FOUNDRY APPLICATIONS
Foundry engineering is a complex process. It requires careful attention to performance, cost-effectiveness, material compatibility, environmental conscientiousness, and regulatory compliance. Silicon nitride and sialon ceramics, with their high thermal conductivity and impressive melting point, qualify as the ideal foundry product solution on multiple fronts. Offering high performance in the long term, Si3N4 materials meet the needs for iron and steel ladles through vacuum degassing, making them perfect for ferrous metal casting.
International Syalons has supplied world-leading advanced ceramic systems to ferrous and non-ferrous foundries, including semiconductor and automotive foundries, across the globe for years. Our silicon nitride and sialon foundry products are particularly renowned for their outstanding chemical stability in contact with molten metal, especially pure aluminium. We aim to deliver high-quality metal handling products that eclipse the service lifetime of conventional systems, such as chill cast iron, silicon carbide, or aluminium titanate. With enhanced durability in extreme heat and corrosive atmospheres, Si3N4 ceramics promote greater uptime, more use cycles, and higher throughput in ferrous castings. These include thermocouple protection sheaths; heater and riser tubes; ladles; primary and secondary aluminium smelters; holding furnace furniture; and cast house filter boxes.
Syalon 101, with its light weight and low coefficient of thermal expansion, is a standout choice for molten metal handling systems. Its exceptional thermal shock resistance, derived from its high strength and temperature gradient management, ensures the durability and longevity of your aluminium products. Moreover, the material's extreme resistance to corrosion by non-ferrous metals, especially aluminium and zinc, guarantees a pure, uncontaminated melt. The added advantage of Syalon 101 is its non-wetting properties for most non-ferrous metals, which translates to minimal dross build-up and subsequently reduced maintenance efforts and costs. Coupled with its inherent thermal stability, Syalon 101 promises consistent performance, making it an efficient and cost-effective solution for foundry applications.
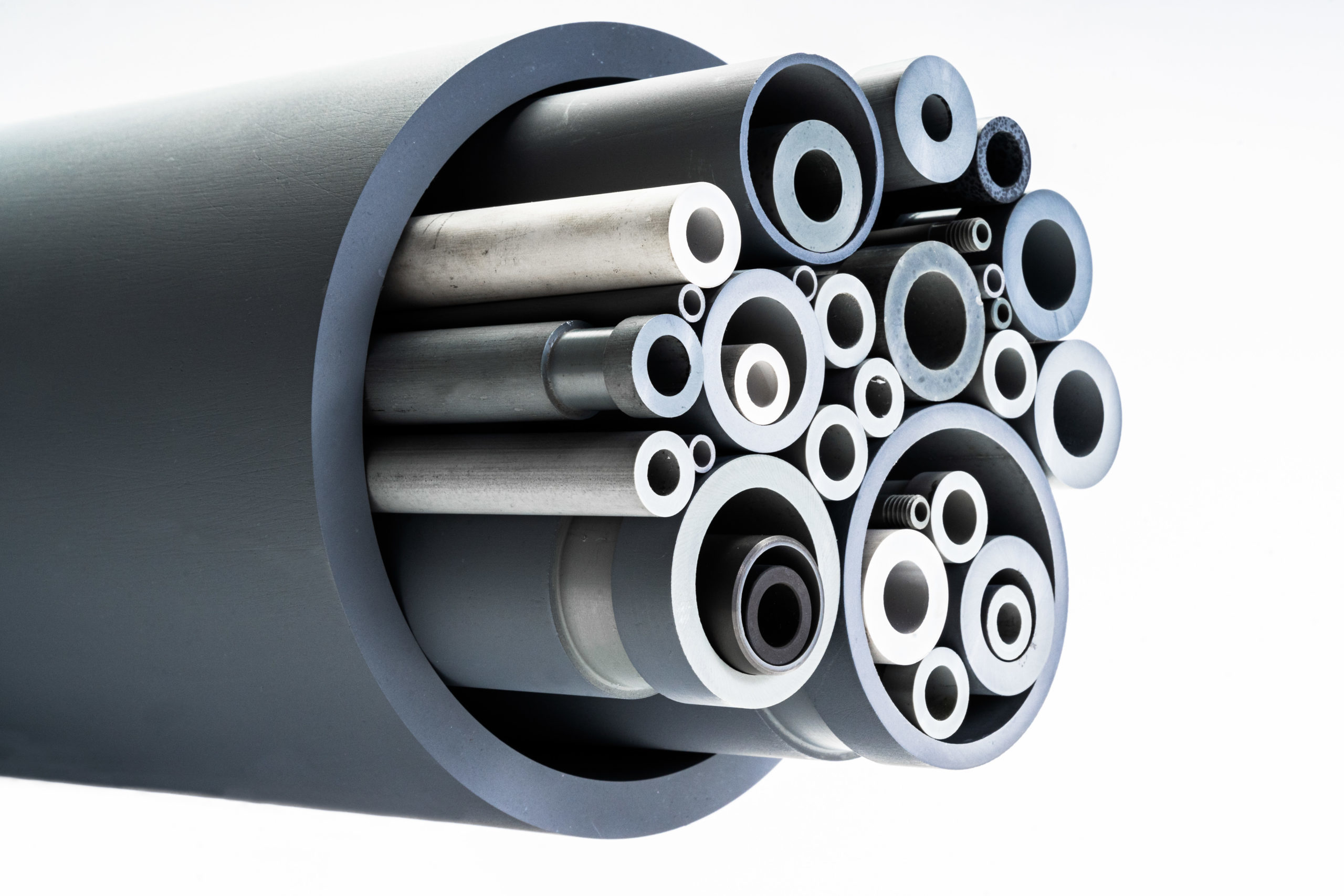
Syalon 101 thermocouple protection sheaths are becoming the industry standard in non–ferrous metal foundries. They possess outstanding thermal shock resistance, high thermal conductivity, are non–wetting, and suffer no degradation in contact with aluminium and its casting alloys.
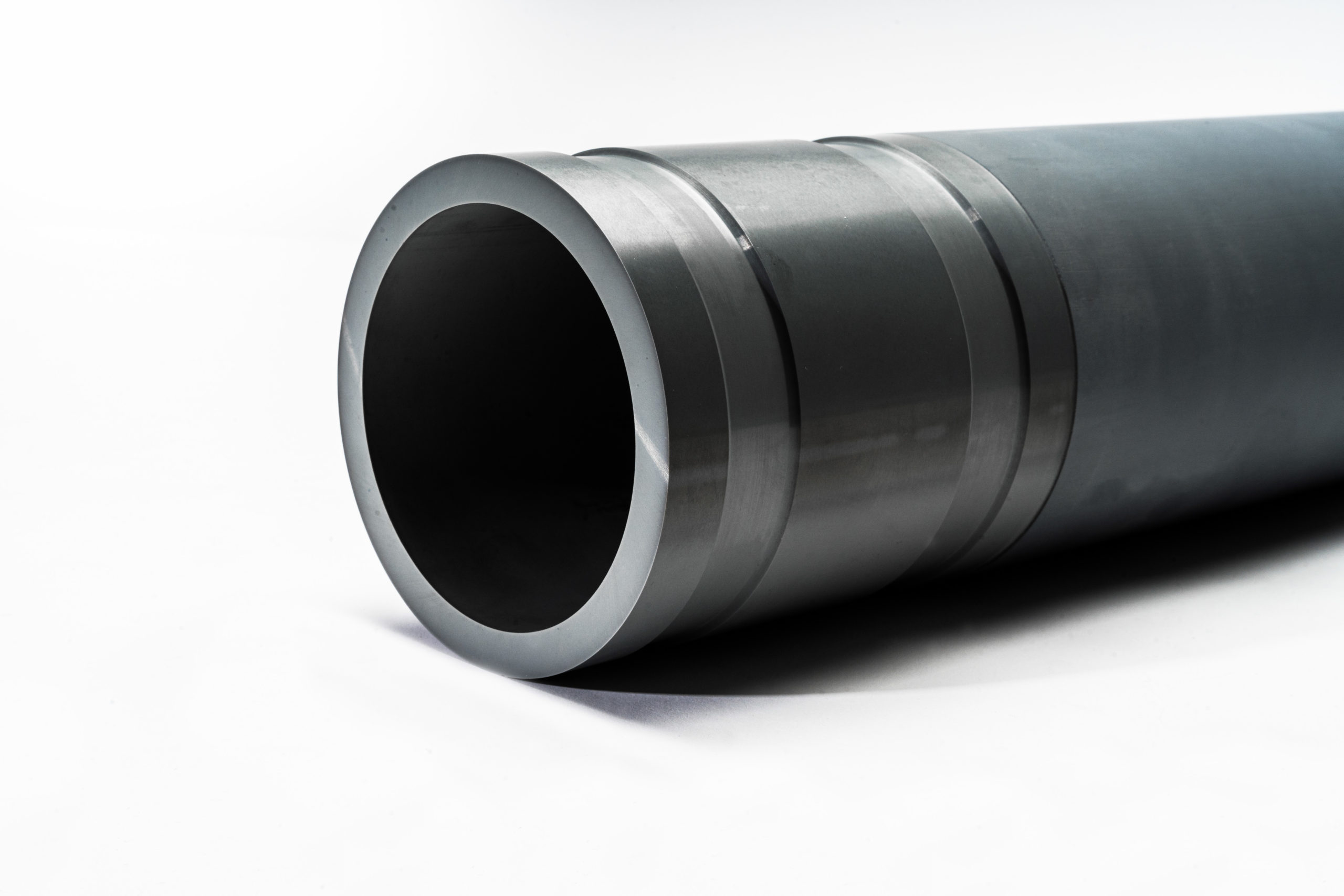
The benefits of Syalon 101 for thermocouple sheaths apply equally to heater and riser tubes. International Syalons manufacture a wide array of heater and riser tubes, which are often heat treated, to suit most requirements in the non–ferrous molten metal foundry business.
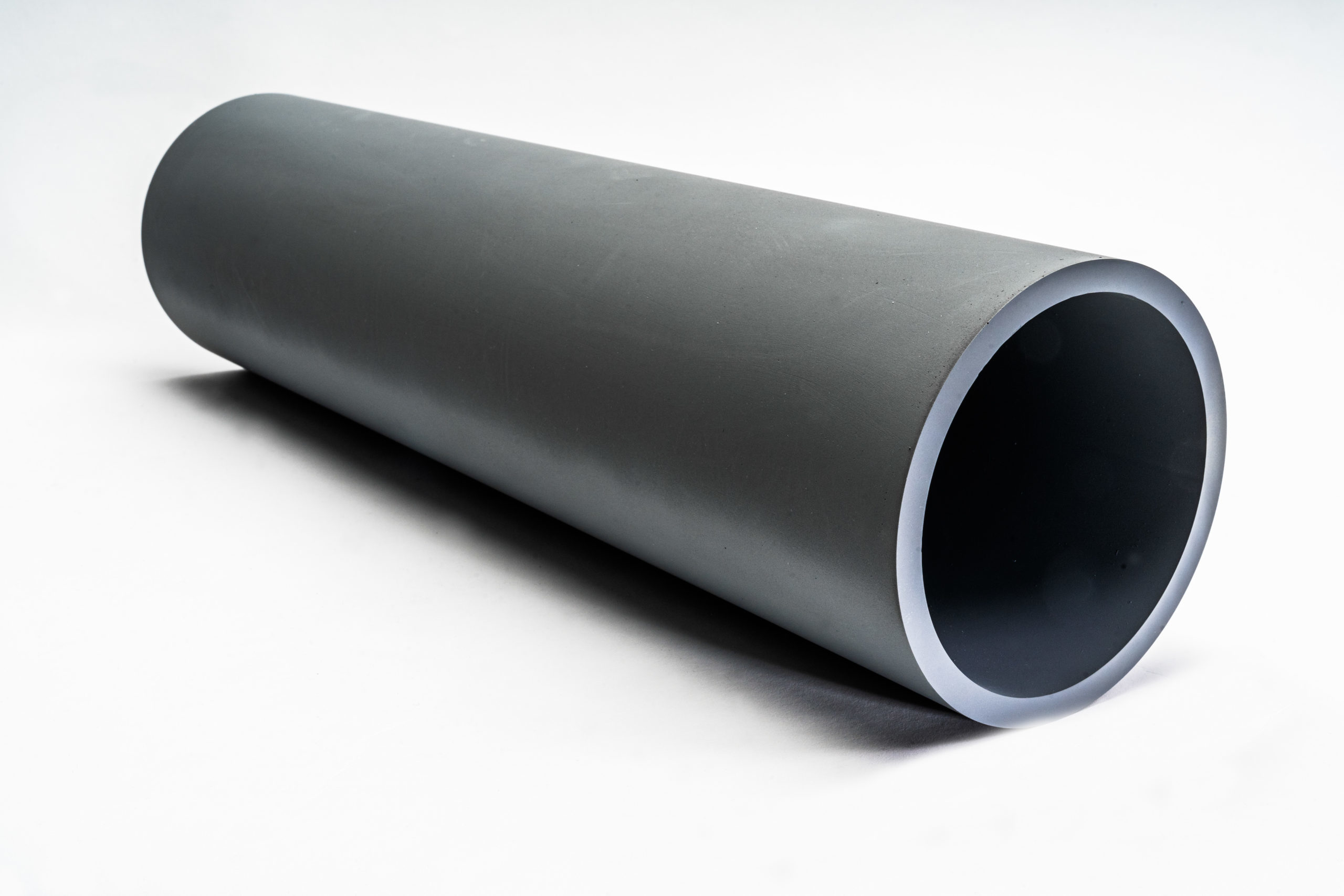
Silicon nitride and sialon riser tubes are used for precise, large capacity, high and low pressure die casting of aluminium products in many foundries and cast houses as they offer a greatly increased service lifetime over low-cost refractories.
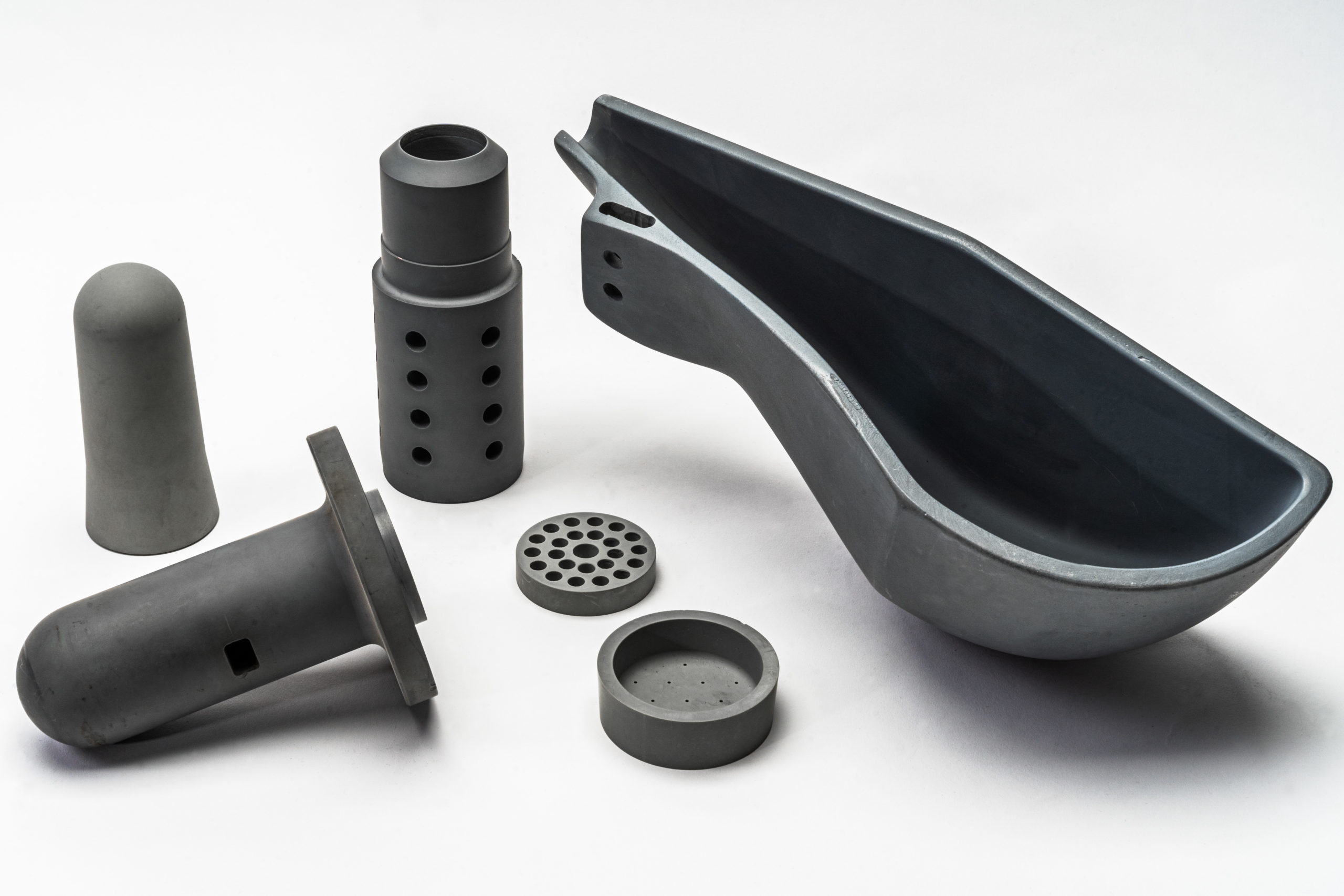
Sialon ceramic equipment, with its light weight properties, is often used for handling non–ferrous metals, such as aluminium alloys and zinc. Sialons are alloys of silicon nitride and are characterized by excellent thermal and chemical stability, making them ideal for these applications.
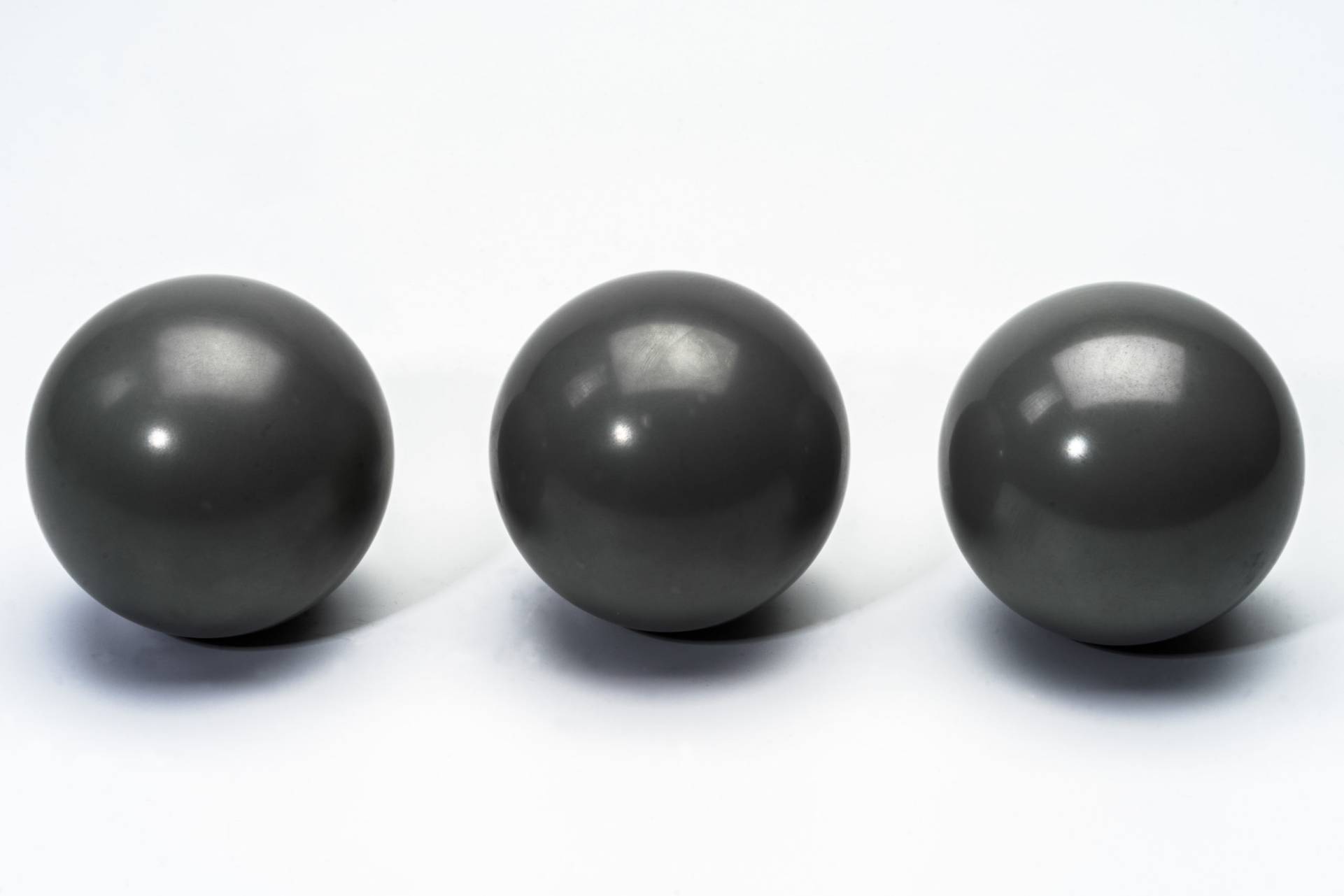
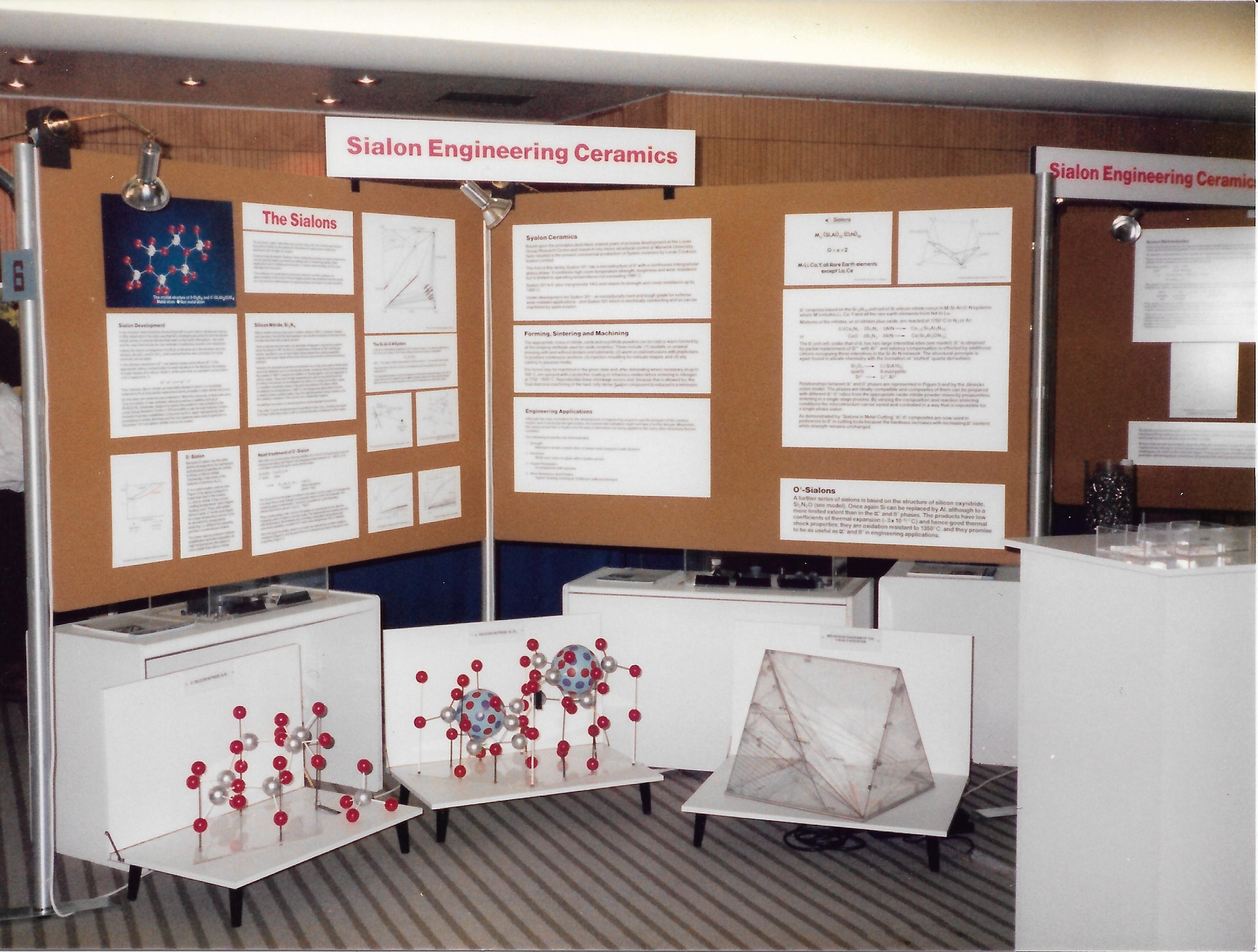
Explore the discovery of sialon ceramics
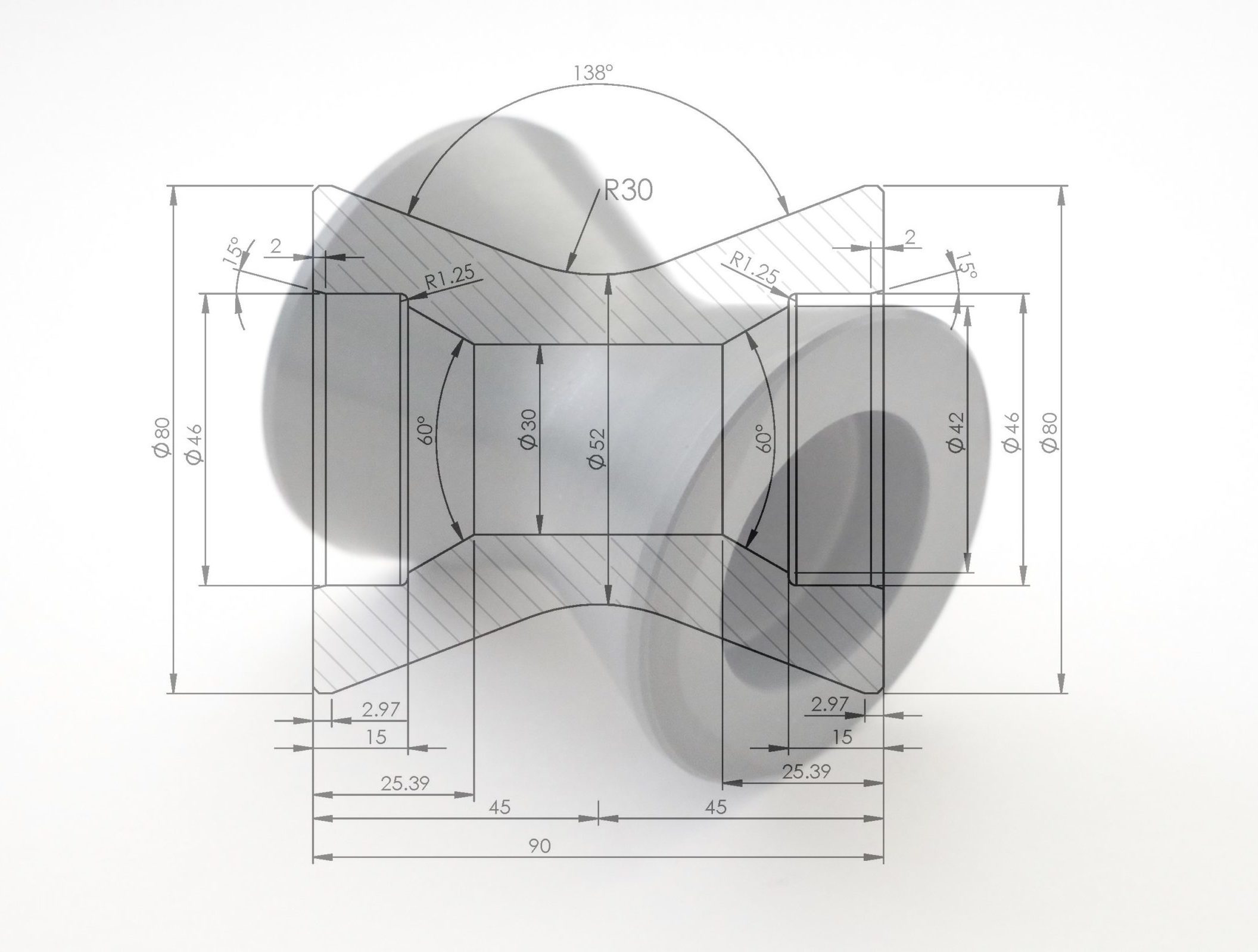
Learn how to design with ceramics
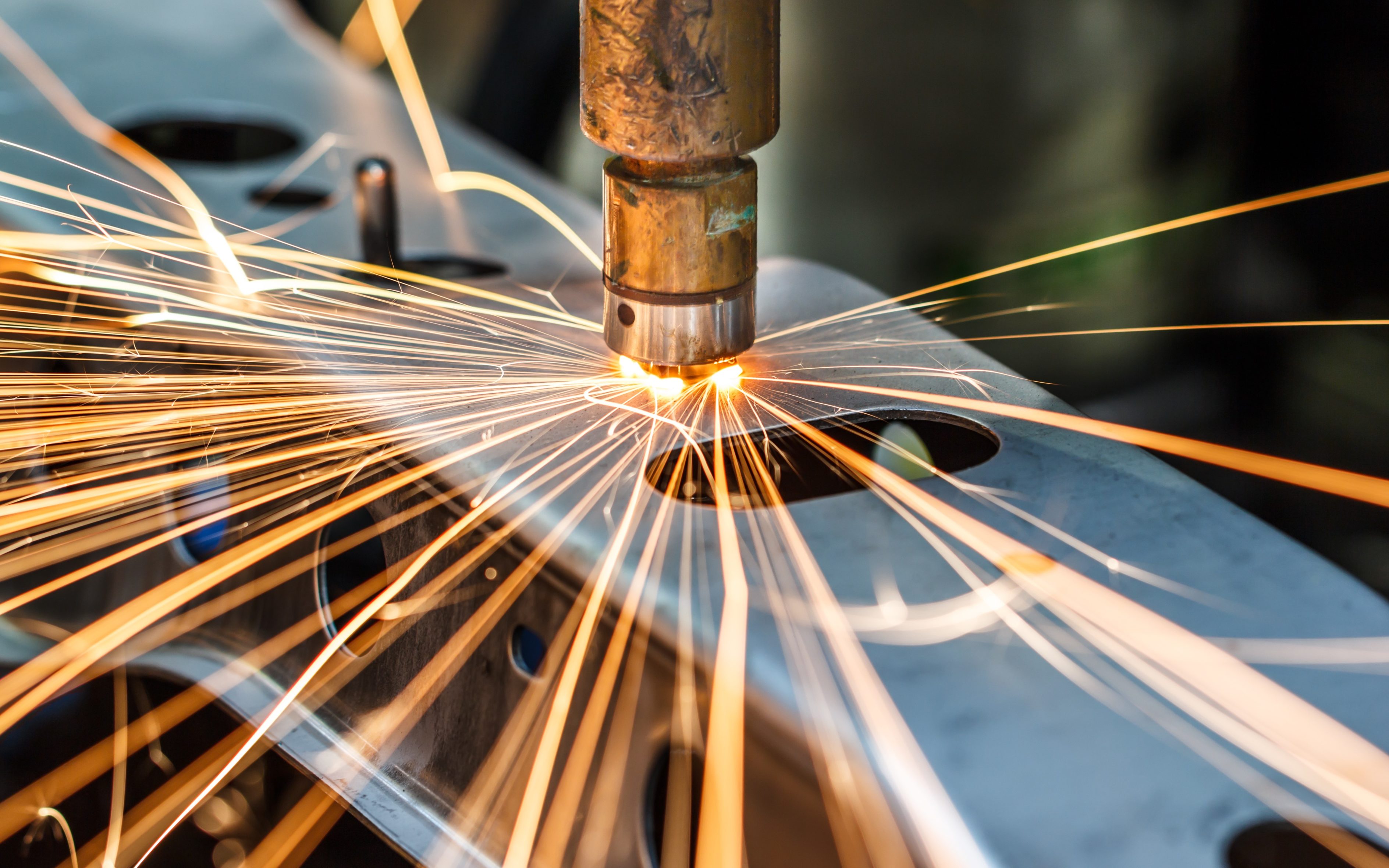
Sialon and zirconia provide the high temperature strength and non-wetting properties necessary for metal casting, extruding, and welding.
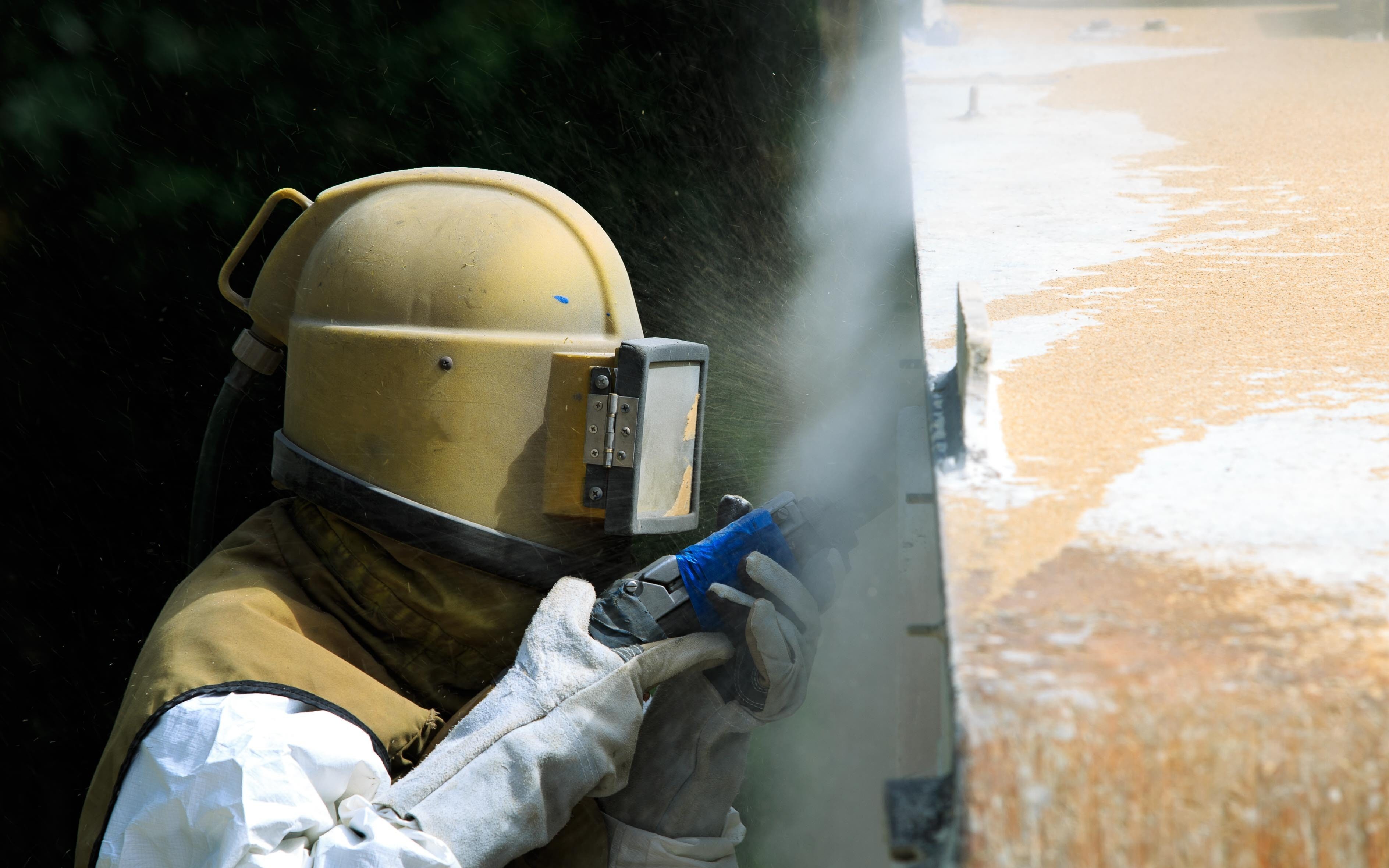
Technical ceramics are characterised by excellent mechanical strength and hardness, and are widely used in extreme wear applications.
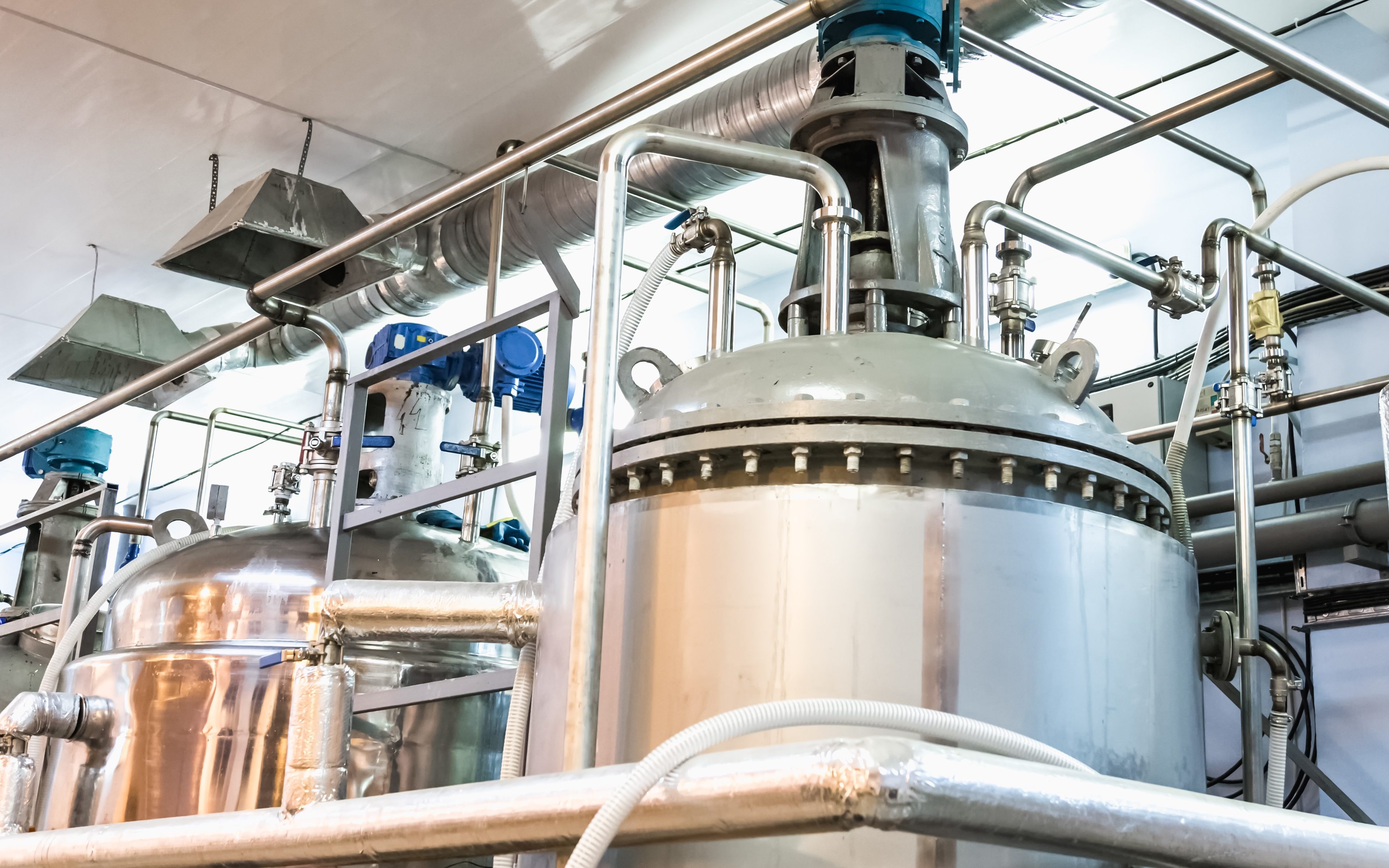
Silicon nitride offers excellent corrosion and thermal resistance and are ideal materials for use in the chemical and process industries.
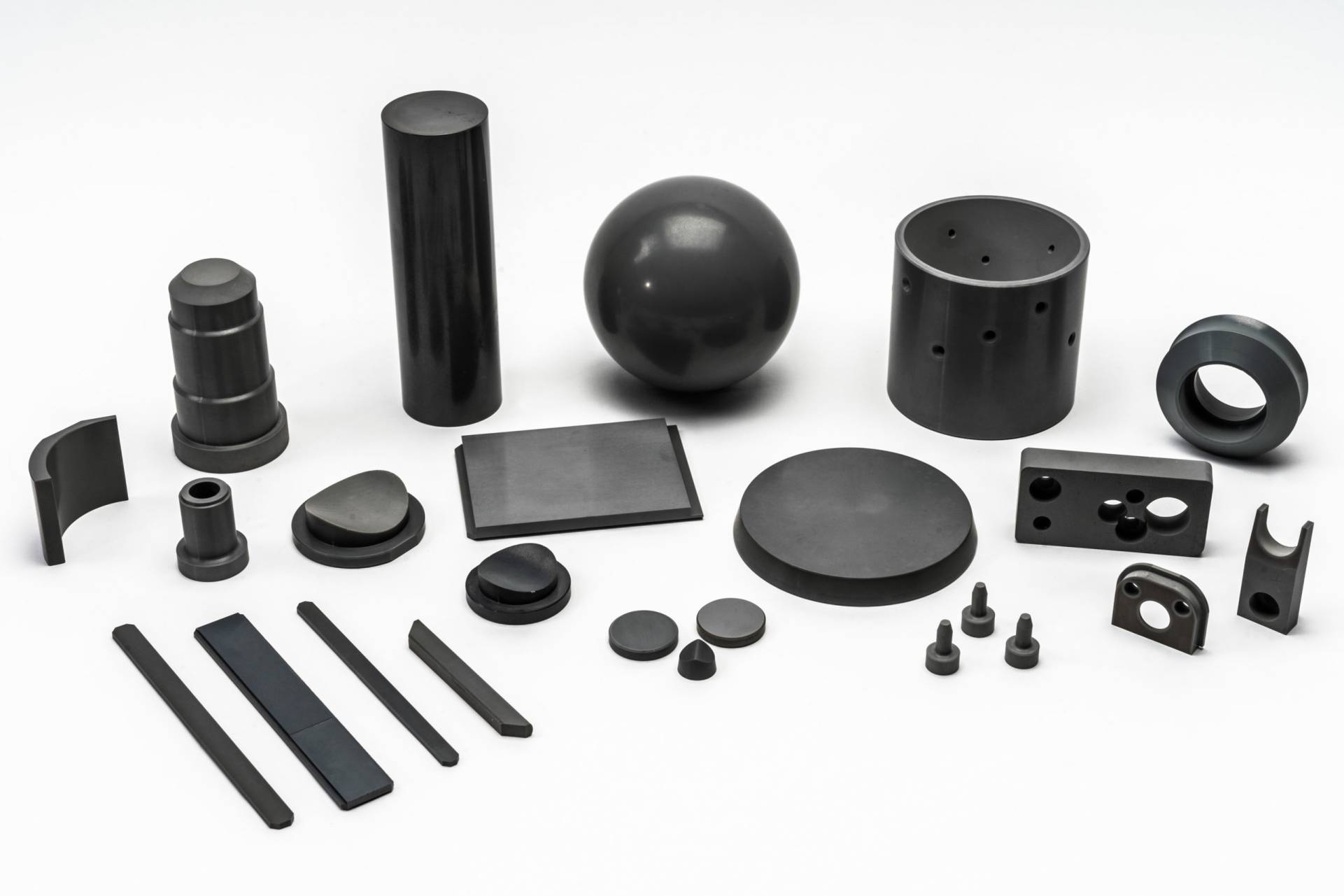