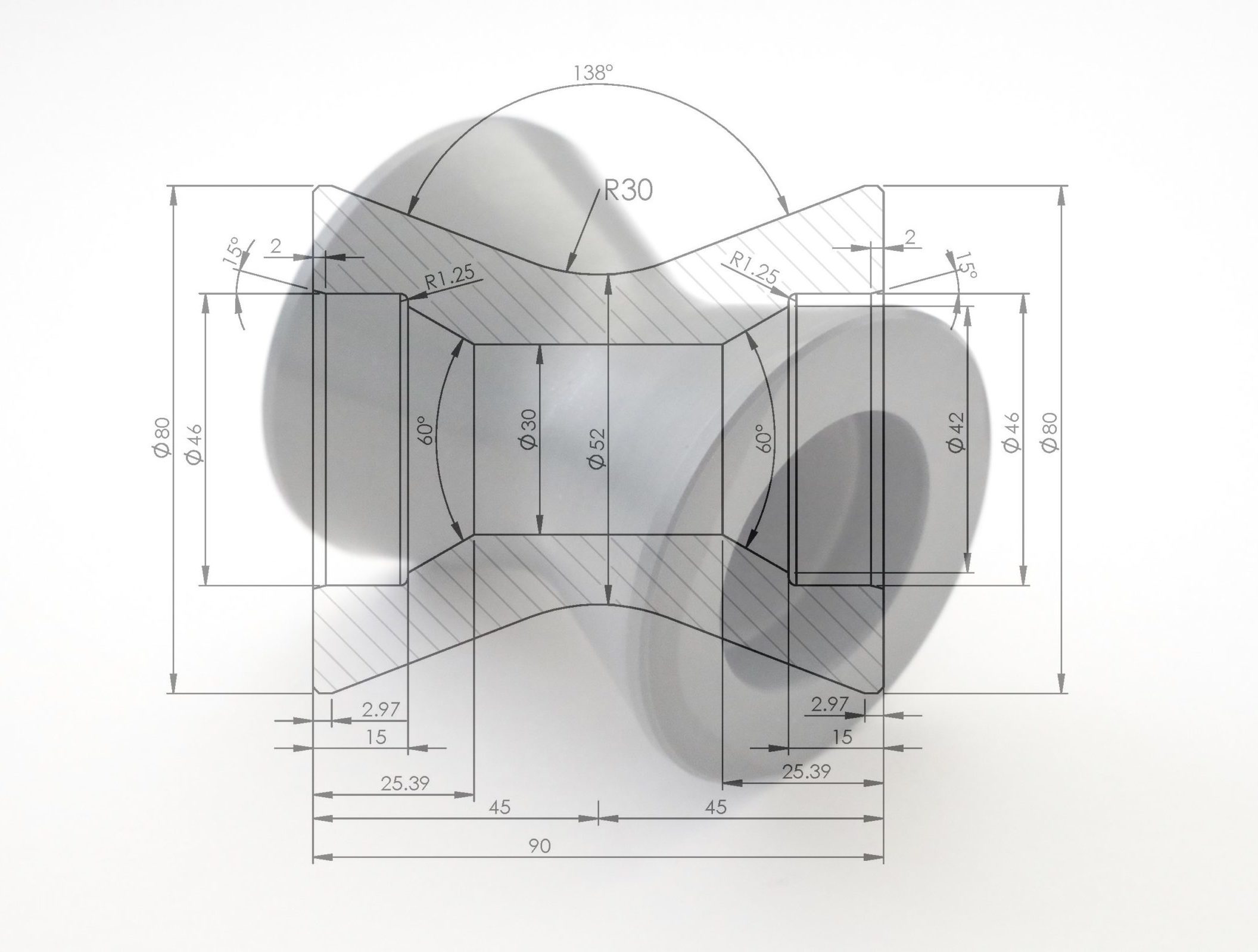
Learn how to design with ceramics
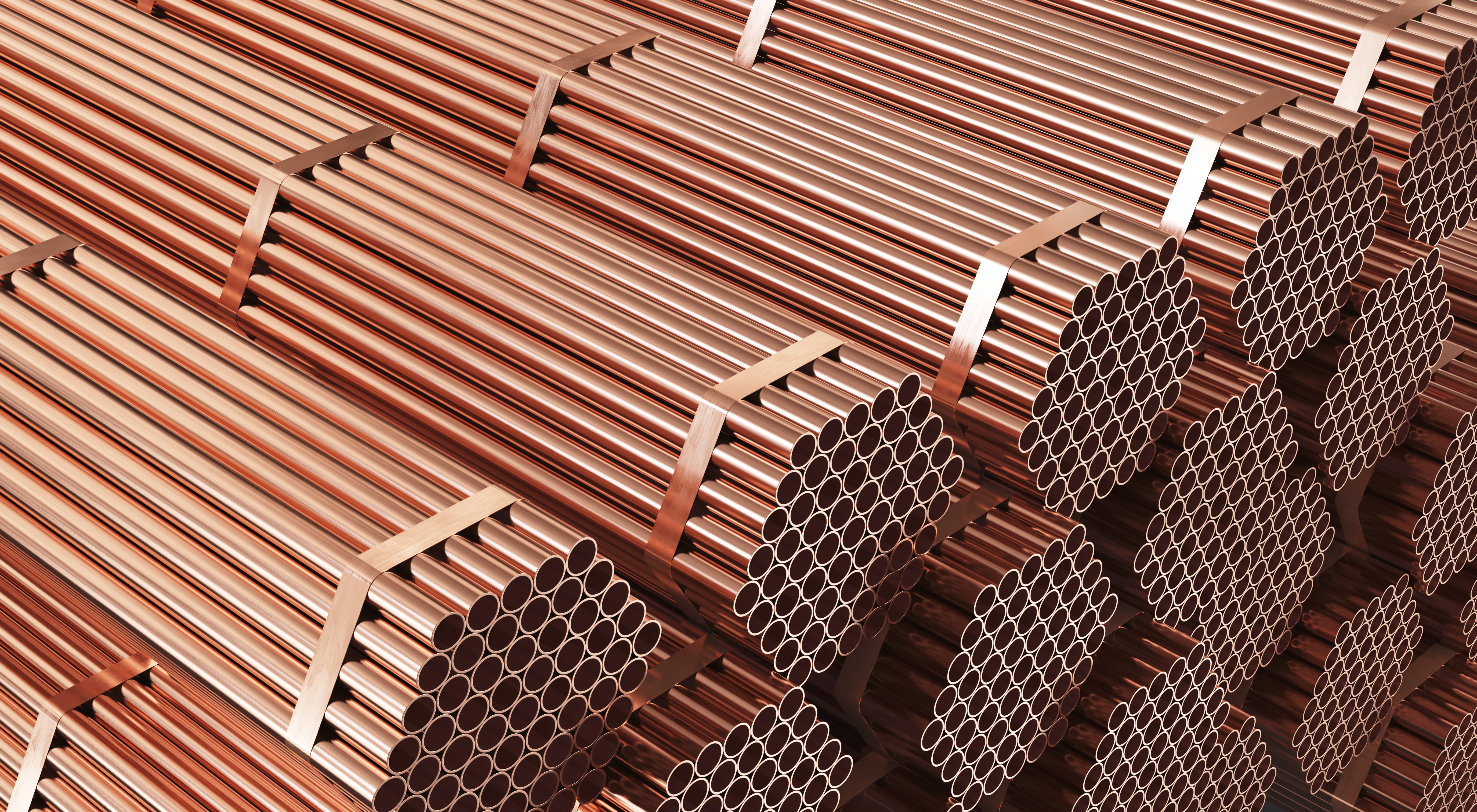
Sialon and zirconia provide the high temperature strength and non-wetting properties necessary for metal casting, extruding, and welding.
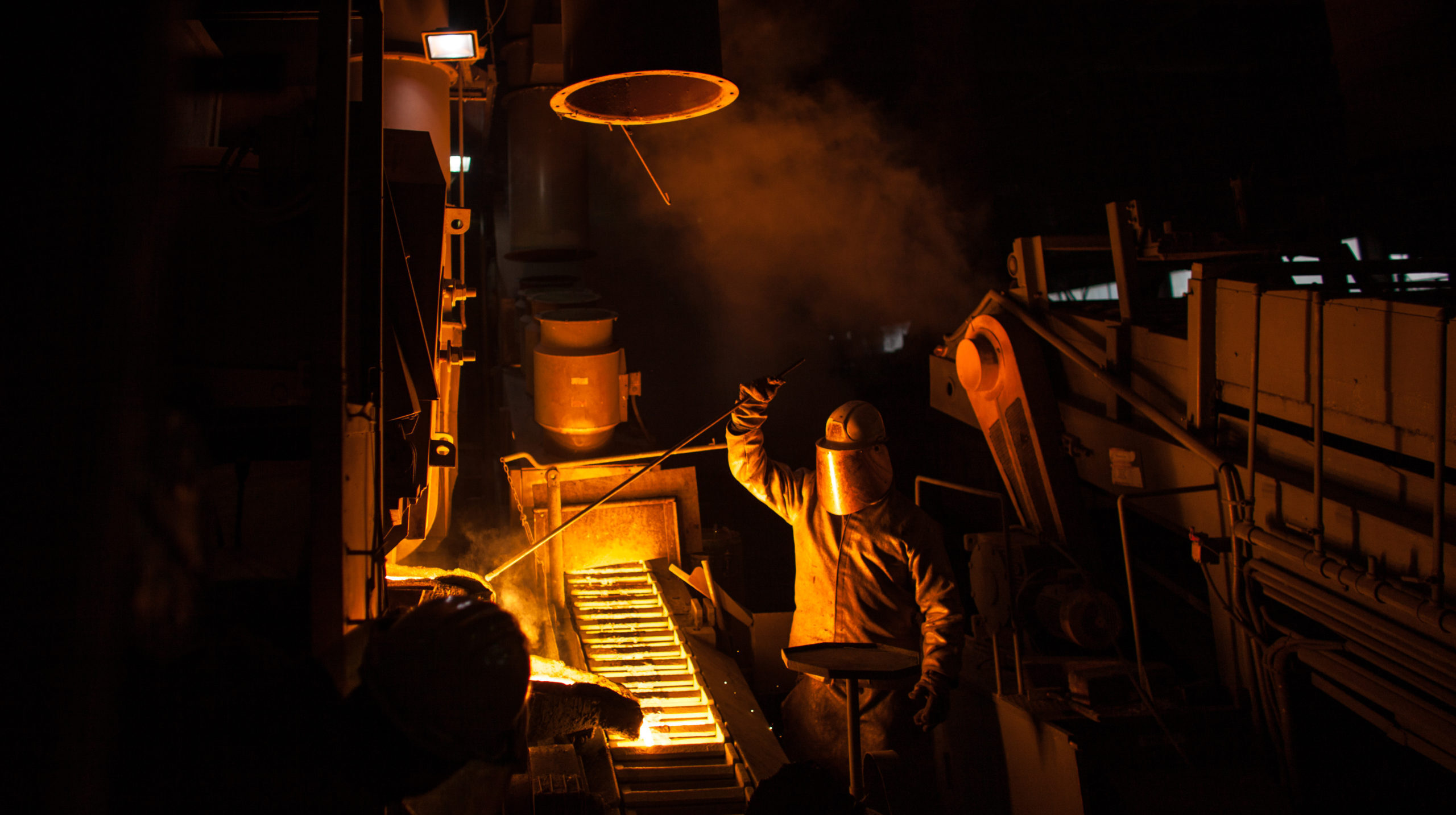
The temperature and corrosion resistance properties of sialon have been utilised in a range of foundry products for molten metal handling.
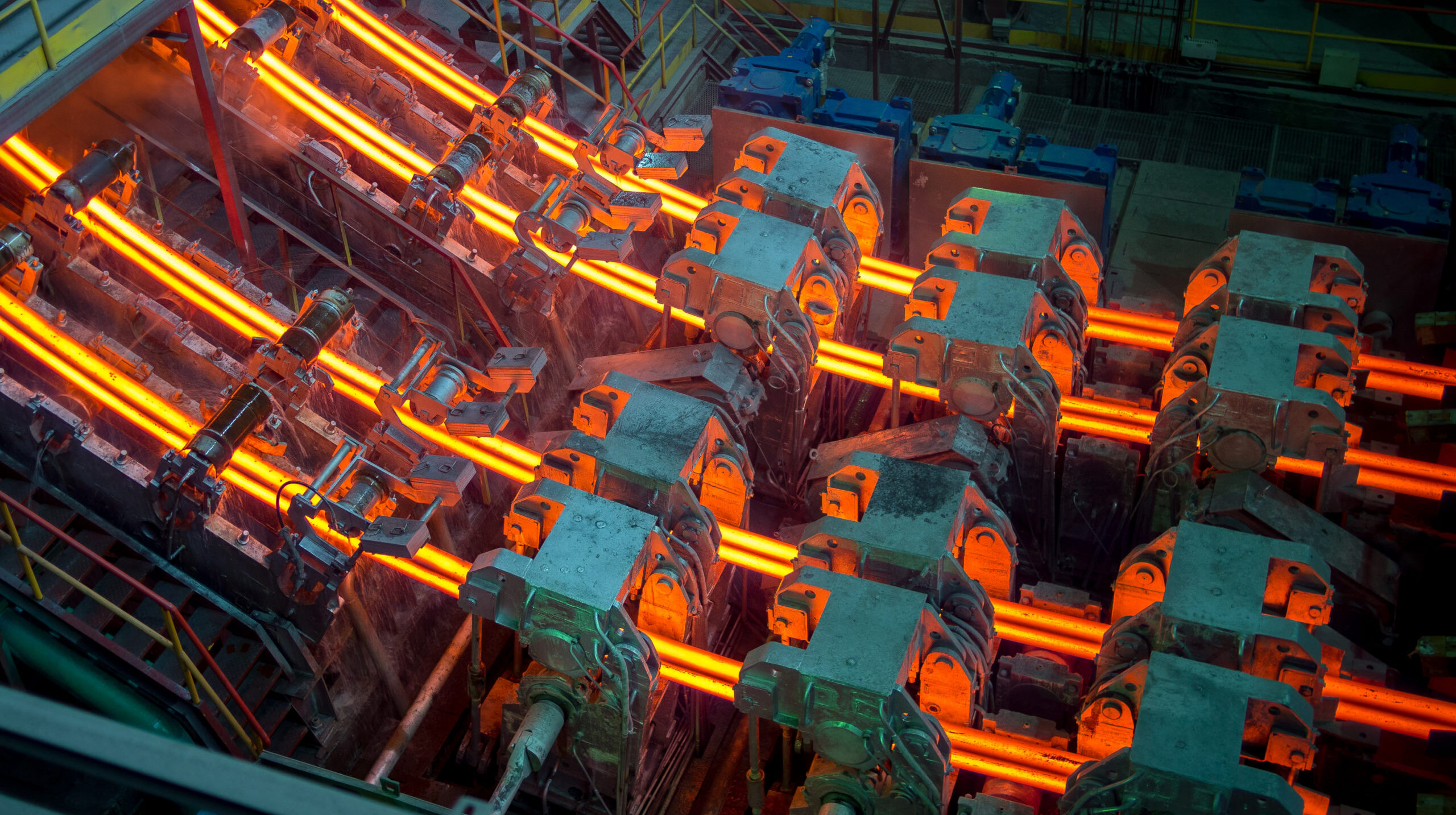
Silicon nitride, zirconia, and alumina ceramic offer outstanding refractory properties and thermal stability.
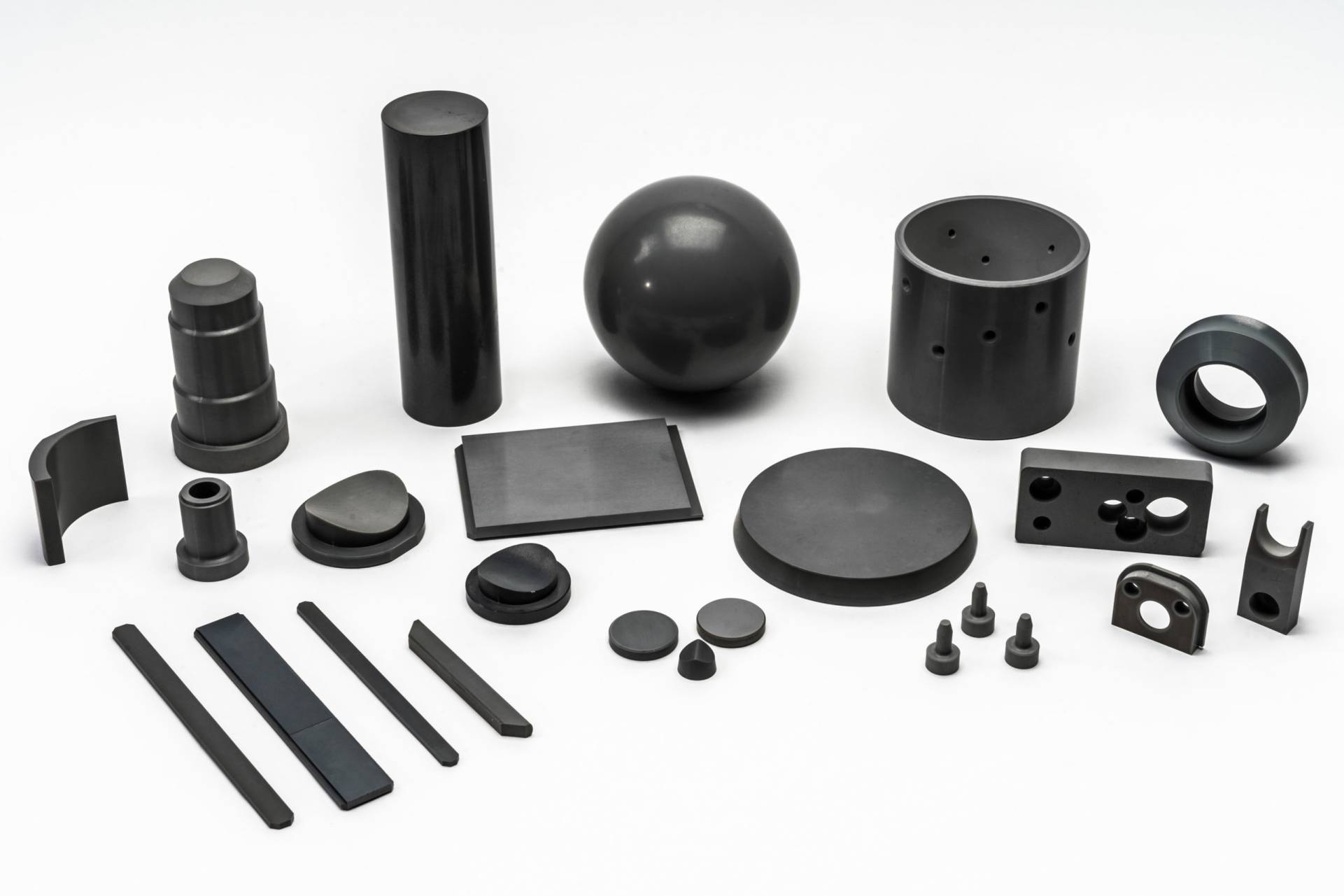